Modi Vivendi
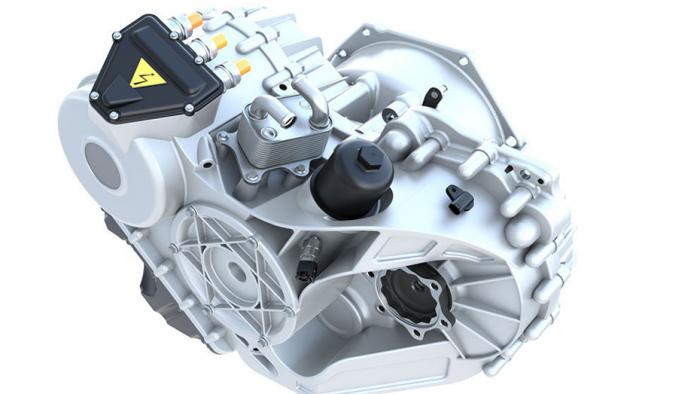
Sparsamer als Toyotas HSD? Der Ingenieursdienstleister AVL List aus Graz hat ein multimodales Hybrid-Getriebe mit einer Elektromaschine und drei fixen Übersetzungen entwickelt, das mit einem überaus elastisch ausgelegten Verbrennungsmotor höchste Effizienz erreichen soll
Graz/A, 30. April 2015 – Der Ingenieursdienstleister AVL List aus Graz hat ein multimodales Hybrid-Getriebe mit einer Elektromaschine und drei fixen Übersetzungen entwickelt, das mit einem überaus elastisch ausgelegten Verbrennungsmotor höchste Effizienz erreichen soll. Der Kraftverteiler für Klein- und Kompaktwagen soll mindestens zehn Prozent günstiger sein als vergleichbare Angebote auf dem Markt, konkreter Vergleichspartner: der bestens etablierte Hybridantrieb von Toyota.
Neun Gangstufen sind längst in Serie für Standard- und quer eingebaute Antriebe, Volkswagen kündigte unlängst ein zehnstufiges Doppelkupplungsgetriebe für den VW Touareg ab 2016/17 an. Um die zehn Gänge dürfte für Pkw ein vorläufiger Höhepunkt bleiben, denn darüber überwiegen Kosten- und Gewichtsnachteile die Verbrauchseinsparung. Eine Senkung der Übersetzungsverhältnisse können wir dagegen bei hybridisierten Antrieben erwarten, wie die Entwicklung der AVL zeigt.
Die Vermehrung der Gangstufen
Wenn sich Carl Benz in seinen von seinem Schwiegersohn verfassten Memoiren richtig erinnert, begann die Vermehrung der Gänge bereits kurz nach der Patentierung des ersten Automobils. Dort heißt es, dass seine Gattin Bertha sich nach ihrer eigenmächtigen Eskapade von Mannheim nach Pforzheim und zurück im August 1888 mit dem Motorwagen einen weiteren Gang zu den beiden bereits vorhandenen gewünscht habe, damit man am Berg nicht immer schieben müsse. Laut technischer Daten hatte der Wagen zwar nur eine feste Übersetzung und die später produzierten Patent-Motorwagen mit 2,5 und drei PS zwei Gänge, aber das ändert ja nichts an der Tatsache.
Der Grund liegt in der Eigenschaft von Kolbenkraftmaschinen mit innerer Verbrennung, ihr Drehmoment mit der Drehzahl auf- und danach wieder abbauen. Im Gegensatz zu Elektromotoren oder Dampfmaschinen benötigt man also zusätzlich eine Kupplung als Anfahrelement und verschiedene Übersetzungen, die es ermöglichen, die Geschwindigkeit mit dem nutzbaren Drehzahlbereich einigermaßen synchronisieren zu können – oder umgekehrt die Kraft an den Antriebsrädern den Erfordernissen anzupassen. Dazu haben noch bis in die 60er-Jahre, beispielsweise beim damals hier überaus beliebten Opel Kapitän, drei Gänge genügt. Aktueller Standard: eine knappe Verdopplung.
Noch mehr Gangstufen und eine weitere Spreizung zwischen unterster und oberster Stufe können das Auto noch etwas sparsamer machen. Denn genau betrachtet ist der Verbrennungsmotor bei einer bestimmten Leistung sogar nur bei einer Kombination aus Last und Drehzahl optimal effizient. Bei wechselnden Leistungsanforderungen (die Regel im Auto) muss also die Drehzahl angepasst werden können. Die heutigen Getriebe mit bis zu neun Gängen im Pkw, wie das ZF 9HP [1] (und noch deutlich mehr im Lkw) spiegeln das Bemühen, den Motor möglichst oft in diesem Verbrauchs-Bestpunkt halten zu können. Neun Gangstufen klingt nach viel – und ist es auch. Im Pkw gelten Getriebe mit noch mehr Gängen als nicht mehr sinnvoll, weil jeder weitere Zugewinn von den mechanischen Verlusten im Getriebe überwogen würde. Ideal wäre es, die Übersetzung kontinuierlich variabel anzupassen, um bei jeder Verschiebung von Last und Drehzahl die passende Drehzahl stufenlos einregeln zu können. Das gibt es bereits, stellt aber das Gefühlsempfinden vieler vor allem deutscher Autofahrer nicht zufrieden.
Anschubsen in Effizienzproblemzonen
Wichtiger noch als Geschmacksfragen ist heute die Effizienz – und daher kommen seit einiger Zeit Elektromotoren ins Spiel. In Hybridfahrzeugen helfen sie dem Verbrennungsmotor dazu über seine Schwächephasen und Effizienzproblemzonen hinweg. So kann beispielsweise die E-Maschine mit vollem Drehmoment ab Stillstand den Wagen ohne Getriebe und Kupplung aus dem Stand anschubsen und den Verbrennungsmotor erst starten, wenn sein Einsatz sinnvoll ist. Bis zu dessen Bestpunkt kann ihn je nach Anforderung eine E-Maschine bei der weiteren Beschleunigung unterstützen. Zudem kann mit so einer variablen Kombination die Ladung der Traktionsbatterie berücksichtigt und in allen Bereichen auch stufenlos Strom rekuperiert werden.
Parallel arbeitende Aggregate wie etwa bei Volkswagens Golf GTE mit seiner fest zwischen Verbrennungsmotor und 6-Gang-Doppelkupplungsgetriebe eingebauter E-Maschine, sind dazu nur begrenzt in der Lage. Mit einem Planetenradsatz dagegen ermöglicht ein Getriebe eine so genannte Leistungsverzweigung zur Steuerung der Drehzahlen zwischen zwei E-Maschinen und dem Verbrennungsmotor. Die Verzweigung ermöglicht zudem rein elektrischen Antrieb, Fahren ausschließlich mit dem Verbrennungsmotor oder mit allen Motoren gleichzeitig.
Um die Drehmomentcharakteristik von Brennkraft- und E-Maschine(n) als auch die unterschiedlichen Wirkungsgrade zu berücksichtigen, kann man ebenfalls per Planetenradsatz eine weitere Verzweigung vorsehen. Immerhin sinkt der Wirkungsgrad [2] der E-Maschine mit der Drehzahl beträchtlich – von 90 auf nur noch 70 Prozent. Dann erhält man ein sogenanntes Two-Mode Hybridsystem, in dem der Energiefluss über den elektrischen Zweig bei Bedarf stark verringert werden kann.
Wenn sich der Wagen beispielsweise konstant schnell auf der Autobahn bewegt, funktioniert das immer noch am sparsamsten mit der Kraft aus dem Verbrennungsmotor. Das kann auch das ECVT in Toyotas HSD, allerdings muss in ihm immer eine gewisse Menge elektrischer Energie vom Generator aufgebracht werden, um das Drehmoment des Verbrennungsmotors an der Stegwelle des Summiergetriebes durch das Drehmoment des Generators am Sonnenrad abstützen zu können.
Bekanntes neu kombiniert
Die mechanische Umsetzung eines Two-Mode Hybridsystems ist im Prinzip einfach, weil alle Maschinenbauelemente schon lang bekannt und im Automobilbau bewährt vorliegen. Nur ihre Kombination ist neu. Planetenradsätze arbeiten seit Jahrzehnten in Großserien-Automatgetrieben, lassen sich ohne Zugkraftunterbrechung durch Festbremsen mit Lamellenkupplungen weich umschalten und bieten zwei Freiheitsgrade pro Radsatz.
Man kann dazu sogar ein herkömmliches Wandlerautomatikgetriebe für den Einbau im Standardantrieb umrüsten, indem man anstelle der Lamellenbremsen E-Maschinen an zwei der Planetenradsätze anbringt. Die anderen Radsätze können genutzt werden, um die jeweils benötigten Übersetzungsverhältnisse zwischen allen drei Motoren festbremsen zu können. So hat das hat ein Konsortium aus Daimler, BMW und General Motors 2006 gemacht. Basis war die Mercedes-Benz 7G-Tronic mit dann sechs Betriebsarten (EVT mit einfacher respektive zweifacher Kraftverzweigung plus vier festen Gangstufen mit je einem oder beiden aktivierten E-Maschinen). Wie viele feste Übersetzungen erhalten bleiben sollen, ergibt sich letztlich aus den Anforderungen des Gesamtlayouts und der Breite der Betriebs„punkte“ beim Verbrennungsmotor.
Im multimodalen Kraftverteiler für Quermotoren vom Ingenieursdienstleister AVL aus der Hightech-Hochburg Graz reichen drei fixe Übersetzungen für den Verbrennungsmotor, der durch seine Auslegung ein breites Leistungsplateau bietet. Die Ingenieure nutzen die von Hause aus fülligere Drehmomentkurve eines Dreizylinder-Ottomotors, den sie mit den üblichen Downsizing-Maßnahmen Turboaufladung, Benzindirekteinspritzung, gekühlter Niederdruck-Abgasrückführung und Reibungsreduktion sehr aufwendig in seiner Effizienz ertüchtigt haben. Zudem lassen sie ihn im verbrauchseffizienten Miller-Zyklus laufen, also mit einem per Steuerzeiten verkürzten Verdichtungshub, um im Verhältnis den Expansionshub zu verlängern. Das überrascht auf den ersten Blick angesichts des Ziels eines besonders breiten Drehmomentbands, denn damit kappt man die Kraft bei niedrigen Drehzahlen. Doch ist hier in Anbetracht der Gesamteffizienz ohnehin nötige elektrische Schubhilfe so berechnet, dass der Gesamtvorteil überwiegt.
Nur eine E-Maschine
Die Bescheidenheit bei der Anzahl der Gänge wird mit geringerem Gewicht, kleineren Reibungsverlusten und einfacherem Aufbau belohnt. Wert legen die Ingenieure auch darauf, nur eine E-Maschine zu verwenden, was das zusätzlich die Kosten senken helfen soll. Schließlich wollte man es mindestens zehn Prozent günstiger produzieren können als vergleichbare Angebote auf dem Markt.
Das Getriebe nutzt ein verbreitetes Radsatzkonzept nach Lepelletier, also einen einfachen Planetenradsatz mit nachgeschaltetem Ravigneaux-Radsatz, wie man es aus aktuellen Sechsgang-Wandlergetrieben kennt. Wegen des beengten Raumangebots beim Quereinbau wurde die E-Maschine auf eine eigene, achsparallele Ebene verlegt, von wo aus die Kraft per Räderkaskade über das zusätzliche Hohlrad des Ravigneaux-Radsatzes auf die Getriebewelle (und umgekehrt) übertragen werden kann.
Vier Schaltelemente, eine Bremse und drei Kupplungen ermöglichen drei Gänge für den Verbrennungsmotor und Fahrmodi mit Einbeziehung der 65 kW leistenden E-Maschine durch Boosten und Rekuperation. Dazu kommen zwei rein elektrische Fahrmodi und zwei Betriebsbereiche, in denen die E-Maschine die Übersetzungsverhältnisse kontinuierlich variiert.
Zwei Gänge für die E-Maschine
Zum rein elektrischen Fahren wird der Verbrennungsmotor direkt hinter seinem Schwungrad ganz ausgekuppelt. Für den ersten Gang ergibt sich mit zwei geschlossenen Lamellenkupplungen über beide Planetenradsätze eine Gesamtübersetzung von der E-Maschine zum Rad von 12,3. Im Zweiten beträgt mit nur einer geschlossenen Kupplung die Gesamtübersetzung 3,04. Welche der beiden Kupplungen in diesem Fall geschlossen (oder geöffnet) ist, spielt keine Rolle, was den Ingenieuren zusätzliche Freiheitsgrade bei der Steuerung ermöglicht.
Zwei Betriebsarten mit stufenloser Übersetzung
Drehmoment und Übersetzung können stufenlos durch die E-Maschine so eingeregelt werden, dass der Verbrennungsmotor im Bereich seines besten spezifischen Wirkungsgrads läuft. Die E-Maschine arbeitet dabei als Generator und liefert eine Leistung von mindestens 3,5 kW in das elektrische Hochvoltsystem des Fahrzeugs. Sie kann das in zwei verschiedenen Übersetzungsbereichen tun:
Im ersten Modus gibt der Verbrennungsmotor seine Kraft mit Sonnendrehzahl, im zweiten direkt als Stegdrehzahl über den Ravigneaux-Radsatz ab. Die gewünschte Abtriebsdrehzahl wird jeweils durch die E-Maschine eingeregelt, um den Dreizylinder im günstigsten Verbrauchsbereich zu halten. In beiden Fahrstufen ist es möglich, selbst bei leerer Batterie bergauf mit dem Verbrennungsmotor anzufahren. Bei ausreichender Batterieladung fährt das Fahrzeug aber grundsätzlich rein elektrisch an.
Drei konventionelle Modi
Weitere drei konventionelle Fahrmodi erlauben jeweils Boosten und Rekuperieren der E-Maschine beim Betrieb mit dem Verbrennungsmotor.
Welche der genannten Betriebsarten die effizienteste ist, hängt von den ständig wechselnden Bedingungen ab. Daher wählt die Steuerung die passende Strategie je nach Ladezustand der Batterie und der Kraftanforderung an den Antriebsstrang. Ein Beispiel wäre die Umschaltung auf den Betrieb mit dem Ottomotor ohne Umweg über den elektrischen Pfad ab etwa 120 km/h (je nach Auslegung und Fahrzeugröße), ein anderes das rein elektrische Anfahren aus dem Stand bei ausreichend gefülltem Stromspeicher. Dazwischen kann auf verschiedenen, jeweils der Situation gerechten Pfaden der Verbrennungsmotor unterstützt werden, Strom erzeugt oder Bewegungsenergie zurückgewonnen werden.
URL dieses Artikels:
https://www.heise.de/-2628998
Links in diesem Artikel:
[1] https://www.heise.de/autos/artikel/Innenvielzahn-1784562.html
[2] https://www.heise.de/autos/artikel/Doppelkupplungslos-mit-eDCT-1802337.html
Copyright © 2015 Heise Medien