Neues Verfahren gewinnt 2,6 Gramm Eisen aus Rotschlamm
Forscher extrahieren Eisen aus giftigem Rotschlamm, der bei der Aluminiumproduktion anfällt. Doch noch ist das Vorgehen sehr energieintensiv.
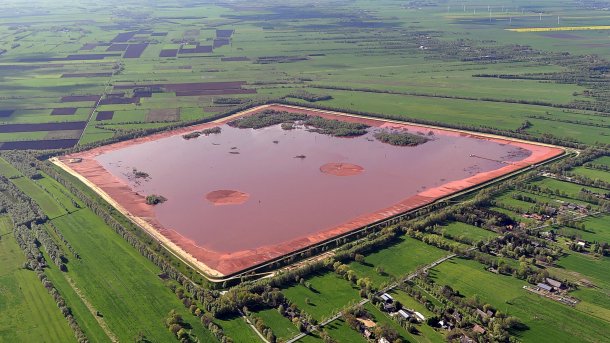
Rotschlamm-Becken des ehemaligen Vereinigte Aluminium-Werks Stade.
(Bild: Wikimedia Commons / cc by-sa 3.0)
- John Timmer
- Ars Technica
Seltene Erden, Lithium, Kupfer und auch Eisen: Auf Metalle wie diese bilden die Grundlage der modernen Gesellschaft, verursachen aber auch eine Reihe von Problemen. Die Trennung der von uns gewünschten Metalle von anderen Mineralien ist oft energieintensiv und kann große Mengen giftiger Abfälle hinterlassen. Um sie in reiner Form zu erhalten, ist oft ein zweiter, erheblicher Energieaufwand erforderlich, der die damit verbundenen Kohlenstoffemissionen in die Höhe treibt.
Ein Team vom Max-Planck-Institut für Eisenforschung hat nun herausgefunden, wie einige dieser Probleme für eine bestimmte Klasse von Bergbauabfällen, die bei der Aluminiumproduktion anfallen, gelöst werden können. Ihre Methode stützt sich auf Wasserstoff und Elektrizität, die beide aus erneuerbaren Energien gewonnen werden können, und extrahiert Eisen und möglicherweise andere Metalle aus den Abfällen. Was zurückbleibt, ist zwar immer noch giftig, aber nicht mehr so umweltschädlich. Die dazugehörige Studie haben sie in "Nature" veröffentlicht.
Rotschlamm mit giftigen Stoffen
Der erste Schritt bei der Aluminiumherstellung ist die Isolierung des Aluminiumoxids von den anderen Bestandteilen des Erzes. Zurück bleibt ein Material, das als Rotschlamm bekannt ist; man schätzt, dass jährlich fast 200 Millionen Tonnen davon produziert werden. Die rote Farbe stammt von den vorhandenen Eisenoxiden, aber der Schlamm enthält noch viele andere Stoffe, von denen einige giftig sein können. Und der Prozess der Isolierung des Aluminiumoxids hinterlässt einen sehr basischen pH-Wert.
All diese Eigenschaften bedeuten, dass der Rotschlamm im Allgemeinen nicht in die Umwelt zurückgegeben werden kann (oder zumindest nicht sollte). Er wird in der Regel in Auffangbecken aufbewahrt, in denen weltweit schätzungsweise 4 Milliarden Tonnen Rotschlamm lagern. Und viele Auffangbecken sind im Laufe der Jahre geplatzt.
Die Eisenoxide können an manchen Orten mehr als die Hälfte des Gewichts des Rotschlamms ausmachen, was ihn zu einer guten Eisenquelle machen könnte. Bei der traditionellen Verarbeitung von Eisenerzen werden diese mit Kohlenstoff zur Reaktion gebracht, wobei Kohlendioxid freigesetzt wird. Es gibt jedoch Bestrebungen, eine "grüne Stahlproduktion" zu entwickeln, bei der dieser Schritt durch eine Reaktion mit Wasserstoff ersetzt wird, wobei Wasser als Hauptnebenprodukt übrig bleibt. Da Wasserstoff mithilfe von erneuerbarem Strom aus Wasser hergestellt werden kann, hat dies das Potenzial, einen Großteil der mit der Eisenherstellung verbundenen Kohlenstoffemissionen zu vermeiden.
Doch zurück zum Max-Planck-Team: Die Forschenden wollten eine Methode zur Herstellung von grünem Stahl an Rotschlamm zu testen. Sie erhitzten einen Teil des Materials in einem elektrischen Lichtbogenofen unter einer Atmosphäre bei 900 mbar, die hauptsächlich aus Argon (das mit nichts reagiert) und Wasserstoff (mit 10 Prozent der Mischung) bestand.
Eisen (heraus)pumpen
Die Reaktion verlief bemerkenswert schnell. Innerhalb weniger Minuten bildeten sich in der Mischung metallische Eisenknollen. Die Eisenproduktion war nach etwa 10 Minuten weitgehend abgeschlossen. Das Eisen war bemerkenswert rein, etwa 98 Gewichtsprozent des Materials in den Knollen waren Eisen.
Ausgehend von einer 15-Gramm-Probe Rotschlamm reduzierte das Verfahren diese Menge auf 8,8 Gramm, da ein Großteil des Sauerstoffs im Material in Form von Wasser freigesetzt wurde. (Dieses Wasser könnte in die Wasserstoffproduktion zurückgeführt werden, wodurch sich der Kreislauf in diesem Aspekt des Prozesses schließen würde). Von diesen 8,8 Gramm lagen etwa 2,6 Gramm (30 Prozent) in Form von Eisen vor.
Die Forscher fanden heraus, dass in der Mischung auch einige kleine Stücke relativ reinen Titans enthalten sind. Es besteht also die Möglichkeit, dass dieses Gemisch für die Herstellung weiterer Metalle verwendet werden kann, obwohl der Prozess wahrscheinlich optimiert werden müsste, um die Ausbeute an anderen Metallen als Eisen zu erhöhen.
Gute Nachrichten und Nachteile
Die gute Nachricht ist, dass man sich danach um viel weniger Rotschlamm kümmern muss. Je nachdem, woher das ursprüngliche aluminiumhaltige Erz stammt, kann ein Teil davon relativ hohe Konzentrationen an wertvollen Stoffen enthalten, zum Beispiel seltene Erden. Der Nachteil ist, dass alle giftigen Stoffe im ursprünglichen Erz wesentlich stärker konzentriert sind.
Als kleines Plus neutralisiert das Verfahren auch den pH-Wert der verbleibenden Rückstände. Man muss sich also zumindest um eine Sache weniger Sorgen machen.
Der Nachteil ist, dass das Verfahren unglaublich energieintensiv ist, sowohl bei der Herstellung des benötigten Wasserstoffs als auch beim Betrieb des Lichtbogenofens. Die Kosten für diese Energie machen die Sache wirtschaftlich schwierig. Dies wird teilweise durch die niedrigeren Verarbeitungskosten ausgeglichen – das Erz wurde bereits gewonnen und hat einen relativ hohen Reinheitsgrad.
Das wichtigste Merkmal sind jedoch die extrem niedrigen Kohlenstoffemissionen. Derzeit gibt es in den meisten Ländern keinen Preis für diese Emissionen, was die Wirtschaftlichkeit dieses Prozesses erheblich erschwert.
Der Artikel erschien ursprünglich bei Ars Technica.
(jle)