Solar cells: How flexible films should open up previously unused areas
Optimized manufacturing process should help reduce the cost of increasingly efficient, flexible organic solar cells.
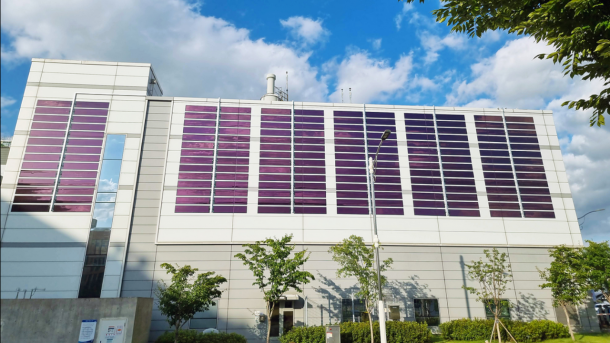
The German company Heliatek in Dresden equipped a building from the Samsung Advanced Institute of Technology in South Korea with 168 solar foils and with more than 8 kWp.
(Bild: Heliatek)
(Hier finden Sie die deutsche Version des Beitrags)
The intensive expansion of solar power plants worldwide today is based on the dominance of silicon solar cells. The market is dominated by modules with efficiencies of well over 20 percent. At the same time, solar cells based on perovskite materials continue to celebrate new records: currently, the best perovskite cell is 25.7 percent, and in tandem with a silicon cell it is as high as 31.3 percent, according to the National Renewable Energy Laboratory NREL. Flexible organic solar cells have attracted less attention in recent years. But thanks to new materials and optimized manufacturing processes, significant progress has been made in this field as well.
Organic solar cells form the basis for flexible solar films. The German company Heliatek in Dresden, for example, equipped a building of the Samsung Advanced Institute of Technology in Gyeonggi-do in South Korea with 168 solar films at the beginning of November. Covering an area of 147 square meters, these films deliver 8.4 kilowatts of power with an efficiency of just under ten percent. Other installations, for example on a wind turbine tower in Spain or a round storage tank at a combined heat and power plant in Marburg, Germany, show that the flexible films can also be used to transform unusual, previously unused surfaces into small solar power plants.
Efficiency improvements for solar films
These solar films, which are a good ten times lighter than silicon modules, have a great chance of achieving higher efficiencies. Just under two years ago, a Chinese-American working group led by Bryon W. Larson of the National Renewable Energy Laboratory in Golden broke through the 18 percent mark. The main reason for this increase was not the photovoltaically active substances, but new donor and acceptor materials. These ensure that excitons - pairs of electrons and electron holes - generated by sunlight can be split more efficiently into their components, i.e. charge carriers that can be used to generate solar electricity. The current record value is 18.2 percent, achieved by researchers at Beihang University and Shanghai Jiao Tong University.
However, it is still a long way from a solar cell in the laboratory to a usable solar module. But here, too, a current approach by a German-Chinese team raises hope. The group led by Jie Min from Wuhan University, with the participation of Christoph Brabec from the University of Erlangen-Nuremberg, optimized a process to apply the individual layers of an organic solar cell to a carrier material more quickly and efficiently. In principle, their process allows production rates of up to 30 meters of solar film per minute. Until now, only two meters per minute have been considered standard. The efficiency of the solar cells produced in this way is also impressive, at just under 18 percent.
If these advances can be translated into an industrial production process, flexible solar films will be able to expand their currently still vanishingly small market share. If the production costs are also significantly lower than those of silicon modules, wider use, for example on house facades or on vehicles, would be entirely possible. In any case, the demand for lightweight, inexpensive and nevertheless efficient solar modules for this building- or vehicle-integrated photovoltaics is growing steadily.
(jle)