Das neue Edelholz
Holz wird durchsichtig, elektrisch leitend, magnetisch: Wer in dem Material nur einen Rohstoff für Bodenbelag und Möbel sieht, ist auf dem Holzweg.
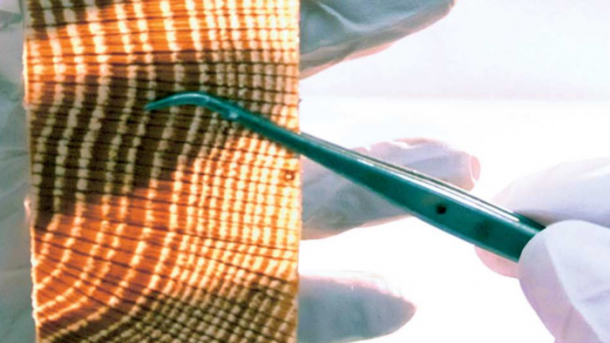
(Bild: Woodoo)
- Wolfgang Richter
Mahagoni glitzert mit tausend Sternchen, Tanne glänzt wie Perlmutt, Eiche erinnert an den Panzer eines Insekts. Wenn der junge Architekt und Materialforscher Timothée Boitouzet seine Proben gegen die Sonne hält, erkennt man bei manchen gar nicht, dass es sich um Holz handelt. Es ist allerdings auch kein gewöhnliches Holz, denn Boitouzet hat es durchsichtig gemacht, es schimmert wie Eis. Sein Pariser Start-up Woodoo entfernt dazu einen lichtundurchlässigen Bestandteil des Holzes – das Lignin – und ersetzt es durch einen biobasierten, durchsichtigen Kunststoff. Die natürliche Struktur des Holzes wird dabei nicht verändert. Obwohl Woodoo erst seit zwei Jahren existiert, hat es mit seiner Methode bereits 24 Innovationspreise eingeheimst.
Lesen Sie dazu auch:
Holz schimmert wie Eis
Das liegt zum einen sicher daran, dass die mehrere Millimeter dicken Paneele extrem ästhetisch wirken und dafür prädestiniert sind, in Luxusautos, Jachten und Penthäusern effektvoll von hinten ausgeleuchtet zu werden. Nach eigenen Angaben hat Woodoo bereits Verträge mit dem französischen Luxuskonzern LVMH abgeschlossen – Inhalt allerdings streng geheim. Boitouzet aber hat eigentlich etwas anderes im Sinn. "Durch das Polymer wird das Holz bis zu zehnmal stärker", sagt er. Denn es nähme nicht nur den Platz des Lignins ein, sondern würde auch in die von Natur aus vorhandenen luftgefüllten Zwischenräume eindringen. "Damit wird das Holz auch unempfindlicher gegenüber Wasser und feuerfester." Dicke Bohlen aus jeweils senkrecht zueinander verleimten Lagen des neuen Materials sollen so zur Grundlage des Bauens werden. "Das 19. war das Jahrhundert des Stahls, das 20. das des Betons. Das 21. Jahrhundert wird das des Holzes werden", ist sich Boitouzet sicher.
Tatsächlich hat die Holzforschung gerade in den letzten Jahren erstaunliche Erfolge erzielt. Die Entwicklung läuft dabei in zwei gegensätzliche Richtungen. Einerseits versuchen Wissenschaftler, die Eigenschaften von Holz so zu verbessern, dass es immer mehr Funktionen erfüllen kann. Sie machen Holz antimikrobiell, wasserfest oder durch eingelagerten Kalk feuersicher, stellen sogar magnetisches oder elektrisch leitendes Holz her. Auf der anderen Seite zerlegen Forscher das Holz in seine Bestandteile und produzieren aus diesen gänzlich neue Materialien, die Produkte aus Erdöl ersetzen können.
Holz wird der Werkstoff des 21. Jahrhunderts
Um die vielen unterschiedlichen Konzepte zu verstehen, ist ein Crashkurs in Holzkunde unumgänglich: Das Gerüst für die Zellwände eines Baums liefert die Zellulose, ein Polymer, das aus vielen Tausend Glukosemolekülen besteht. Etwa hundert dieser Stränge lagern sich zu einer "Elementarfibrille" zusammen, stabilisiert von den Anziehungskräften zwischen ihren Wasserstoffatomen. Jeweils etwa 20 dieser Elementarfibrillen bilden gemeinsam eine Mikrofibrille mit einem Durchmesser von 10 bis 30 Nanometern und einer Länge von mehreren Mikrometern. Diese Mikrofibrillen wiederum bündelt der Baum zu Makrofibrillen mit einem Durchmesser von mindestens 500 Nanometern, wobei sich Zwischenräume von einigen zehn Nanometern bilden. Diese sind teilweise mit Lignin ausgefüllt. Während die Fibrillen für die Zugfestigkeit des Holzes verantwortlich sind, sorgt der Füllstoff Lignin für die notwendige Druckfestigkeit. Den Kontakt zwischen beiden vermitteln die sogenannten Hemizellulosen – sie bestehen nicht aus Glukose, sondern aus anderen Zuckersorten, und ihre Polymerstränge sind nur einige Hundert Moleküle lang.
"Verglichen mit den drei anderen klassischen Baustoffen Stahl, Glas und Beton ist Holz sehr komplex aufgebaut", sagt der Leiter der Holzforschung an der TU München, Klaus Richter. Denn nicht nur die Zellwände eines Baums sind kunstvoll konstruiert. Die Zellen selbst unterscheiden sich je nach ihrer Funktion für den Baum, und ihre hohlen Innenräume sind über ein Netzwerk dünner Kanäle und Ventile miteinander verbunden. Die komplizierte Struktur sei Segen und Fluch zugleich, sagen die Holzforscher. "Holz wurde durch die Evolution in Jahrmillionen optimiert", erklärt Richter. "Das Ziel der Natur war dabei aber, dass ein Baum lange lebt. Nicht, dass er uns schöne Bretter liefert."
Magnetische Holzwand als Messerhalter
Den besonderen Aufbau des Holzes nutzen etwa jene Forscher aus, die es magnetisch machen wollen. Dazu weichen sie das Holz in einer sauren Lösung ein, die Eisenchlorid enthält. Wenn die Flüssigkeit tief eingedrungen ist, legen sie das Brett in eine starke Lauge. Eine sogenannte Fällungsreaktion ist die Folge: Im gesamten Holz schneit es schwarze Nanopartikel aus Eisenoxid. Sie werden besonders an den Zellwänden in die Lücken zwischen den Fibrillen eingebaut. Es ergibt sich eine Vorzugsrichtung entlang der Holzfasern, in der das Brett mithilfe eines äußeren Magnetfeldes magnetisierbar ist. Die so ausgerichteten Partikel sind fest im Holz eingeschlossen und lassen sich nicht abwaschen.
Tatsächlich gibt es schon eine Küche, in der an solch einer magnetischen Holzwand kleine Küchenmesser kleben bleiben. Sie ist Teil einer "Vision Wood" getauften Versuchswohnung der schweizerischen Materialforschungsanstalt Empa in Zürich, eines der weltweit führenden Holzforschungszentren. Dort leben zwei Doktoranden in einer Wohngemeinschaft und dokumentieren ihre Erfahrungen. Zum Beispiel ist dort auch Holz verbaut, das ganz schwer brennt. Hierfür wird ein Brett zunächst mit einer wässrigen Lösung aus Kohlensäuredimethylester (C3H6O3) und Kalziumchlorid (CaCl2) getränkt. Bei anschließender Behandlung mit Natronlauge bildet sich tief in den Zellstrukturen der feuerhemmende Kalk. Die Brennbarkeit des Holzes sinkt auf etwa ein Drittel.
Forscher der Empa haben gemeinsam mit der benachbarten ETH Zürich auch einen dünnen Film aus Kupfer-Nanodrähten auf eine Holzoberfläche aufgebracht und mithilfe von starken Lichtblitzen zusammenschmelzen lassen. Wieder wurden die dabei entstehenden Nanopartikel vorzugsweise entlang der Holzfasern eingebaut – sie ergeben quasi eine elektrische Leitung und würden es so ermöglichen, Holzoberflächen mit elektrischen Funktionen zu verbinden, etwa in Smart Homes oder Autos. "Können wir die gewünschten Partikel in die Holzzellwände integrieren, sind sie dort gut geschützt", erklärt Mark Schubert von der Empa. Doch sei es eben auch aufgrund des komplexen Aufbaus des Holzes enorm schwierig, sie erst mal dorthin zu bekommen. Ein Weg ist, wie beim magnetischen und feuerfesten Holz mit zwei flüssigen Komponenten zu arbeiten, die erst im Holz reagieren und dort den gewünschten Feststoff produzieren.
Ist das noch Natur?
Wasser als Lösungsmittel ist jedoch nicht immer das Mittel der Wahl, denn es lässt das Holz quellen und erzeugt dadurch kleine Mikrorisse – eher schlecht, wenn das Material nicht nur elektrisch leitend, sondern zusätzlich noch wasserdicht sein soll. Deshalb experimentieren die Empa-Forscher auch mit organischen Lösungsmitteln. Ähnlich wie Timothée Boitouzet bauen sie auf diesem Weg einen Kunststoff auf Mineralölbasis ins Holz ein. Die Polymerisation, also die Ausbildung von langen Ketten, erfolgt erst, wenn die Bausteine bereits im Holz sind. Gestartet wird der Vorgang durch die Zugabe einer weiteren Chemikalie. Vom Erfolg der Züricher Forscher zeugt ein Waschbecken aus Holz, das in der Versuchswohnung dank wasserabweisendem Polymer immer noch wie neu aussieht.
Wasserabweisendes Holzwaschbecken
Im Unterschied zu Boitouzet haben sie das Lignin im Holz belassen. Denn seine Eigenschaften lassen sich ebenfalls nutzen, um dem Rohstoff völlig neuartige Merkmale zu geben. "Gerade dieser Stoff lässt sich sehr vielseitig verändern", erklärt Mark Schubert. Grund sei seine chemische Struktur mit vielen einzelnen Sauerstoff-Wasserstoff-Molekülen. Diese "OH-Gruppen" lassen sich leicht abspalten und durch andere Elemente ersetzen. An der Empa geschieht dies zum Beispiel mit Jod, sodass das Holz plötzlich antibakterielle Eigenschaften aufweist und sich für Türklinken oder Möbel in Krankenhäusern anbietet. Mit anderen Molekülen könnte man Holz auch wasserabweisend machen oder durchgehend einfärben.
Aber ist das wirklich noch Holz? Bleiben bei all den chemischen Umbauten nicht die speziellen Vorteile des Werkstoffs auf der Strecke, zum Beispiel seine Umweltfreundlichkeit? Was passiert etwa mit den synthetischen Lösungsmitteln, die Woodoo zum Auswaschen des Lignins benötigt? Ob sie zurückgewonnen werden, will die Firma nicht sagen. Und wie nachhaltig ist ein Waschbecken aus Holz, wenn dabei Mineralöl ins Spiel kommt?
Holz wird zum Kunststoff gemacht
"Wenn man das Holz quasi zum Kunststoff macht, muss man das kommunizieren und darf es nicht mehr als natürlich und umweltfreundlich bezeichnen", sagt Holzforscher Klaus Richter von der TU München. Dennoch hält er technische Lösungen, die das Holz stark verändern, nicht per se für schlecht. "Die Vorteile des Produkts aus dem modifizierten Holz müssen eben so groß sein, dass es Varianten aus anderen Materialien übertrifft", so Richter. Noch scheint die Wirtschaft daran allerdings Zweifel zu haben. Keine der genannten Empa-Ideen hat bisher zu einer Unternehmensgründung geführt. Gerade die Bauindustrie sei sehr konservativ, beklagen viele Holzforscher. Nur auf dem Luxussegment scheint bisher Bewegung möglich: So vertreibt die Empa-Ausgründung Swiss Ebony heimischen Bergahorn, der durch Hitze und Druck so verdichtet wurde, dass er die Eigenschaften von Tropenholz bekommt. Damit gefertigte Griffbretter von Saiteninstrumenten ersetzen das streng geschützte Ebenholz, und die Klangübertragung lässt sich durch die Prozedur nach Kundenwunsch anpassen.
Besser sieht es hier auf dem zweiten Feld der Holzinnovationen aus, bei dem aus den Bestandteilen von Holz völlig andere Materialien entstehen. Bereits seit fast zwanzig Jahren gibt es Arboform, eine Mischung aus Lignin und Pflanzenfasern, die auf herkömmlichen Spritzgießmaschinen für Kunststoff verarbeitet werden kann und von der Firma Tecnaro aus Ilsfeld bei Heilbronn weltweit vermarktet wird. Der finnisch-schwedische Konzern Stora Enso wiederum bearbeitet die aus dem Holz gelöste Zellulose mechanisch so, dass die Faserstruktur aufbricht und die einzelnen Mikrofibrillen freigibt. Diese winzigen Wollfäden aus langen Zuckermolekülen haben ähnliche Eigenschaften wie Kristalle und lassen sich zu einem Gel verarbeiten. Stora Enso mischt als erstes Unternehmen diese "mikrofibrillierte Zellulose" Kartons bei, um sie stabiler zu machen. Man kann die Verpackungen also dünner machen. Das spart Ressourcen.
Sogar Schaumstoffe aus Holz sind mittlerweile in der Erprobung. Sie sollen als Wärme- und Schalldämmung, als Verpackungsmaterial, aber auch als Filter Verwendung finden – und würden im Gegensatz zu allen auf dem Markt befindlichen Produkten zu 100 Prozent aus Holz bestehen und gut recycelbar sein. Entwickelt hat sie das Fraunhofer-Institut für Holzforschung. Dazu wird das Holz mit Wasser gemischt und sehr fein zermahlen. Die Fibrillen können sich gut ineinander verhaken, das Lignin sorgt für entsprechendes Volumen. Mithilfe von Kohlendioxid kann diese Masse nun wie Eischnee aufgeschlagen werden. Nach einer langen Trocknung entstehen so Hartschaumplatten oder elastische Schaumstoffe.
Aus Holz: Das stärkste Biomaterial der Welt
Das erstaunlichste Produkt aber dürfte eine Entwicklung von Forschern der Technischen Hochschule in Stockholm (KTH) zusammen mit dem Hamburger Forschungszentrum Desy sein. Aus Zellulose haben sie das stärkste Biomaterial der Welt gemacht. Das Material ist achtmal steifer und einige Male zugfester als die Abseilfäden aus natürlicher Spinnenseide, die bisher als das stärkste biologische Material galten. Ausgangsstoff waren die Elementarfibrillen des Holzes. Sie schwammen in einem nur einen Millimeter breiten Kanal zusammen mit entionisiertem Wasser.
Der Trick: Die Fibrillen sind häufig elektrostatisch negativ aufgeladen und stoßen sich ab, sie sind daher leicht beweglich. Durch die Wasserströmung orientierten sich die Fibrillen in Fließrichtung. Am Ende des Kanals neutralisierten die Forscher die elektrostatische Ladung. Nun konnten sich die perfekt ausgerichteten Fibrillen aneinander anlagern und einen festen Verbund bilden. Das Forscherteam hofft, aus den 15 Mikrometer dicken und mehrere Meter langen Fäden bald einen Stoff für praktische Anwendungen weben zu können.
Wenn sich von all diesen Ideen nur ein Bruchteil am Markt wird behaupten können, ist für Klaus Richter von der TU München jedes innovative Projekt die Mühe wert. Denn obwohl Holz der klimaneutrale, nachwachsende Rohstoff schlechthin sei, würde es noch viel zu wenig genutzt. Laut Waldbericht der Holzwirtschaft wächst in fast allen europäischen Ländern mehr Holz nach als gefällt wird. "In den europäischen Wäldern steht genug Holz, um auch einen erhöhten Bedarf zu decken", sagt Richter. Vor allem dann, wenn man auch endlich mehr auf die Ressource Altholz zurückgreifen würde. Als vor drei Jahren die olympische Radrennbahn in München abgerissen wurde, hat er das verwendete Fichtenholz untersucht. "Auch nach 45 Jahren war es in einem guten Zustand", sagt Richter. "Und trotzdem landete es im Ofen."
(bsc)