3D-Druck: Forscher entwickeln Material aus Holzabfällen
Bei der Holzverarbeitung entsteht auch Abfall, aus dem sich nichts mehr bauen lässt. Eine neue Recycling-Methode könnte das vielleicht bald ändern.
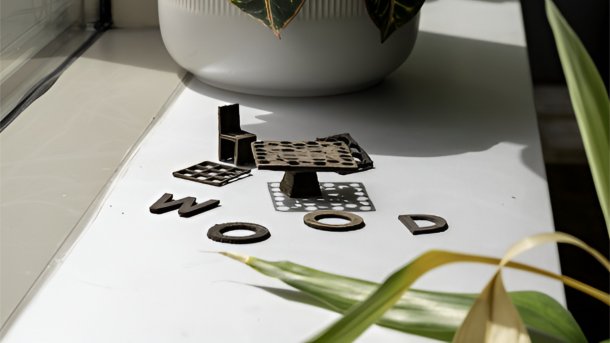
(Bild: Gustavo Raskosky/Rice University)
- Akos Fodor
An der privaten Rice University (Houston, Texas) hat ein Team von Forschern eine wasserbasierte Tinte aus Holzabfällen entwickelt, die sich für den 3D-Druck verwenden lässt. Mit dem recycelten Material will man zukünftig Teile für die Architektur oder Möbel herstellen. Im Rahmen der Forschungsarbeit ist es dem Team bereits gelungen, Objekte zu fertigen, deren Belastbarkeit sogar die von gewachsenem Holz übertrifft.
Als Zutaten dienen ausschließlich natürliche Zellulosefasern und -kristalle sowie Lignin im Nanomaßstab. Diese muss man im richtigen Verhältnis mit Wasser vermengen, damit sie sich per Direct-Ink-Writing (DIW) bei Zimmertemperatur verarbeiten lassen. Das Verfahren ähnelt dem Fused-Deposition-Modelling (FDM), nur schichtet der 3D-Drucker statt eines thermoplastischen Filaments eine zähflüssige Masse. Für die Versuche kam ein Hyrel Engine HR zum Einsatz, den man normalerweise für Bioprinting, also das Drucken von organischem Zellstoff verwendet. Entsprechend klein fallen die bisherigen Modelle aus.
(Bild: science.org/ Rice University)
Nach dem Drucken werden Modelle zunächst mit Trockeneis und dann zwei Tage lang bei -85 °C gefriergetrocknet. Schließlich erhitzt man sie noch einmal für etwa 20 Minuten auf 180 °C, damit das Lignin die Fasern verholzt und die Teile fest werden lässt.
Die Festigkeit von gewachsenem Holz erreicht das Gemisch zu diesem Zeitpunkt allerdings noch nicht. Durch das Zerkleinern des Zellstoffs sind nämlich die länglichen Fasern verloren gegangen, die Holz von Natur aus besitzt und die essenziell für dessen Stabilität und Flexibilität sind.
Um das zu kompensieren, haben die Forscher die Drucke daher versuchsweise (einfach und mehrfach) gepresst, bevor sie sie erhitzt haben. Mit dieser Nachbearbeitung konnte das Team Klötzchen herstellen, die in Druckfestigkeits- und Biegetests sogar vielfach robuster waren, als Stücke aus Balsaholz. Diese Technik ermöglicht bisher allerdings nur sehr einfache (und pressbare) Formen.
(Bild: science.org/ Rice University)
Wie im wissenschaftlichen Paper auf science.org beschrieben steht, könne man zukünftig damit experimentieren, längere oder andere Fasern in die Tinte einzuarbeiten. Und auch sonst gibt es noch einige Fragen, die man klären muss, wenn man das Projekt skalieren will, z.B. wie sich Überhänge in größerem Maßstab realisieren lassen. Dennoch finden wir den nachhaltigen Ansatz und die bisherigen Ergebnisse schon jetzt vielversprechend.
(akf)