Der richtige Dreh beim 3D-Druck
Mit einem eigenen 3D-Drucker muss man sich nach wie vor beschäftigen – die Geräte wollen bedient werden, im Wortsinn. Doch die Zahl der neuralgischen Punkte im 3D-Druckprozess ist überschaubar und mit etwas Erfahrung, Geduld und Experimentierfreude bekommt man sie in der Regel in den Griff.
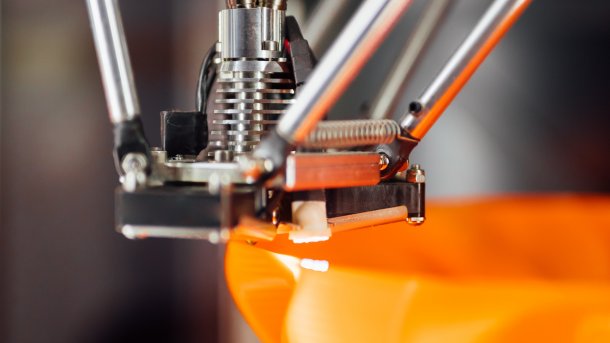
(Bild: Bild: nikkytok/Shutterstock.com)
Aktualisierter Artikel
Dieser Artikel über den Einstieg in den 3D-Druck mit eigenem Gerät erschien zuerst in der Make-Ausgabe 1/15 auf Seite 118. Er wurde zuletzt im September 2019 überarbeitet und aktualisiert.
Jeder 3D-Druck startet mit einem 3D-Datenmodell, das die genaue Geometrie des gewünschten Objekts definiert. Man konstruiert es mit CAD-Software, formt es mit einem 3D-Modellierprogramm, klickt es mit einem kostenlosen Webdienst wie Tinkercad zusammen, holt es sich über einen 3D-Scanner in den Rechner oder lädt es aus einer Online-3D-Datenbank im Internet.
Solche fertigen Vorlagen lädt man in eine spezielle 3D-Druck-Software, die man mit dem Drucker bekommt.Manchmal handelt es sich dabei um frei verfügbare Programme wie Repetier Host oder Cura, in anderen Fällen hat der Hersteller eine proprietäre eigene Software programmiert. Egal, um welche Software es sich handelt, sie bietet eine 3D-Ansicht der Bauplattform, die man mit seinen Vorlagen bestückt. In der Regel kann man die Objekte skalieren. Das ist oft nötig, denn die Raumkoordinaten sind in gängigen 3D-Formate wie OBJ und STL nicht an Einheiten gekoppelt. Wenn ein angelsächsischer Konstrukteur sein Objekt in Zoll entworfen hat, die eigene Druckersoftware aber in Millimetern rechnet, muss man oft ziemlich heranzoomen, um das 3D-Modell auf der Bauplattform überhaupt zu entdecken. Skalieren mit dem Faktor 25,4 schlägt hier die Brücke zwischen den Maßsystemen.
Schräge Überhänge der 3D-Vorlage bewältigen die meisten 3D-Drucker problemlos, bis etwa 50 Grad gegenüber der Senkrechten. Was noch flacher vorspringt oder gar größere Lücken überspannen soll, muss gestützt werden. Die Druckersoftware fügt hierfür automatisch Stützstrukturen ein, in manchen Programmen – etwa Cura – muss man diese Funktionen allerdings erst einschalten. Die Stützen sollen möglichst wenig Material verbrauchen, optimal stützen und sich später leicht vom Werkstück trennen lassen, insbesondere dann, wenn der Drucker nur einen Kopf hat und deshalb die Stützen aus demselben Material druckt wie das Objekt selbst.
Die Stützstrategie kann man der Druckersoftware in der Regel detailliert vorgeben: Parameter regeln unter anderem, ab welchem Winkel überhaupt unterfüttert wird, ob die Hilfsstrukturen nur auf Basis des Drucktisches errichtet werden oder auch auf dem Werkstück selbst ("internal support"). Zu viele Stützen machen die Nachbearbeitung mühsam, an manche kommt man auch gar nicht mehr ran, um sie zu entfernen. Bei kleinen Objekten lohnt es sich oft, einfach mal das Risiko einzugehen und sie ganz ohne Stützen zu drucken – mehr als ein Fehldruck kann dabei nicht passieren und manchmal tragen sich auch reichlich luftig anmutende Konstruktionen erstaunlicherweise fast von selbst.
Von Anfang an
Einen grundlegenden Artikel, wie 3D-Druck überhaupt funktioniert, finden Sie ebenfalls auf unserer Webseite.
Schmelzschicht
In diesem Artikel dreht sich alles um 3D-Drucker, die mit Schmelzschichtung arbeiten (Fused Deposition Modeling, FDM), so wie beinahe alle günstigen 3D-Drucker. Wie sich stattdessen eine Stereolithographiemaschine anfühlt, die mit Laserlicht Kunstharz härtet, lesen Sie ebenfalls auf unserer Webseite.
Scheibchenweise
Wenn in der 3D-Voransicht alles sitzt und passt, zerlegt die Software die Vorlagen in lauter hauchdünne horizontale Scheiben wie ein Gurkenhobel das Gemüse. Das dafür zuständige Modul der Druckersoftware wird Slicer genannt, ist oft ein eigenes (Unter-)Programm und manchmal sogar austauschbar.
Experimente mit den üblicherweise zahlreichen Parametern des Slicers zahlen sich oft aus. Die wichtigste Stellschraube ist die horizontale Schichtdicke. Auf wie wenige Millimeterbruchteile man die drücken kann, hängt nicht nur von der Mechanik und Elektronik ab, sondern ist auch eine Software-Frage – wir haben in der Vergangenheit schon erlebt, dass ein 3D-Drucker nach einem Firmware- und Software-Update auf einmal 0,1 Millimeter dünn statt wie bisher minimal in 0,2-Millimeter-Schichten drucken konnte.
Der typische 3D-Druck besteht aus einer soliden Hülle, während sein Inneres nur mit einer losen Struktur gefüllt ist ("Infill"). Deren Dichte gibt man gewöhnlich in Prozent an – mit den voreingestellten Standardwerten zwischen 10 und 30 Prozent kann man hier selten etwas falsch machen. Die massiv gedruckte Hülle besteht typischerweise aus drei Schichten, auch das ist in der Regel völlig in Ordnung. Wer hingegen ein besonders leichtes und materialsparendes Objekt oder ein strapazierfähigeres braucht, findet bei diesen Parametern ein weites Betätigungsfeld. Manche Software möchte Wand- und Bodenstärken in Millimeter angegeben bekommen.
Software-Alternativen
Bei manchen 3D-Druckern ist man auf die mitgelieferte Software des Herstellers angewiesen. Bei anderen stehen kommerzielle oder kostenlose Programme als Alternative zur Wahl, zum Beispiel Cura, Repetier Host oder Simplify3D.
X, Y und Z
Bei allen 3D-Druckern entfernen sich Kopf und Tisch im Lauf des Drucks parallel zur Z-Achse voneinander; die X- und Y-Achse liegen parallel zum Tisch. Die mechanische Umsetzung variiert dagegen stark von Modell zu Modell: Während die einen den Kopf in der horizontalen Ebene bewegen und den Tisch nur nach unten fahren, steigt bei anderen der Kopf in die Höhe und der Tisch pendelt sowohl nach links und rechts wie vor und zurück. Unserer Erfahrung nach gibt es keine ideale Anordnung der Achsen und ihrer Antriebe. Für die mechanische Auslegung eines 3D-Druckers scheint eher wichtig zu sein, ob die Maschine etwa möglichst kompakt, leicht zu erweitern oder zu warten sein soll.
Beschränkte Haftung
Löst sich ein Objekt beim 3D-Druck vom Tisch, ist es unrettbar im Eimer. Der Slicer bietet meist einige Optionen, die für erhöhte Haftung sorgen sollen. Lässt man die Maschine die erste Schicht auf dem Tisch dicker drucken – etwa 0,3 Millimeter statt 0,2 Millimeter in den oberen Schichten – gleicht das einen minimal zu großen Abstand zwischen Düse und Tisch bei Druckbeginn aus.
Eine "Brim" (engl.: Krempe) verbreitert schlicht die Basis des Objekts, indem dessen unterste Schicht dicht an dicht mit weiteren Materialbahnen umgeben wird – diese Maßnahme ist bei hohen Objekten mit kleiner Grundrissfläche angezeigt. Ein "Raft" (engl.: Floß) besteht aus meist drei Gitterlagen, die auf dem Drucktisch erst mal eine Bauplattform bilden, auf der dann das Objekt selbst aufgeschichtet wird. Es ist aufwendiger, liefert aber viel mehr Sicherheit als eine Brim und ist auch bei Druckern nützlich, bei denen sich der Abstand zwischen Düse und Tisch bei Druckbeginn nicht zuverlässig justieren lässt. Nicht jede Software bietet beide Optionen, manche haben noch andere oder verwenden zumindest andere Bezeichnungen.
Sind die Parameter gewählt und hat der Slicer die Vorlagen portioniert, berechnet die Software für jede Schicht erst die geometrische Bahn, die der Druckkopf später beschreiben muss, dann wird das ganze in Maschinensteuercodes (Gcode) heruntergebrochen. Der wandert dann entweder über ein USB-Kabel, einen Stick oder eine SD-Karte in den Drucker, der nach dem Startbefehl und der benötigten Vorheizzeit sein Werk beginnt.
Bohrung
Viele Druckerhersteller geben den Durchmesser der Düse an – dieser ist etwas größer als die maximale horizontalen Schichtdicke, die die Maschine drucken kann. Je feiner eine Düse ist, desto schmalere Materialbahnen kann sie innerhalb einer Schicht anlegen. Der Druck verlängert sich aber dadurch, weil ja nur weniger Material pro Zentimeter Weg aufgebracht werden kann. Eine feine Düse verstopft zudem schneller und ist schwieriger wieder frei zu bekommen: Mit einem 0,2-Millimeter-Stahldraht lässt sich nicht so viel Druck ausüben wie mit einem mit 0,4 Millimeter Durchmesser. Ist eine Düse nach einem ABS-Druck verstopft, hilft es oft, sie auszubauen, vollständig abkühlen zu lassen und über Nacht in Aceton zu legen. PLA löst Aceton leider nicht.
Was bringt der Doppelkopf?
Die teuren 3D-Drucker der Einsteigerklasse heben sich von den günstigen Geräten oft dadurch ab, dass sie statt einer Druckdüse zwei oder sogar noch mehr im Druckkopf sitzen haben und deshalb eine Schicht des Objekts aus mehreren Materialien zusammensetzen können. So lässt sich das eigentliche Modell beispielsweise aus ABS oder PLA drucken, die Stützen aber aus einem anderen Material, das sich hinterher in einem Wasser- oder Laugenbad auflöst.
Das klingt erst einmal sehr vielversprechend. Unserer Erfahrung nach kann man allerdings die meisten Objekte entweder ganz ohne oder nur mit leicht entfernbaren Stützen drucken – dafür braucht es keinen Doppelkopf. Beim Druck mit nur einem Material ist eine fest im Druckkopf angebrachte zweite Düse manchmal sogar kontraproduktiv: Da sie nur wenige Zentimeter neben ihrem Zwilling und mit ihm exakt auf derselben Höhe sitzt, kratzt sie oft direkt über die frisch aufgeschmolzene Schicht. Hat man Pech, löst sich dabei das mühsam aufgeschichtete Objekt von der Plattform und der Druck ist gelaufen. Die radikale Lösung: Wer die zweite Düse ohnehin nicht nutzt, kann sie meist recht einfach abschrauben.
Die 3D-Drucker-Hersteller beschreiten mittlerweile aber neue Wege, um den Doppelkopfdruck (auch Dual Extrusion genannt) praktikabel zu machen. Beim Ultimaker 3 beispielsweise zieht sich die gerade nicht genutzte Düse ein Stück in den Druckkopf zurück. Beim Bolt von Leapfrog hingegen sind die Köpfe in einer Dimension voneinander unabhängig positionierbar; der jeweils nicht genutzte Kopf zieht sich auf seine Seite zurück. Beide Konstruktionen erfüllen ihren Zweck, sind aber mechanisch weit aufwändiger als ein konventioneller, starrer Doppelkopf und daher derzeit nicht in preiswerten 3D-Druckern zu haben.
Biege machen
Ob dann alles klappt, hängt wesentlich vom Material ab – üblich sind bei FDM-Druckern ABS und PLA (zu den exotischeren druckbaren Stoffen siehe Make 2/19, Seite 8). PLA sondert unseres Wissens keine giftigen Dämpfe ab, wenn es heiß wird, es verzieht sich wenig beim Abkühlen und man kann es aus nachwachsenden Rohstoffen herstellen. Es heißt, dass es langfristig unter UV-Bestrahlung leiden und im Lauf der Zeit sogar kompostieren soll – ob das ein Vorteil oder Nachteil ist, sei mal dahingestellt. An unseren bisher aus PLA gedruckten Objekten konnten wir jedenfalls noch keine Zersetzungsprozesse feststellen, allerdings stammen die ältesten erst aus dem Jahr 2011 und keines davon war seitdem Wind und Wetter ausgesetzt.
Beobachtet haben wir allerdings, dass manches unverarbeitete PLA-Filament von der Rolle zum Teil nach ein oder zwei Jahren Lagerzeit nicht mehr gut zu verwenden war: Der Plastikdraht zeigte winzige Querrisse, brach leicht und aus dem Druckkopf kamen ungewohnt dünne Fädchen – ob das hygroskopische Material mit der Zeit zu viel Feuchtigkeit aufgenommen hat oder eher ausgetrocknet ist, wissen wir nicht. Der Effekt fiel uns meist (aber nicht immer) bei halbtransparenten PLA-Sorten auf.
ABS hingegen druckt sich noch nach Jahren wie am ersten Tag. Beim Erhitzen wird allerdings Styrol frei, was mäßig giftig ist. Ist für ausreichend Lüftung gesorgt, bleibt das größte ABS-Problem: Beim allmählichen Abkühlen der älteren Materialschichten bauen sich Spannungen im Werkstück auf, die es verbiegen ("Warping"), was oft dazu führt, dass sich Objekte vom Drucktisch lösen, sei der auch noch so gut beheizt und speziell beschichtet – ob mit Kapton-Tape oder blauem Malerkrepp beklebt oder einfach mit Klebestift eingestrichen.
Was ABS-Drucke nach unserer Erfahrung noch am zuverlässigsten am Boden hält, ist die von der Firma PP3DP für ihre UP-Drucker verwendete Lochrasterplatte. Diese besteht aus hitzebeständigem Kunststoff, der Platinenmaterial ähnelt. Beim Druck der ersten Schicht dringt ABS etwas in die Löcher ein, das abkühlende Material verzahnt sich mit der Grundplatte. Kombiniert man diese mit einem Raft, klappt der ABS-Druck fast immer. Allerdings erfordert es etwas Übung und manchmal ziemliche Kraft, das abgekühlte Objekt von der Grundplatte zu trennen.
ABS oder PLA?
Manchmal liest man, ABS wäre stabiler als PLA – das können wir aus unseren Erfahrungen weder bestätigen noch durch eine systematische Untersuchung widerlegen. Entscheidender dürfte für die meisten Anwendungen sein, dass PLA bereits bei etwa 70 Grad weich wird und seine Festigkeit verliert – Kaffeetassen kann man daraus nicht drucken.
Geschlossener Raum
3D-Drucker mit geschlossenem Bauraum sollten eigentlich weniger Probleme mit Spannungen bei ABS haben, weil die Objekte im Inneren wärmer gehalten werden. In unseren eigenen 3D-Druckertests hat sich das bisher aber nicht bemerkbar gemacht.
Die hohe Schule
Natürlich bietet manche 3D-Drucker-Software noch viel mehr Regler und Raffinessen. Recht verbreitet ist etwa die Option, den Druck bei einer vorab bestimmten Schicht eine Pause einlegen zu lassen – dann kann man etwa eine Mutter in eine passende Aussparung setzen, die im weiteren Druck formschlüssig ins Objekt integriert wird.
Kein Grund zum Innehalten ist hingegen für die meisten 3D-Drucker, wenn ihnen das Material ausgeht – das bekommen sie schlicht nicht mit. Passiert das, während die Maschine ohne Aufsicht läuft, zeichnet der Kopf seine vorbestimmten Werkzeugbahnen in die Luft und wird dabei stets weiter beheizt. Meistens ist die Düse anschließend von verbrannten Materialresten verstopft.
Manche Hersteller sinnen auf Abhilfe: Während die einen auf proprietäre Materialkartuschen setzen, die Drucker und Software anhand eines Chips unterscheiden und über deren Füllstand sie Buch führen, ging MakerBot Industries das Problem mit seinem "Smart Extruder" an: Der sollte kontrollieren, ob noch Material in den Druckkopf gespult wird. Falls nicht, soll er den Druck unterbrechen wie ein Kopierer, dem das Papier ausgeht.
Auch wenn das in unserem Test der fünften Maschinengeneration von MakerBot zuverlässig funktionierte, verbringen wir dennoch möglichst viel Zeit in der Nähe unserer 3D-Drucker, wenn sie Dinge materialisieren. Um sie zu bedienen. Um sie zu beobachten und um Erfahrungen zu machen, die wir weitergeben können.
()