Meisterschaft der Maschinen: Die Industrial Logistic Liga
Die autonomen Industrie-Logistik-Roboter müssen im Team arbeiten, dabei flexibel auf Störungen reagieren und in Echtzeit Entscheidungen treffen. Sie sind Blaupause für KI-Systeme in der Industrie 4.0.
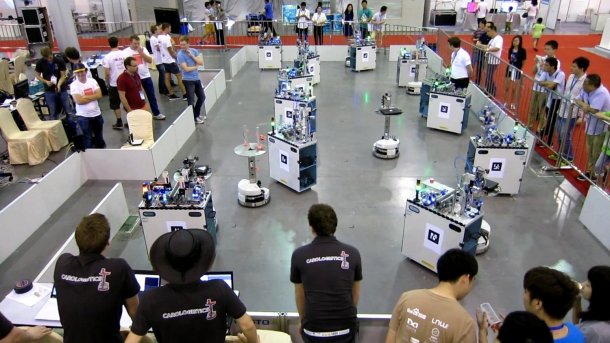
- Alexander Ferrein
- Ulrich Karras
- Tim Niemueller
Die Produktion in Fabriken steht am Rande eines Paradigmenwechsels: Weg von starren Routinen und hin zu einer dynamischen, flexiblen Aufgabenverteilung – stark beeinflusst vom Internet of Things (IoT) oder genauer von Cyber-Physischen Systemen (CPS).
Meisterschaft der Maschinen:
In solchen CPS arbeiten Systeme zu Datenverarbeitung mit mechanischen Systeme zusammen. Dabei nehmen Sensoren die Umwelt wahr und Aktuatoren – bis hin zu autonomen Robotern – manipulieren die Werkstücke. Zusammengefasst werden die vielfältigen Entwicklungen unter dem Schlagwort Industrie 4.0.
Ein wichtiger Aspekt von Industrie 4.0: Die Produktion soll flexibler gestaltet werden, um auch kleine Stückzahlen effizient zu fertigen. Das erlaubt unter anderem eine weitere Personalisierung von Produkten, aber auch eine kostengünstigere Fertigung von Nischen- und Spezialprodukten. So war Ende 2016 zu lesen[1], dass Audi von der Fließbandproduktion zu flexiblen Produktionsinseln wechseln will. Dabei werden nur solche Produktionsinseln von den autonomen Flurförderfahrzeugen angesteuert, die für das gerade produzierte Auto relevant sind.
Proben für Industrie 4.0
Genau an diesem Punkt setzt die RoboCup Logistik-League (RCLL) an. In der Liga geht es darum, dass eine Gruppe von mobilen Robotern einen Produktionsfluss aufrecht erhält und optimiert. Dafür müssen die Roboter auf einem Feld mit Produktionsstationen gemäß eines flexiblen und dynamischen Produktionsplans, der von außen vorgegeben wird, bestellte Produkte in einem vorgegebenen Zeitfenster ausliefern. Alle Roboter arbeiten dabei voll autonom, alle Entscheidungen müssen also in Echtzeit und von den Robotern selbst gefällt und umgesetzt werden. Ziel ist es, Systeme zu erforschen und prototypisch umzusetzen, die Methoden aus der künstlichen Intelligenz nutzen. Diese sollen dann später in Kooperation mit der Industrie in die reale Produktion transferiert werden.
Die Industrie braucht allerdings stabile Lösungen. Daher hat sich die RCLL als weiteres Ziel gesetzt, ein Benchmark-Szenario für Prozesse der Intraproduktionslogistik[2] zu entwickeln. Zum einen können Planungsalgorithmen analysiert werden, wie es 2017 im Rahmen eines Simulationswettbewerbs auf Basis der RCLL zur automatischen Aufgaben- und Zeitplanung geschehen wird. Zum anderen können im Wettbewerb die unterschiedlichen Produktionsstrategien der Roboterteams anhand von Produktionskennzahlen, wie sie bereits in der Industrie verwendet werden, analysiert und bewertet werden.
Die RCLL ist eine vielschichtige Domäne: Neben Grundfragestellungen der mobilen Robotik wie Navigation, dynamische Kollisionsvermeidung, Lokalisierung, Sensordatenverarbeitung und präzisem Maschinenhandling muss sie auch produktionsseitig bedingte Probleme wie Störungen oder Ausfall von Produktionsmaschinen oder Ausschuss lösen. Damit integriert sie Supply-Chain-Management und Bereiche der dynamischen Planung aus dem Forschungsgebiet der Künstlichen Intelligenz.
DIe RCLL-Wettbewerbe
Im Wettbewerb treten pro Spiel zwei Teams mit jeweils drei Robotern auf einem gemeinsamen Feld gegeneinander an. Jedes Team hat dabei exklusiv sechs Produktionsstationen mit unterschiedlichen Fähigkeiten zur Verfügung – verteilt über das gesamte Spielfeld. Das Antreten von zwei Teams bringt eine größere (gewollte) Unsicherheit in das Spiel, mit der die Teams umgehen müssen — und natürlich geschieht dies auch im Sinne eines attraktiven RoboCup-Wettbewerbs. Das Spiel hat zwei Phasen. In der ersten, der Explorationsphase, müssen die Roboter den Typ und die Position der unterschiedlichen Produktionsmaschinen identifizieren und melden. In der folgenden Produktionsphase müssen die Roboter die eigentliche Produktion betreiben.
Unsere weitere Beschreibung bezieht sich auf das Spiel von 2016 (die Liga wird stetig weiterentwickelt).
Das Spielfeld
Das Spielfeld ist in 24 rechteckige Zonen von 2 m x 1.5 m aufgeteilt. Auf diese Zonen werden zwölf Produktionsmaschinen zufällig verteilt.Jedem Team werden sechs Produktionsmaschinen unterschiedlichen Maschinentyps zugeordnet sowie eine Base Station (BS); diese liefert die Grundelemente der Produkte. Zwei Cap Stations (CS) pro Team ermöglichen das Montieren von Deckeln. Sie müssen vorab mit Deckeln befüllt werden. Um eine große Variantenvielfalt zu erzeugen, enthalten die Produkte bis zu drei verschiedenfarbige Ringe. Zwei Ring Stations (RS) pro Team mit jeweils zwei verfügbaren Farben werden genutzt, um diese Ringe zu montieren. Manche Ringfarben erfordern das vorherige Anliefern von Rüstmaterial. Die Delivery Station (DS) erlaubt schließlich das Abliefern von Produkten.
Auf den Spielfeldern Stehen verschiedene Maschinen, die von der Firma Festo bereitgestellt werden. Sie sind durch spezielle AR-Tags (ähnlich zu QR codes) markiert, die eine eindeutige Kennzeichnung der Maschinen für die Roboter liefern.
Die Produkte
Produkten, die in der RCLL hergestellt werden können., unterscheiden sich in ihrer Komplexität und den daraus resultierenden Arbeitsschritten. So besteht ein C0 Produkt aus einem Basiselement und einem Deckel. Deutlich komplexer wird der Produktionsplan beim C3-Produkt: Neben Basiselement und Deckel müssen hier noch drei Ringe hinzugefügt werden. Da es auch auf die Reihenfolge der Ringe ankommt, sind bis zu 240 verschiedene Produktvarianten möglich.
Produktabläufe in der RCLL (5 Bilder)

Alle Maschinentypen und -positionen werden von der Referee-Box an die Teams kommuniziert, um gleiche Produktionsbedingungen zu gewährleisten. Die Referee-Box generiert während der 15 minütigen Spielzeit Aufträge von unterschiedlichen Produkten mit entsprechenden Angaben über die Auslieferungszeit. Die Referee-Box überwacht über die Kommunikationsschnittstelle zu den Maschinen die Produktionsschritte und vergibt entsprechend eines vorgegebenen Regelwerks vier Bewertungspunkte.
Referee-Box
Eine Besonderheit der Logistik-Liga: Die Umgebung, also das Feld mit den Maschinen, ist selber ein System, das Sensordaten der Maschinen verarbeitet, Entscheidungen trifft und zur Ausführung anweist. Diese Funktion wird von der Referee-Box[3] erfüllt. Sie ist als wissensbasiertes System konzipiert, das Spiel selbst ist in einem regelbasierten System modelliert. Außerdem erstellt die Referee-Box auch den zufallsbasierten Bestellkatalog mit Zeitvorgaben und geplante Maschinenausfälle; Letztere sind für einen beschränkten Zeitraum aktiv und den Teams nicht vorab bekannt. Die Box kommuniziert mit den Robotern, etwa um Aufträge mitzuteilen oder Anweisungen für das Rüsten der von den Maschinen durchzuführenden Operationen entgegenzunehmen.
Das angestrebte Ziel des Benchmarking ist nur möglich, wenn man das Verhalten der Teams analysieren kann. Die Referee-Box schafft die wesentlichen Voraussetzungen hierzu: Sie zeichnet alle Zustandsveränderungen, Spielparameter und jegliche externe Kommunikation in einer Datenbank auf. Diese Daten können dann zur genaueren Analyse der Spiele verwendet werden.
Simulation separater Schritte
Die integrierten Systeme der Teams sind äußerst komplex und benötigen eine erhebliche Entwicklungszeit, wobei die Teams nur selten ein vollständiges Spielfeld zur Verfügung haben. Deshalb wurde eine vollständige Simulation des Spiels auf Basis der Gazebo-Engine entwickelt. Die Simulation ermöglicht es, vertikale Abhängigkeiten während der Tests aufzulösen. So werden zum Beispiel die technisch oft sehr komplexen Schritte wie das Handling der Werkstücke abstrahiert, sodass sich die Entwickler zunächst darauf konzentrieren können, Strategien für Spielabläufe zu modellieren. Erst in einem weiteren Schritt werden dann die separat entwickelten Teilkomponenten auf den realen Roboter integriert.
Koordiniert planen
Die RCLL fordert die Teams in vielen Bereichen der mobilen autonomen Robotik heraus. Ein besonderes Augenmerk liegt auf der automatisierten verteilten Aufgaben- und Zeitplanung zur Koordination der Robotergruppe. Das Team Carologistics hat sein gesamtes Softwaresystem als Open Source Software veröffentlicht[4]. Im Laufe eines Spiels laufen dort etwa 50 Softwarekomponenten — pro Roboter. Einzelne Softwarekomponenten müssen gezielt nur für kurze Zeit aktiviert werden, um mit den beschränkten Ressourcen auf dem Roboter auszukommen, was ein weiteres Koordinationsproblem darstellt.
Hinzu kommen noch die Feldinfrastruktur (Maschinen, Referee Box), gegebenenfalls die Simulationsumgebung mit zahlreichen Plugins sowie Adapter zu anderen Systemen. Bereits die direkten Abhängigkeiten der Software erfordern weit über hundert Zusatzpakete und Softwarebibliotheken. Die Integration dieser komplexen Systeme stellt also eine große Herausforderung dar.
Aber auch die methodischen Fragen sind mitunter sehr komplex. So stößt etwa das Planungsproblem mit zeitlichen Abhängigkeiten und kurzen Planzeiten schnell an seine Grenzen. Die Anfahrt an Maschinen auf wenige Millimeter Genauigkeit erfordert robuste und dennoch sehr schnelle Sensordatenverarbeitung sowie eine präzise Robotersteuerung.
Entwicklung der Liga
Am Anfang war der Puck...
Die RoboCup Industrial Logistics League wurde beim RoboCup 2012 in Mexiko das erste Mal offiziell ausgetragen, seinerzeit noch unter dem Namen Logistics League Sponsored by Festo. Die ersten “Produkte” der Liga waren Hockey-Pucks, die mit RFID-Chips ausgestattet waren. Sie konnten von den “Maschinen” auf dem Feld programmiert werden, um unterschiedliche Zwischenprodukte darzustellen. Die Pucks wurden unter die Maschinen geschoben, die daraufhin durch eine Ampel den Produktionsstatus anzeigten[5]. Jedes Team spielte auf einem eigenen Feld, Interaktionen zwischen gegnerischen Robotern fand nicht statt. Ein Startschuss in Richtung industrielle Anwendung war gegeben, aber für die Zuschauer war das Spiel noch sehr undurchsichtig. Vom Blickwinkel der mobilen Robotik war das Geschehen eher als einfach einzustufen.
dann kam der Schiedrichter...
Als erste Innovation wurde 2013 die schon erwähnte Referee-Box eingeführt, um den auch für die Schiedsrichter sehr schwierig zu verfolgenden Spielablauf von der Bewertung zu automatisieren. Dadurch konnten Informationssysteme geschaffen werden, die das Geschehen auch für die Zuschauer transparenter machte. Zwei parallele Felder wurden miteinander synchronisiert und Teams konnten erstmals gegeneinander antreten – wenn auch weiterhin in separaten Spielflächen.
... und die Kollision
Gemäß dem RoboCup-Gedanken wurde das Szenario schrittweise komplizierter gemacht, um Innovationen bei den teilnehmenden Teams zu fördern. So wurden im nächsten Schritt die beiden separaten Spielfelder zusammengelegt, so dass sich nun Roboter aus verschiedenen Teams begegneten. Damit mussten die Roboter mit robuster Kollisionsvermeidung ausgestattet werden. Bewusst wurden einige Maschinen in das Hoheitsgebiet des jeweilig anderen Teams gelegt, um Situationen zu schaffen, in denen Kollisionsvermeidung benötigt wird.
Ab 2014 mit Benchmarking
2014 wurden die ersten Schritte zu einem gezielten Benchmarking unternommen. Abbildung 5 zeigt die Maschinenauslastung der beiden Finalisten von 2014. Auffällig sind die langen orange und dunkelgrün markierten Phasen des zweiten Teams. In den orangenen Phasen stehen Werkstücke zur Abholung an einer Maschine bereitstehen, in den dunkelgrünen warten Maschinen auf weiteres Material. Mit dieser Beobachtung kann man auf zwei unterschiedliche Produktionsmodelle der Teams schließen: Während das Team oben auf einen hohen Durchsatz setzte, wollte das untere Team eine große und gleichmäßige Auslastung aller Maschinen gewährleisten. Der Ansatz des Teams Carologistics aus Aachen erwies sich jedoch in dem gegebenen Szenario als effizienter.
Die genannten Produktionsmodi und weitere Kennzahlen sind aus der Industrie bekannt. Sie zeigen die Eignung des Szenarios als Benchmark, in dem diese bereits Anwendung finden können.
Produktionsmaschinen ins Feld
2015 wurde dann ein radikaler Schritt durchgeführt. Es wurden MPS-Produktionsmaschinen der Firma Festo eingeführt und die festen Positionen der Maschinen komplett aufgegeben. Die Roboter mussten sowohl die Position der Maschinen als auch den Typ der Maschine auf dem Spielfeld erkennen. Um diese Aufgabe etwas zu erleichtern, wurden die Maschinen mit AR-Tags gekennzeichnet.
Insgesamt wurde das Handling der Maschinen jedoch erheblich erschwert. So wurde die Produktvielfalt von 3 auf etwa 240 mögliche Kombinationen erweitert. Noch dazu waren nun dynamischere Abläufe und eine flexiblere Koordinierung der Roboter gefordert.
Innovationen und Zukunft der Liga
Für den nächsten RoboCup 2017 in Nagoya gibt es wieder eine Reihe von Innovationen. So wurde das Spielfeld vergrößert und die Spielzeit verlängert. Außerdem erhalten beide Teams neue Stationen zur Lagerung von Werkstücken, um Produktionsstrategien noch flexibler und variabler gestalten zu können.
Es gibt auf Seiten des Technischen Komitees (TC) und des Organisationskomitees (OC) weitere Innovationen, die in den nächsten Jahren umgesetzt werden sollen. Eine Idee ist, die Form mit “Anpfiffzeiten” abzuschaffen. Mit Hilfe der Referee-Box kann die Produktion komplett gesteuert und die Punktzahl automatisch ermittelt werden. So bestünde die Möglichkeit, eine Produktion im 24/7-Modus durchzuführen: Es wird dann ohne Stillstand während des gesamten RoboCups produziert und Teams können Punkte einfahren.
Das genaue Prozedere muss noch im Einzelnen geklärt werden, aber man hätte hier die Möglichkeit, einen Benchmark für die verschiedenen Ansätze der Teams im Dauereinsatz zu schaffen. Anforderungen an die Robustheit und Flexibilität würden für die Teams noch einmal deutlich gesteigert. Auch ein Energiemanagement der Roboter würde notwendig.
Im Rahmen der Internationalen Konferenz zur automatisierten Aufgaben- und Zeitplanung (ICAPS) wird 2017 erstmalig ein Wettbewerb in Simulation, basierend auf der RCLL durchgeführt[6]. Durch die Entkoppelung von tatsächlichen Robotersystemen wird es möglich, sich noch stärker auf die effiziente Koordination der Roboter zu konzentrieren und weitere Forschungsfelder enger anzubinden. Denn auch in einer vermeintlich einfachen Umgebung wie der RCLL gibt es schon erhebliche Herausforderungen in der Planung. Mittelfristig sollen Ansätze aus dem Simulationswettbewerb wieder auf die RCLL übertragen und neue Teams gewonnen werden. Der Wettbewerb unternimmt auch Schritte hin zu einer Verlagerung der Softwareprozesse in Cloud-basierte Systeme.
Unwägbarkeiten trotzen
Die RCLL befasst sich als eine der beiden RoboCup Industrial Ligen mit einer wichtigen Fragestellung der Produktion der Zukunft: der Intraproduktions-Logistik. Dabei muss ein Team von Robotern einen dynamischen Produktionsplan erarbeiten und flexibel durchführen und die Roboter müssen mit Unwägbarkeiten wie Maschinenausfällen oder Ausschussproduktion umgehen, um einen zeitlich festgelegten Auftrag zu erfüllen.
Dabei hat die Liga verschiedene Herausforderungen sowohl auf der planerischen Seite als auch auf der Robotik-Seite. Beide müssen erfolgreich von den Teams gemeistert werden. Die Liga ist sehr dynamisch, sie wird fortlaufend weiterentwickelt und es werden neue Herausforderungen eingeführt. Dabei wird auch versucht, das Szenario immer weiter an ein echtes Produktionsszenario anzugleichen, ohne allerdings die Einstiegshürden zu groß werden zu lassen. Interessierte können das Szenario mit einem bootbaren USB-Stick gleich einmal selber ausprobieren[7].
Literatur
[2] Niemueller, T., Lakemeyer, G., Reuter, S., Jeschke, S., & Ferrein, A. (2017). Benchmarking of cyber-physical systems in industrial robotics—the RoboCup logistics league as a CPS benchmark blueprint. Cyber-physical systems—foundations, principles, and applications. Elsevier
[3] T. Niemueller, S. Zug, S. Schneider, U. Karras (2016). Knowledge-based Instrumentation and Control for Competitive Industry-Inspired Robotic Domains. In KI - Künstliche Intelligenz, October 2016, Volume 30, Issue 3, pp 289–299.
[4] https://www.fawkesrobotics.org/projects/rcll2016-release/
[5] Weitere Informationen zu den Spielfeldern und der Liga im Allgemeinen sind auch unter http://www.robocup-logistics.org/media zu finden.
[6] http://www.robocup-logistics.org/sim-comp
[7] https://trac.fawkesrobotics.org/wiki/RestoreUSBStickImage (uk)