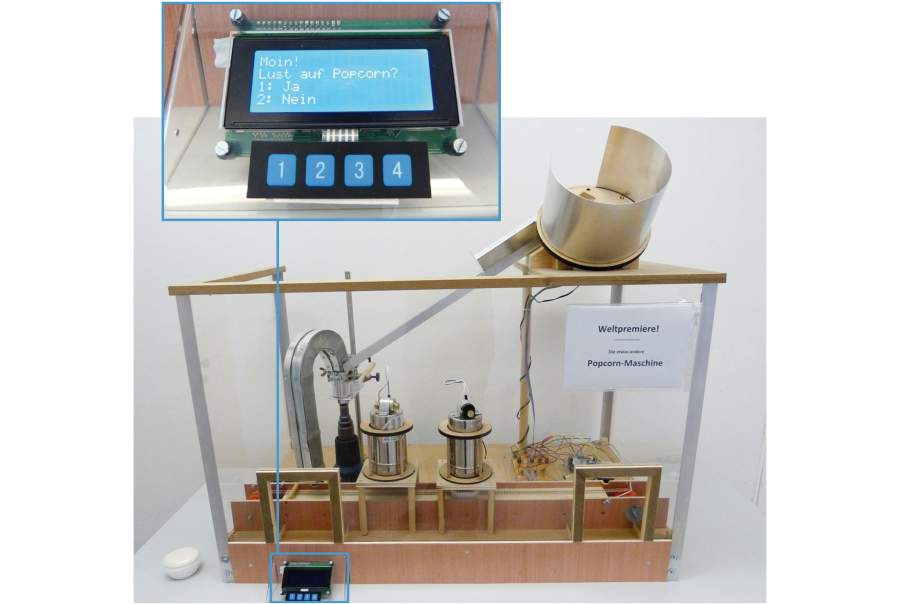
Arduino-Popcornmaschine
Süß, salzig oder ungewürzt – diese selbstgebaute Maschine bereitet große und kleine Portionen Popcorn frisch und ohne Öl zu.
Geschmackswunsch und Portionsgröße angeben, kurz warten und das individuelle Popcorn genießen: Auf der Maker Faire im Norden im November 2017 zeigten meine Studierenden mit der Popcornmaschine ein Projekt für den Technikunterricht, das sie nicht nur auf den Unterricht an Grund- und Gemeinschaftsschulen vorbereitet hat, sondern auch leckere Snacks serviert.
Die Maschine funktioniert so: Mittels Display und Tasten wird die gewünschte Menge und die Geschmacksrichtung (süß, salzig oder natur) des Popcorns eingegeben. Außerdem muss man eine Papierschale auf eine bestimmte Stelle der Maschine stellen. Eine Reflexlichtschranke stellt sicher, dass die Schale korrekt platziert ist und das Popcorn darin landen kann. Der Mais wird in einer Art Trichter gelagert und mit einer motorgetriebenen Lochscheibe vereinzelt. Die Maiskörner fallen über eine Rutsche in einem Zubereitungskorb. Eine weitere Reflexlichtschranke erfasst ihre Anzahl. Ist die Portionsgröße erreicht, stoppt die Lochscheibe.
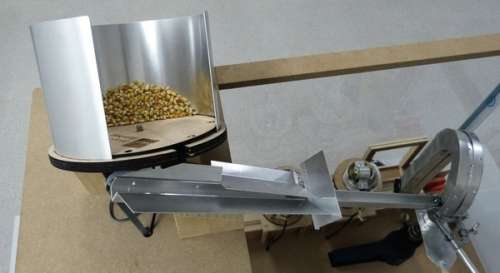
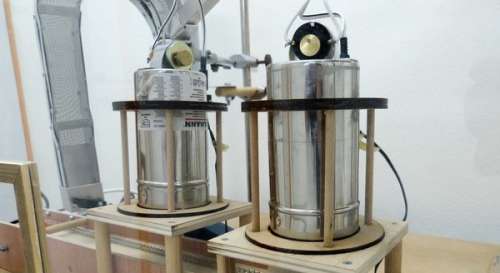
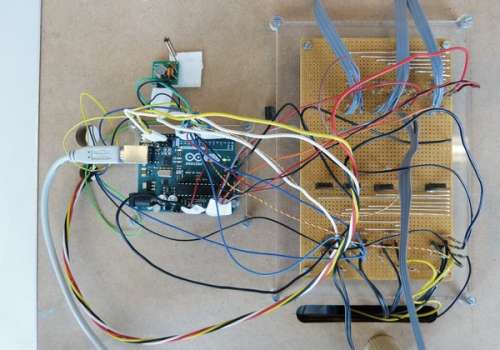
Ein Heißluftfön bläst die Maiskörner nun mit circa 200 Grad Celsius heißer Luft an. Nach 30 bis 60 Sekunden platzen die Körner auf. Der Luftstrom ist nach oben gerichtet, sodass die aufgepoppten Körner aufgrund ihres größeren Volumens erfasst und durch den Kanal gepustet werden. Am Ende des Kanals zählt eine dritte Reflexlichtschranke das Popcorn, bevor es in der bereitgestellten Papierschale landet. Ein Förderband transportiert das Schälchen zur Entnahmestelle. Dabei durchläuft es die beiden Würzstationen für Puderzucker und Pudersalz. Sie bestehen aus je einer beweglich aufgehängten Puderzucker-Streudose, die mit einem Vibrationsmotor geschüttelt wird, wenn der Inhalt herunterrieseln soll. Je nach gewünschter Geschmacksrichtung verharrt die Schale mit dem Popcorn für einen Augenblick unter der entsprechenden Würzstation und wird gesüßt oder gesalzen. Anschließend wird sie zum Entnahmepunkt befördert, wo der hungrige Besucher sie entnehmen kann.
Zum Bau der Maschine definierten wir Entwicklungsziele, etwa „soll Popcornduft verströmen“ und „Zubereitungsprozess soll sichtbar sein“. Anschließend teilten sich die Studierenden in Teams mit Aufgaben wie Vereinzelung, Würzung oder Steuerung auf. Mit begrenztem Budget, Zeitdruck und Bugs im Quellcode mussten sie mit einigen Problemen kämpfen, was allerdings nur den wenigsten Besuchern auffiel. Im Herbstsemester 2018/19 werde ich das Seminar „Projekte für den Technikunterricht“ wieder an der Europa-Universität Flensburg anbieten. Und die nächste Maker Faire im Norden findet am 17. und 18. November statt. —hch