Hintergrund: Packaging-Techniken für Chips und Chiplets
Statt monolithischer Chips werden Hochleistungs-CPUs schon heute aus mehreren Chiplets zusammengesetzt. Künftig wird das zum Standard werden – ein Überblick.
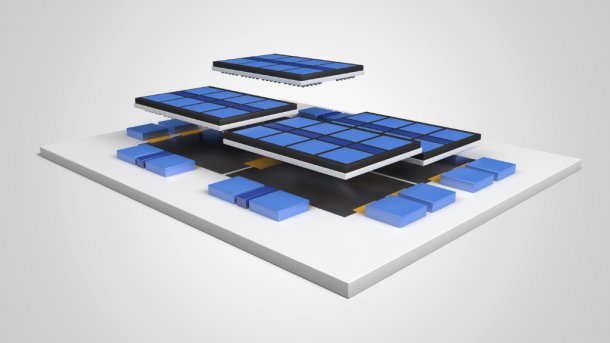
(Bild: Bild: Sven Hauth, basierend auf Intel-Grafik)
- Florian Müssig
Bislang lag das Hauptaugenmerk bei Prozessoren und Grafikchips immer auf dem jeweiligen Chip selbst, obwohl so ein Silizium-Schnipselchen (genannt Die) nie direkt zum Einsatz kommen kann: Die Kontakte am Chip selbst sind zum Auflöten auf Platinen oder zum Einstecken in Fassungen viel zu winzig. Die Übersetzung in praktikable Größenordnungen übernimmt das sogenannte Package, das sich nur ungenau als "Gehäuse" übersetzen lässt. Es geht um ein meist grünlich aussehendes Substrat aus organischen Materialien, dessen eingebettete Leiterbahnen die Kontakte in mehreren Schichten immer größer werden lassen, bis man dann wahlweise Füßchen (PGA: Pin Grid Array), Kontaktflächen (LGA: Land Grid Array) oder Lotkugeln (BGA: Ball Grid Array) in alltagstauglicher Millimeter-Größe erhält.
Die Untersetzung im Package erstreckt sich grob über eine Größenordnung. Die restlichen Schritte von den nanometerkleinen Transistoren bis hin zu den nach außen geführten Kontakten am Die (100 µm oder größer) erfolgt mittels Metallschichten im Chip, die auch die Verdrahtung nicht benachbarter Transistorbereiche übernehmen. Die Aufteilung dieser Streckung ist seit Jahren nahezu unverändert, denn das Substrat hat gewisse Limitierungen, was die Dichte der Lötpunkte beziehungsweise der zugehörigen Leitungen angeht.
Package-on-Package-Stapel
Für manche Anwendungszwecke reicht das allerdings schon aus. Smartphone-Prozessoren etwa werden traditionell als Package-on-Package-Stapel (PoP) gefertigt. Auf das Package des passiv kühlbaren SoC-Prozessors wird ein weiteres Package mit dem Arbeitsspeicher gesetzt – eine kompakte Bauweise, dank der der Fußabdruck des PoP-Gebildes auf der Hauptplatine klein bleibt und nur noch vergleichsweise wenige Kontakte zwischen den beiden hergestellt werden müssen. Zudem hilft die Bauform beim Stromsparen, denn wenige Übergangspunkte und besonders kurze Leitungen erlauben geringe Spannungen.