Doppelkopf im Test: 3D-Drucker Ultimaker 3
Der Ultimaker 3 soll mit zwei Materialien gleichzeitig in 3D drucken – versprochen haben das schon viele, funktioniert hat es bisher erstaunlich selten. Doch mit diesem Gerät wird Dual Extrusion endlich Realität.

(Bild: Ultimaker)
Die 3D-Drucker des niederländischen Herstellers Ultimaker hatten zwar seit der ersten Generation Platz für die Montage eines zweiten Druckkopfs, in Serie ging diese Erweiterung allerdings nicht, ehe der Ultimaker 3 erschien. Der ist jetzt standardmäßig mit einem Doppelkopf ausgerüstet. Dieser besteht allerdings nicht aus einer simplen starren Montage zweier Extruder nebeneinander auf einem gemeinsam verschiebbaren Schlitten, wie man es von konventionellen Doppelkopf-Druckern wie dem Renkforce RF2000 von Conrad oder dem Creatr HS von Leapfrog kennt. Stattdessen lassen sich die Extruder im Kopf mit einem Handgriff einzeln austauschen – Ultimaker bietet unterschiedliche Modelle an, die für verschiedene Materialien optimiert sind und die die Maschine auch erkennt, um die Druckparameter entsprechend automatisch anzupassen.
3D-Drucker Ultimaker 3 im Test (16 Bilder)
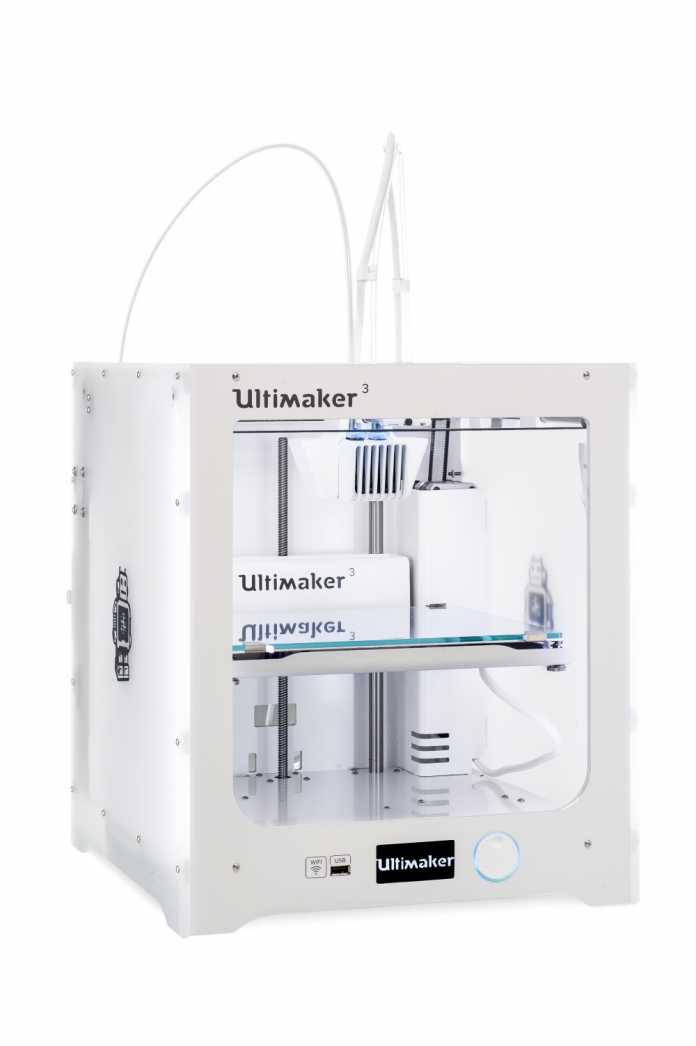
(Bild: Ultimaker)
Heben und schonen
Noch praktischer: Außerdem kann der Ultimaker 3 den von vorne gesehen rechten Extruder einige Millimeter in der Höhe verstellen. In der Praxis fährt so die rechte Düse in die Höhe, um aus dem Weg zu sein, wenn die linke ihre Arbeit tut; ist die rechte dann dran mit Drucken, fährt sie deutlich tiefer als die linke und die Maschine korrigiert die Position des Drucktisches entsprechend, sodass die rechte Düse freie Bahn hat. Damit umgeht Ultimaker das notorische Problem starr montierter Doppeldüsen, bei denen die gerade nicht aktive oft direkt über die frisch aufgeschmolzene Materialschicht kratzt und diese beschädigt. Hat man ganz viel Pech, löst sich dabei das mühsam aufgeschichtete Objekt von der Plattform und der Druck ist gelaufen – leider ist das bei vielen konventionellen Doppelkopfdruckern Alltag.
Stützen zum Auswaschen
Vor allem das Versprechen, die Probleme des Zwei-Materialien-3D-Drucks endlich gelöst zu haben, interessierte uns bei unserem Test des Ultimaker 3. Deshalb haben wir leichten Herzens auf den Druck unserer Standard-3D-Objekte verzichtet. Die sind eben speziell dafür entworfen, zu zeigen, wie sich ein 3D-Drucker mit nur einem Material und ohne Stützstrukturen schlägt. Stattdessen haben wir uns auf Werkstücke konzentriert, die ohne Stützen gar nicht zu fertigen sind und bei denen sich darüber hinaus Stützen aus demselben Material wie der eigentliche Werkstück nur sehr schwierig entfernen lassen. So druckten wir etwa drei geometrische Gitterkörper ineinander, einen Würfel, einen Ikosaeder und eine Sphäre aus lauter Dreiecken – silbernes PLA als Baumaterial auf der einen Seite und wasserlösliches PVA als Stützmaterial auf der anderen Seite machten es möglich (siehe auch Video).
Empfohlener redaktioneller Inhalt
Mit Ihrer Zustimmmung wird hier ein externes Video (Kaltura Inc.) geladen.
Ich bin damit einverstanden, dass mir externe Inhalte angezeigt werden. Damit können personenbezogene Daten an Drittplattformen (Kaltura Inc.) übermittelt werden. Mehr dazu in unserer Datenschutzerklärung.
Schichtwechsel
Der Druck des Geräts mit zwei verschiedenen Materialien ist interessant zu beobachten: Bei jedem Wechsel der aktiven Düse fährt der Druckkopf in die hintere linke Ecke und die frisch reaktivierte Düse trägt erst mal eine Schicht auf einen Turm mit quadratischem Grundriss (Kantenlänge 1,5 cm) auf, um den Materialfluss wieder gleichmäßig zum Laufen zu bringen und eventuell noch übrige Materialreste an der gerade deaktivierten Düse abzustreifen. Das funktionierte im Test durchgehend zuverlässig – am Ende landeten die beiden Materialien genau dort, wo sie hinsollten und waren vor allem dort nicht zu finden, wo sie nicht hinsollten. Das ist leider beim Doppelkopfdruck bis heute keine Selbstverständlichkeit. Gelingen anderen Maschinen Vorzeigestücke wie gestreifte Kegel noch ganz passabel (weil da nur wenige Materialwechsel drin sind), kommt hingegen unser Test-Getriebe meist als gesprenkeltes Gemisch aus zwei Kunststoffen heraus. Nicht so beim Ultimaker 3: Das Getriebe erwies sich nach dem Auflösen des stützenden PVA nicht nur als nahezu perfekt gedruckt, sondern auch als funktionsfähig.
Empfohlener redaktioneller Inhalt
Mit Ihrer Zustimmmung wird hier ein externes Video (Kaltura Inc.) geladen.
Ich bin damit einverstanden, dass mir externe Inhalte angezeigt werden. Damit können personenbezogene Daten an Drittplattformen (Kaltura Inc.) übermittelt werden. Mehr dazu in unserer Datenschutzerklärung.
Neuralgischer Punkt
Allerdings konnten wir eine kritische Stelle identifizieren, die bei uns im Test darüber entschied, ob der Druck gelang oder komplett fehlschlug. Ist die Düse zum allerersten Mal bei einem Druck an der Reihe, fährt der Kopf ans vordere Ende der Druckplatte und drückt dort einen kleinen Klumpen Material hin. Dann fährt er zur ersten Druckposition, und zwar so flott, das der Klumpen auf der Platte kleben bleibt und der nachgezogene Faden flüssigen Materials aus der Düse abreißt. Bei PLA funktionierte das im Test zuverlässig, beim deutlich zäheren PVA nicht immer – da kam es schon vor, dass der Materialfaden aus der Düse nicht unterbrochen wurde, sondern am Klumpen festhing und den komplett von der Grundplatte rupfte und auch noch hinter sich herzog. So ein unkontrollierter Materialklumpen kann allerdings einem Druck gefährlich werden: Im schlimmsten Falle klebt er an einer frischen Materialschicht fest, ist dann der Druckdüse im Wege, die unter Umständen mit dem Klumpen als Angriffspunkt das ganze Werkstück losreißt. So passierte es in unserem Test auch einmal, sodass wir in der Folge jedesmal zu Druckbeginn den Klumpen aus PVA mit einer Pinzette auf der Druckplatte festhielten. War der kritische Moment vorbei, gelangen auch extensive Drucke problemlos – unser aufwendigstes Arrangement aus drei Testobjekten brauchte sogar zwei Tage und neun Stunden zur Fertigstellung.
Gerät | Ultimaker 3 |
Hersteller / Vertrieb | Ultimaker / u.a. iGo3D, Reichelt, Conrad, Comprise |
Bauraum | 19,7 cm × 21,5 cm × 20 cm (bei Dual Extrusion) |
Drucktisch | Glasplatte, beheizt |
Software | Cura (Windows, MacOs, Linux) |
Filamentstärke | 2,85 mm |
Material | Nylon, PLA, ABS, CPE oder PVA |
Druck über.... | USB-Stick, USB, WLAN, LAN |
Preis | ca. 3600 € |
Einschätzung
Der von Ultimaker beschrittene Weg, mit zwei Materialien zu drucken, funktioniert in der Praxis gut. Das eröffnet dem 3D-Druck tatsächlich neue Möglichkeiten, da es eben doch Objekte gibt, die sich nicht ohne Stützen fertigen lassen und die man nicht sauber entstützt bekommt, wenn man die Stützstrukturen aus demselben Material aufbaut wie das Werkstück selbst. Allerdings hat sich der Hersteller mit dem Ultimaker 3 noch mehr vorgenommen als unfallfreier Doppelkopf-Druck: Eigentlich soll die Maschine auch in den Händen weniger versierter Nutzer zuverlässig gute Ergebnisse liefern, weshalb zum Beispiel die gerade eingesetzte Düse oder das eingespulte Material automatisch erkannt werden sollen. Was im Druckkopf reibungslos funktionierte, schlug in unserem Test bei den per NFC identifizierten Materialspulen häufiger fehl – der Drucker bat dann darum, doch von Hand auszuwählen, um welches Material es sich gerade handle. Auch unsere oben geschilderte Beobachtung, dass man besser den ersten PVA-Klumpen festhält, erfordert Aufmerksamkeit vom Bediener. Ein guter Doppelkopf-3D-Drucker für versierte Anwender ist der Ultimaker 3 auf jeden Fall. Es scheint aber noch Finetuning nötig, bis auch Leute damit nichts mehr falsch machen können, die nicht tief in den 3D-Druck einsteigen wollen oder können.
- Das Testgerät wurde uns von iGo3D zur Verfügung gestellt.
()