Dreidimensionale Drucke im Prototypenbau
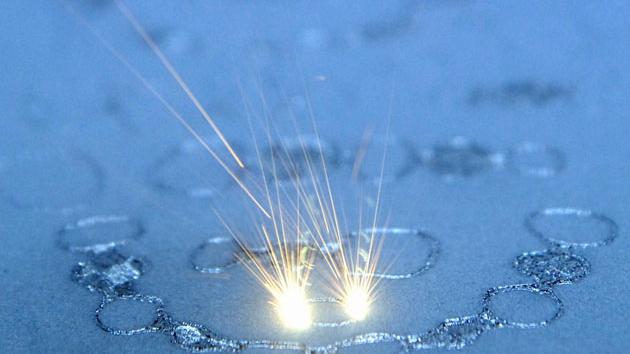
Moderne Methoden im Prototypenbau erzeugen Bauteile nahezu beliebiger Komplexität direkt aus CAD-Daten. Was dem Laien fast wie Zauberei erscheint, erspart den Entwicklern eine Menge Arbeit
Hannover, 31. August 2009 – Moderne Methoden im Prototypenbau erzeugen Bauteile nahezu beliebiger Komplexität direkt aus CAD-Daten. Dem Laien erscheint das fast wie Zauberei, und weil wir wissen, dass dies nach Clarke auf jede hinreichend fortgeschrittene Technologie zutrifft, beleuchten wir hier Rapid Prototyping am Beispiel BMW.
„Generative Fertigungsmethoden“
Nach den drögen Massenmodellen der Achtziger und Neunziger erscheinen die derzeitigen Wagen für die breite Mitte geradezu künstlerisch. Selbst Kleinwagen sind an allen Ecken und Enden bis in feine Details ausgestaltet. Ermöglicht wurde dies außer durch längere Leinen für Gestalter durch den in den Neunzigern aufgekommenen schnellen Prototypenbau, dessen Methoden man unter „Rapid Prototyping“ oder deutscher, korrekter unter „generative Fertigungsmethoden“ zusammenfasst. Letzteres deshalb, weil ein Großteil der Verfahren, ja praktisch alle wichtigen, im Schichtbetrieb arbeiten. Erinnern Sie sich noch an diese 3D-Puzzles Ihrer Kindheit, die aus einem Stapel verschieden konturierter Pappscheiben bestanden? Man spießte sie in der richtigen Reihenfolge auf und erhielt am Ende einen menschlichen Kopf, einen Globus oder andere Formen ohne Überhänge. Ähnlich geht es bei den generativen Fertigungsverfahren zu. Eines der ersten Verfahren arbeitete sogar fast exakt so; es schnitt per Schneideplotter die Schichten aus Papier aus, die übereinander am Ende das Werkstück ergaben. Papier setzte sich als Werkstoff für Prototypen jedoch nicht durch, sondern musste schnell Kunstharzen weichen. Auftritt der Stereolithographie.
Stereolithographie
Anfang der Neunziger kombinierte ein schlauer Ingenieur einen industriellen Laser mit einem Bad voll lichtaushärtendem Kunstharz und schuf damit die sogenannte Stereolithographie. Als einer der Urväter generativer Verfahren eignet es sich gut, um eben diese zu erklären. Es ist außerdem bis heute in vielen Bereichen immer noch in der Prototypenproduktion vorhanden, bei BMW steht zum Beispiel eine Maschine aus den frühen Neunzigern, die bis heute ausgelastet arbeitet. Grob betrachtet besteht die Maschine aus einer Plattform, die sich schrittweise ins Kunstharzbad absenkt, und aus einem Laserleitsystem.
Dreidimensionale Drucke im Prototypenbau
Der Laser zeichnet eine Struktur in die Flüssigkeit, die überall bei Kontakt verhärtet. Nachdem so eine Schicht fertig ist, senkt sich die Plattform eine Schichtdicke weit ab und der Prozess beginnt erneut für die nächste Schicht. Das noch flüssige Kunstharz ist dabei nichttragend, daher werden Werkstücke in der Stereolithographie bei Inseln oder zu starken Überhängen mit Stützstrukturen ausgegeben, die ein Arbeiter später entfernt. Stellen Sie sich zum Beispiel vor, ein Mediziner will die Nachbildung eines menschlichen Kopfes herstellen. Sobald der Laser die erste Schicht des Gaumenzäpfchens in das Bad schreibt, liegt es dort als eine Art Insel ungestützt frei und versinkt noch im Bau. Andere Stellen wie etwa die Nase haben zu große Überhangwinkel, sodass sich die neue Materialschicht verformen könnte.
Scheibchenweise
Die Stützstrukturen erstellt ein Operator mit Software-Hilfe bei der Aufbereitung der CAD-Ausgangsdaten. Bei BMW kommt wie häufig in der Autoindustrie die CAD-Suite CATIA zum Einsatz. Deren Modelle werden fürs Schichten durch einen Prozess aufbereitet, der passenderweise „Slicing“ heißt. Dem Namen entsprechend schneidet das Slicing-Programm dabei die Vektordaten in die für das jeweilige Verfahren benötigten Scheibchen. Vorher noch erhalten die Daten die beschriebenen Stützstrukturen – und um die Maschinen möglichst effizient zu bestücken, sollen möglichst viele Bauteile pro Prozess möglichst günstig liegen. Einen Handschuhfachdeckel kann die Maschine zum Beispiel liegend mit vielen Stützen fertigen oder senkrecht mit sehr wenigen. Auch für diesen Arbeitsschritt gibt es Algorithmen, die versuchen, möglichst effizient zu puzzlen, in der Praxis kommen diese allerdings meist nur zur Vorarbeit zum Einsatz, weil ein menschlicher Operator immer noch die besten Bestückungen macht – gerade im Hinblick auf den gesamten Arbeitsablauf. Das fertige, schichtweise aufbereitete Teilepuzzle als Datenmaterial heißt „Bau-Job“. Diesen arbeitet die Maschine in einigen Stunden ab, und der Operator fährt danach die Plattform aus dem Kunstharzbad, auf der jetzt die fast fertigen Teile stehen sollten. Diese werden unter UV-Licht komplett ausgehärtet, von Stützstrukturen befreit und sind damit fertig für den Einsatz.
Dreidimensionale Drucke im Prototypenbau
„Einsatz“ hieß zur Genesis der Stereolithographie zum großen Teil Messeprototypen, die hauptsächlich aus diesen Kunstharzteilen bestanden – lackiert, beklebt oder für Scheinwerfer und Co. durchsichtig. Die Anmutung war damit sehr realistisch, die Warnschilder „Bitte nicht anfassen“ standen jedoch mit Grund daneben, denn die eingesetzten Kunstharze können recht brüchig sein. Gelegentlich sahen Besucher aus der Nähe, dass ein Teil gebrochen und in einer Nachtschicht von einem verzweifelten Messearbeiter mit Klebstoff neu zusammengefrickelt worden war. Trotz der neueren Verfahren bleibt die Stereolithographie aktuell, zum Beispiel für transparente Teile.
Lasersintern
Die Methode mit dem vielleicht höchsten Teiledurchsatz bei BMW ist das selektive Lasersintern (SLS) in Kunststoffpulver. Analog zur Stereolithographie bestehen die SLS-Maschinen aus einem Laserleitsystem und einer schrittweise absinkenden Plattform, plus einem Rakel, einem Schieber oder einer Walze. Dieses Bauteil zieht eine Schicht frischen Substrats über die Arbeitsfläche, immer nachdem der Laser eine Schicht gezeichnet hat und die Plattform eine Etage tiefer gefahren ist. Der Laser strahlt unterschiedlich stark auf das Pulver ein, das unter der gebündelten Energie dann versintert oder verschmilzt. Das umgebende Pulver ist beim SLS derart dicht, dass Stützstrukturen entfallen. Wer den Bau-Job vorbereitet, hat also nur die Aufgabe, möglichst viele Teile in einen Job zusammenzufassen, denn dieser kann beim Lasersintern durchaus ein paar Tage laufen. Danach entnimmt ein Modellbauer (die Berufsbezeichnung im Prototypenbau heißt noch heute so) den kompletten Pulverblock und stellt ihn zum Abkühlen. Anschließend folgt eine Art Archäologie des Prototyping, wenn er die Teile unter einer Abzugshaube ausgräbt, mit einer Bürste entstaubt und in einer Kiste sammelt. Alles Pulver, das nicht in die Teile gewandert ist, wird mit frischem Substrat gemischt und erneut verwendet. Als Substrat ist übrigens nicht nur Kunststoff geeignet, auch Metall- und Sandpulver kommen für das Lasersintern in Frage.
Dreidimensionale Drucke im Prototypenbau
Außer dem Wegfall der Stützstrukturen hat das Verfahren einen weiteren großen Vorteil: Der Operator kann die Struktur des fertigen Materials beeinflussen, indem er die Intensität des Lasers steuert. Eine geringe Energiedichte des Strahls resultiert in einer weichen, gummiartigen Kunststoffqualität, zum Beispiel für Prototypen-Türdichtungen oder -Faltenbälge. Eine hohe Energiedichte produziert härtere Teile, zum Beispiel für Verkleidungsteile. Diese Festigkeitsmodulation ist selbst innerhalb ein und desselben Bauteils möglich, was in Serie derzeit noch nicht so ohne weiteres möglich ist. Bei BMW bauen die Modellbauer aus SLS-Teilen komplette Fahrzeugkarosserien, verlegen darin Kabel und testen, wie andere Prototypenteile passen. Zum Beispiel tragende Fahrzeugteile aus dem nächsten Verfahren:
Strahlschmelzen
Selektives Strahlschmelzen, englisch Selective Laser Melting, abgekürzt SLM, ähnelt dem Lasersintern stark. Wie dort produziert ein Laser Strukturschichten in ein pulveriges Substrat, dann senkt sich die Plattform um eine Schichtdicke, ein Rakel zieht frisches Metallpulver über die Fläche und der Prozess beginnt von vorn. SLM arbeitet jedoch mit einem Laser ungleich höherer Energie, der genug Leistung hat, um Metall regelrecht zu verschmelzen. Damit erreicht das Verfahren eine Werkstückfestigkeit, die Guss- oder Tiefziehteilen entspricht, was es möglich macht, die produzierten Teile gleich den Testfahrern in die Echtwelt-Fahrerprobung mitzugeben. Das funkensprühende Bruzzeln hinter dem Sichtschirm der Maschine funktioniert außer mit verschiedenen Stählen noch mit Aluminium, Titan und einigen anderen Metallen, ja selbst Keramiken wie Aluminiumoxid oder Zirkonoxid. Obwohl ein Bau-Job mit mehreren Tagen bis einer Woche vergleichsweise lang läuft und Stützstrukturen benötigt, sind die Möglichkeiten von SLS für eine Erprobung enorm nützlich.
Dreidimensionale Drucke im Prototypenbau
In der modernen Fahrzeugentwicklung wird wenig geschätzt, sondern gleich berechnet und simuliert. Die Ergebnisse dieser Arbeit liegen erstaunlich deckungsgleich über der Realität. Da diese aber unberechenbar komplex ist, folgt immer eine reale Erprobung. Und hier beschleunigt es die Feedback-Schleife der Fahrzeugentwicklung ungeheuer, wenn ein Ingenieur seine berechneten Teile für die Tiefziehpresse oder den Aluminiumguss in einer Woche schon draußen im Test haben kann – Teile, die wie gesagt fast exakt den späteren Serienteilen entsprechen. Die Strahlschmelzanlagen, die BMW einsetzt, kosten pro Stück rund eine halbe Million Euro. Sie sparen wahrscheinlich deutlich höhere Beträge.
3D-Drucken
Alle generativen Verfahren haben eine gewisse Ähnlichkeit mit Druckern, am deutlichsten ist die Ähnlichkeit bei den Geräten, die tatsächlich „3D-Drucker“ heißen. Diese Maschinen funktionieren im Grunde sehr ähnlich wie ein handelsüblicher Tintenstrahldrucker: Eine Düse tröpfelt verflüssigten Kunststoff auf eine sich schichtweise absenkende Trägerplatte. Die erste Generation der 3D-Drucker hatte meist nur eine Düse und arbeitete daher mit Stützstrukturen. Neuere Geräte sprühen meist zweierlei Substanzen aus zwei Düsen – eine den Werkstoff, die andere ein stützendes Wachs oder Gel. Wachse schmelzen bei Erwärmung, ein Gel löst sich in Wasser auf. Es bleibt in beiden Fällen ein krückenloses Werkstück.
BMW verwendet einen 3D-Drucker, der mit einem Acryl druckt und mit einem wasserlöslichen Gel stützt. Die Auflösung in Z-Richtung, also die Schichtdicke, liegt bei lediglich 16 Mikrometern. Das ist klein genug, um bewegliche Teile direkt in einem Durchgang auszudrucken. In der Beispielbox bei BMW liegt zum Beispiel ein funktionstüchtiger Engländer und ein handtellergroßes Planetengetriebe. Der Drucker ist außerdem so genau, dass die typische Stufenbildung generativer Prozesse dem ungeschulten Auge praktisch nicht mehr auffällt.
Dreidimensionale Drucke im Prototypenbau
Deshalb liegt in der Beispielbox außerdem eine Emily, Ikone der Luxustochter Rolls Royce und Gallionsfigur der so gebrandeten Fahrzeuge. Hier findet auch langsam ein Übergang statt vom Rapid Prototyping zum Rapid Manufacturing nach Kundenwünschen, denn es sind generativ problemlos einzigartige Einmalkonstruktionen möglich, die mit anderen Fertigungsmethoden nicht ohne Nacharbeit entstehen können. Viele der Kunststoffteile aus einem 3D-Drucker sind außerdem schon so nahe an der Serie, dass die Hersteller damit schon vor der Serienfertigung TÜV-Abnahmen machen. Und Hersteller können bei den sinkenden Preisen auch kleinere 3rd-Party-Zubehörhersteller sein, mit kaum mehr als zwei Dutzend Beschäftigten.
China auf dem Schreibtisch
Über die Themen Rapid Prototyping und Rapid Manufacturing gibt es mittlerweile einiges an Literatur und die Geräte werden immer kleiner, günstiger und vielseitiger. In der Architektur zum Beispiel sind 3D-Drucke mit Bindemittel in Gipspulver schon lange alltäglich. Mittlerweile gibt es von diesen Geräten Varianten, die mit farbigen Bindemitteln nicht nur dreidimensional, sondern obendrein in Farbe drucken, und die kaum größer sind als eine typische Office-Farblaserdruckanlage. Einen Schritt weiter geht das Open-Source-Team hinter dem Projekt RepRap (www.reprap.org). Der RepRapper ist ein Kunststoffdrucker, der die Kunststoffteile, aus denen er besteht, selber reproduzieren kann. Die nächste Generation soll sogar einen Teil ihrer Stromkreise mit ausgeben, und schon jetzt kann man sich einen RepRapper mit Teilen für unter 500 Euro aus dem Baumarkt und vom Conrad replizieren. Desktop Manufacturing steckt somit zwar noch in den Kinderschuhen, ist aber schon Realität. „China auf dem Schreibtisch“ nannte es Chris DiBona, Open Source Programs Manager bei Google.
Dreidimensionale Drucke im Prototypenbau
Vielleicht gehören Sie zu denen, die im Internet schöne GPS-Fahrtrouten schöner Strecken tauschen. Analog dazu gibt es für druckbare Teilelösungen bereits einen regen Ideen- und Datenaustasch. Auf absehbare Zeit wird es bei ausreichender Verbreitung solcher Geräte für bestimmte Dinge schneller gehen, sie als eine Art dreidimensionales Fax einzuscannen, als Daten übers Netz zu schicken und zeitnah auszudrucken, als die ewige Lotterie mit einem vergleichsweise langsamen Paketzusteller zu wagen. Aktuell arbeiten Ingenieure und Forscher außerdem daran, Schaltkreise aus organischen Polymeren in der hier beschriebenen Schichtarbeit zu bauen – inklusive OLED-Farbbildschirm. Es stehen uns also rosige Zeiten bevor. Wenn Ihnen in der schönen neuen Welt mal wieder ein Unbekannter beim Parken einen Spiegel abschert, dann können Sie sich in vielleicht gar nicht so ferner Zukunft ganz bequem mit einem Kaffee an den Rechner setzen und sich einen neuen im frei wählbaren Design aus dem 3D-Drucker lassen. (Clemens Gleich)
URL dieses Artikels:
https://www.heise.de/-501260
Copyright © 2009 Heise Medien