Rare earths and platinum group metals: Can Europe be self-sufficient?
In our series we look at the extent to which Germany and Europe could free themselves from import dependencies. What about platinum metals and rare earths?
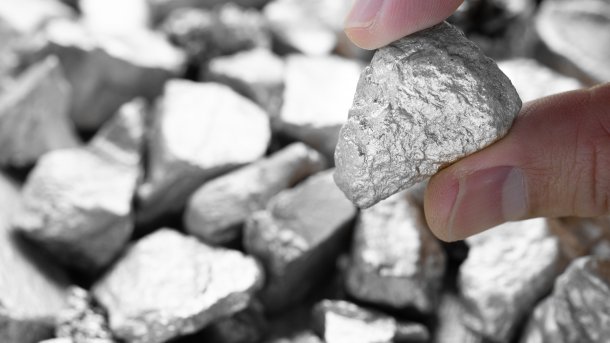
(Bild: Shutterstock)
(Hier finden Sie die deutsche Version des Beitrags)
Rare earths and platinum metals are the magicians among the chemical elements. They can give a material very special properties and thus open the way for new applications. Almost every future technology is therefore closely linked to one of these metals: scandium is used in fuel cells. Iridium can hardly be replaced in the electrodes of an electrolysis cell for hydrogen production. Neodymium, dysprosium, terbium and praseodymium strengthen the magnets used for wind turbines and motors in electric cars. Tantalum increases the performance of hard drives, displays and electrical capacitors. Ruthenium is an important metal for building high-performance computer centres. Lanthanum is in solid-state batteries and superconductors.
This list is only a small excerpt of the diversity. More than 30 metals belong to this group, which chemists call transition metals. But scandium, neodymium, dysprosium, terbium, praseodymium, tantalum, ruthenium and lanthanum stand out because the demand for these metals will increase rapidly in the coming decades. In its report on raw materials for future technologies, the German Raw Materials Agency (DERA) assumes that the demand for ruthenium in 2040, for example, could be almost twenty times greater than the current annual production. For scandium, dysprosium, terbium and iridium, the experts expect an increase by a factor of five to eight.
Shenzhen, Yantian Port
(Bild: zhangyang13576997233 / Shutterstock.com)
The past months have painfully shown that dependence on resources comes at a high price. But can the wheel still be turned back? So let's take a look at the supply situation.
How far Europe could supply itself with strategically important raw materials and what that means for industry is what we want to explore with a raw materials article series.
- New Series: De-Globalisation - How Independent Can Europe Be?
- De-globalisation: Can Europe supply itself with lithium?
- Rare earths and platinum group metals: Can Europe be self-sufficient?
- De-globalisation: Can Europe supply itself with steel and aluminium?
- De-globalisation: Can Europe supply itself with copper?
Shortage of rare earths and metals
Neither Germany nor Europe will be able to meet this growing demand with their own resources. This is already not possible today. The lack of transition metals could endanger the spread of future technology worldwide. The few countries that have deposits can presumably choose who they want to supply and who will be left empty-handed.
The example of ruthenium and iridium explains the problem: Worldwide, there are only three major deposits where these are mined as ores. In South Africa and Zimbabwe, the ores were transported to the upper earth's crust with magma two billion years ago and accumulated there during the cooling phase. In the region around Krasnoyarsk in Russia, the two metals are among the by-products of Siberian copper and nickel mines. DERA estimates global production in 2020 of ruthenium at 33 tonnes, and of iridium at about seven tonnes. Because so few suppliers are involved in the production process, there are hardly any official figures. However, the reserves in the three countries are estimated to be large enough to cover demand over a long period of time.
Scandium currently comes from China, the Philippines or Australia. Europe's dependence on exporting countries is lower for this metal. Scientists have also found significant deposits in the USA, Canada, Madagascar, Russia, Kazakhstan and Norway, but these are not yet being mined. The situation is similar for tantalum: the most important production sites are mines in Congo, Rwanda and Brazil. However, large tantalum deposits are also known in other countries in South America and Africa.
China has dominated the market for lanthanum, yttrium, cerium and the magnetic metals neodymium, dysprosium, terbium and praseodymium for years. These metals often occur together in minerals, for example in bastnäsite. Since the turn of the millennium, China has accounted for more than 80 per cent of global mining output, by far the largest share of which comes from the Bayan Obo mining area in Inner Mongolia in the north of the country. The official mining quantities of the state-owned companies are determined by the government. According to experts, however, between 25 and 50 per cent of Chinese production comes from illegally operated mines that are tolerated by the authorities.
Promotion of transition metals
In 2010, China tried to exploit its monopoly position and drive up the world market price. As an international reaction, mines in California, Australia, Russia, India, Vietnam, Thailand and Malaysia were re-equipped to take over some of the production. But production of the transition metals is not popular because the processes used to process the ores require large amounts of sulphuric and hydrofluoric acid, two chemicals that, along with the large amounts of toxic tailings from open-pit mining, have a significant impact on the environment. The environmental damage was so great that the Chinese government came under pressure and imposed stricter environmental regulations in the 2010s. China also imports ores from the USA and Myanmar, which are processed in the country.
Dependence on China for rare earths and start of recycling
With the exception of the production of electric motors, this market almost completely bypasses Europe. Here, it is mainly finished products that are imported and not the metals as raw materials. China processes a large part of the production itself, the most important export partners are Japan, South Korea and the USA. At the end of 2020, the EU drew up a plan on how to reduce dependence on China for these metals - knowing full well that production costs in Europe will be significantly higher than in China. The European Raw Materials Alliance (ERMA) proposes that manufacturers of components that use rare earths must buy some of the raw materials in Europe. Some of the mines could be reopened in Scandinavia (especially in Finland and Greenland), and the reprocessing should take place in Poland and Estonia. Production there should be less environmentally damaging than usual at many global locations.
In this way, a self-sufficiency rate of 20 per cent could be achieved. However, to achieve this, the recycling of products containing rare earths or platinum metals must begin. There are patents there, but according to DERA, these recycling processes will only be economically viable from 2040 onwards. The problem is that the proportion of valuable raw materials is very small in relation to the total mass. Exceptions are made for production waste and for particularly large parts made of alloys or motors as well as magnets. At present, raw materials extracted with considerable environmental damage are only used once, despite their importance. Recycling is probably the only way to reduce Europe's dependence on imports.
(jle)