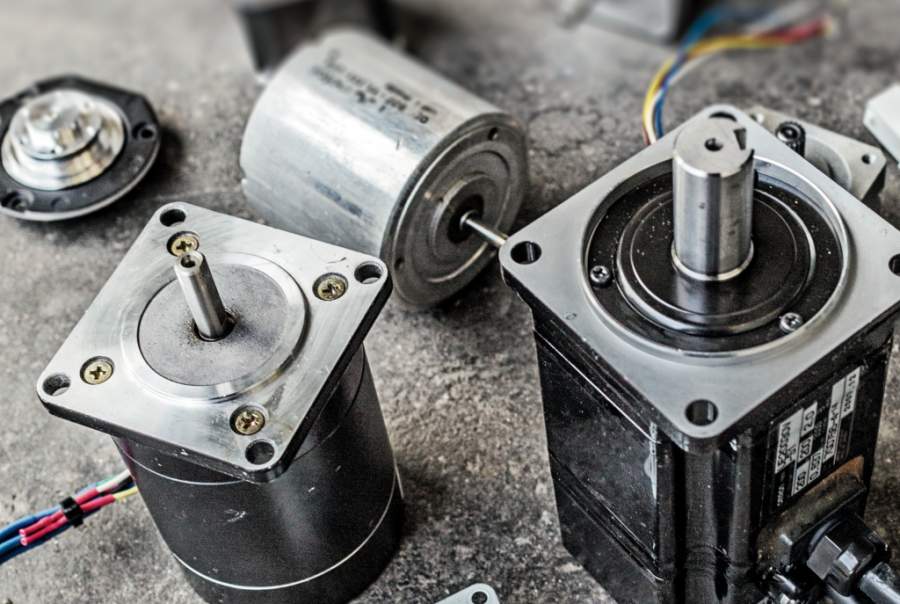
Motoren und Antriebe
Kaum zu glauben: Die ersten Elektromotoren drehten sich schon vor 190 Jahren, aber es dauerte noch Jahrzehnte, bis sie erste praktische Anwendungen erfuhren. Heute hat man eher die Qual der Wahl, für ein Antriebsproblem den passenden Motor zu finden. Wir geben einen Überblick der für Maker interessanten Motorvarianten.
Das Prinzip des Gleichstrommotors hatte schon 1820 der dänische Physiker Hans-Christian Ørstedt verstanden: Ein stromdurchflossener Leiter erzeugt ein Magnetfeld, das auf Eisen und andere Magnete eine Kraft ausübt. So richtig anzuwenden wusste dies erst der Deutschrusse Moritz Herrman von Jacobi, der den ersten praxistauglichen Elektromotor baute und ihn auch gleich als Antrieb für ein Boot verwendete: 1838 schipperte er damit auf der Newa bei Sankt Petersburg herum. Sein batteriebetriebener 200-W-Motor wies mit Kommutator, Feld- und Erregerwicklung schon deutliche Merkmale heutiger Universalmotoren auf.
Viele Erfindungen jener Zeit verschwanden wieder schnell – etwa das Kravogl-Kraftrad von 1867, bei dem der Anker durch Schwerkraft in Position gehalten wird, oder der Egger-Elektromotor von 1875, der den Hub von Elektromagneten über eine Kurbelwelle in Drehbewegung umsetzt. Andere Entdeckungen wie der Homopolarmotor sind heute noch bekannt, fristen aber mangels Wirkungsgrad eher ein Schattendasein oder sind Gegenstand verschwörungstheoretischer Betrachtungen.
Auch wenn der erste Elektromotor eigentlich ein Universalmotor mit Reihenschluss-Erregung (dazu später) war, beginnen wir hier mit dem permanenterregten Gleichtrommotoren – das ist der klassische DC-Motor, für viele Bastler der Erstkontakt mit der Elektrotechnik. Auch er gehört zu den älteren Konstruktionen – weil man zu Zeiten seiner Erfindung ja nur auf galvanische Elemente (Batterien) als Stromquelle zurückgreifen konnte.
Gleichstrommotoren
Der DC-Motor mit Permanentmagneten ist nach wie vor die meistgebaute Motorenausführung, weil er so einfach herzustellen und robust ist. Die Anwendung reicht vom winzigen Vibrationsmotor im Smartphone über Spielzeuge bis zum Kühlerventilator im Auto; oft ist er auch in Maschinen zu finden, wenn eine einfache Drehzahlregelung gewünscht ist und man sich den Aufwand für einen Frequenzumrichter sparen will.
Man erkennt ihn leicht am charakteristischen Trommelanker, der von feststehenden Permanentmagneten umgeben ist – im einfachsten Fall Halbschalen aus billigem Ferritmaterial. Der Strom wird dem Anker über Schleifkontakte (so genannte Bürsten) zugeführt. Dabei sorgt der Kommutator (auch Kollektor oder Polwender genannt) dafür, dass der Strom immer jene Spulen erreicht, die als nächste vom Dauermagnet-Paar angezogen werden.
Permanenterregte Gleichtrommotoren lassen sich ohne weiteres als Generator einsetzen; man braucht noch nicht einmal einen Gleichrichter, weil diese Aufgabe der Kommutator erledigt. Idealerweise erzeugt ein 12-V-Motor, der von außen mit Nenndrehzahl angetrieben wird, auch ebendiese 12 V.
Das bringt uns gleich zu einer elementaren Erkenntnis: Ein idealer Elektromotor würde im Leerlauf gar keinen Strom aufnehmen, weil er ja genau die gleiche Spannung selbst erzeugt („Gegen-EMK“, siehe Kasten), die er für die momentane Drehzahl benötigen würde. Umgekehrt wird der ideale Motor im blockierten Zustand unendlich viel Strom aufnehmen. Das gilt im Prinzip für alle Bauarten!
Aus dem gleichen Grund verringert (!) sich die Drehzahl eines Motors, wenn man die Magnete stärker auslegt: Durch das stärkere Magnetfeld wird im Anker eine höhere Gegen-EMK erzeugt, somit erreicht der Motor das Gleichgewicht aus versorgender Spannung und Gegen-EMK schon bei geringerer Drehzahl. Mit der Stärke des Magnetfeldes steigt indes das erzielbare Drehmoment.

Die Drehzahl lässt sich somit einfach über die angelegte Spannung steuern – dieses Wissen ist sozusagen Kulturgut: Weil batteriebetriebene Spielzeuge mit erlahmenden Zellen immer langsamer werden, weiß dies schon jedes Kind. Eine analoge Spannungseinstellung (zum Beispiel mit einem Transistor als variablem „Vorwiderstand“) ist von der Energiebilanz allerdings wenig erbaulich: schließlich muss der einem Motor vorgeschaltete Spannungsregler die momentan nicht benötigte Leistung in Wärme „verbraten“. Von ganz einfachen Anwendungen abgesehen bedient man sich deshalb heute durchweg der Pulsweitenmodulation (PWM). Statt eines Reglers kann hier ein einfacher Schalttransistor zum Einsatz kommen – weil an dem praktisch nur eine vernachlässigbare Spannung abfällt, ist die Verlustleistung gering.
PWM hört sich schlimmer an, als sie ist: Eine Elektronik schaltet den Motor wiederholt für eine bestimmte Zeit komplett ein und für eine ebenfalls bestimmte Pausenzeit komplett aus. Macht man dies nur schnell genug hintereinander – ein paar hundert- bis tausendmal pro Sekunde – bestimmt das Verhältnis von Ein- und Ausschaltzeit die Drehzahl. Der Motor „sieht“ dann nur eine mittlere Spannung, weil er den schnellen Ein-Aus-Folgen aufgrund seiner Trägheit nicht folgen kann. Einziger Nebeneffekt: der Motor kann im Teillastbereich merklich summen oder pfeifen. Der PWM werden wir im Folgenden noch öfter begegnen.
Ausführungen mit nur zwei (halben) Ankerwicklungen (und somit der Pole auf dem Kommutator) findet man eigentlich nur in Elektro-Experimentierkästen – diese haben nämlich den Nachteil, dass sie in einer bestimmten Ankerstellung nicht selbst anlaufen. Praktische Ausführungen haben daher immer mindestens drei Wicklungen, bessere fünf oder noch mehr. Je höher die Anzahl der Ankerwicklungen (und damit Pole auf dem Kommutator), desto gleichmäßiger ist der Drehmomentverlauf über eine Umdrehung und desto ruhiger läuft der Motor.
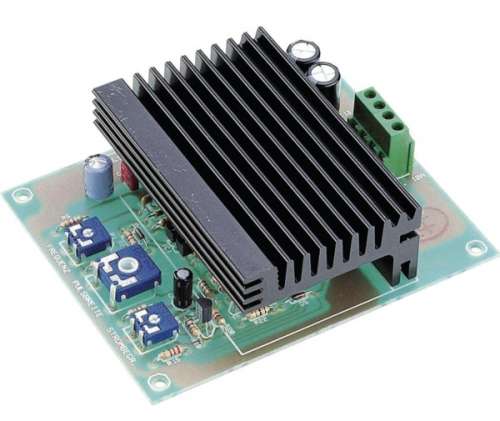
Die einfache Bauart bringt einige Nachteile mit sich: Die auf dem Kommutator schleifenden Bürstenkontakte führen zu Verlusten durch Reibung und Übergangswiderstände sowie zu einem störenden Laufgeräusch. Außerdem entstehen am Kommutator Abrissfunken, die Empfangsprobleme bei allen Funkwellenempfängern auslösen können. Bei DC-Kommutatormotoren muss man daher immer ein Entstörfilter vorsehen; oft reichen schon 100-nF-Kondensatoren von jedem der beiden Anschlüssen zur Gehäuseschale.
Dass der Motor im Stillstand eine gewisse „Selbsthemmung“ durch die den Anker anziehenden Dauermagnete aufweist, kann für die jeweilige Anwendung von Vor- oder von Nachteil sein. In Eisenbahnmodellen zum Beispiel führt die Selbsthemmung dazu, dass das Modell bei Spannungsunterbrechung abrupt stehenbleibt und nicht sanft ausläuft. Akkuschrauber-Motoren dagegen werden oft durch Kurzschließen zusätzlich abgebremst, damit sie beim Loslassen des „Gashebels“ möglichst schnell zum Stillstand kommen.
Die Selbsthemmung vermeiden die so genannten Glockenankermotoren: Durch eine spezielle Wickeltechnik besteht der Anker hier nur aus der in Kunstharz eingebetteten Spulenwicklung und kommt ohne Eisenkern aus. Schaltet man bei einem Glockenankermotor den Strom ab, läuft er gemütlich aus – vorausgesetzt natürlich, dass man die Motorklemmen beim Abschalten nicht kurzschließt.
BLDC-Motoren
BLDC ist die Abkürzung von „Brushless Direct Current“, also eine Motorenbauart ohne Kommutator und Schleifkontakte. Wicklung und Dauermagnet-Anordnung unterscheiden sich im Prinzip nicht vom DC-Motor, wohl aber die Art der Spannungsversorgung. Während beim normalen DC-Motor der Kommutator für ein ständiges Umschalten der zu aktivierenden Wicklungen sorgt, muss dies beim BLDC eine externe Elektronik besorgen. Das ist zwar aufwendiger, spart aber die verschleißträchtigen Bürstenkontakte und deren Reibungsverluste.

Die Elektronik muss natürlich wissen, in welcher Stellung sich der Anker gerade befindet. Der klassische BLDC verwendet dazu drei Magnetfeldsonden, so genannte Hall(effekt)-Sensoren, die bei Erreichen eines bestimmten Magnetfeldes durchschalten und die Stellung der Ansteuerelektronik melden. Die muss dann eigentlich nur das tun, was der Kommutator in der gleichen Situation auch täte: die passenden Wicklungen („Stränge“) unter Strom setzen. Ein auf diese Weise kommutierter Motor verhält sich dann auch exakt wie ein Gleichstrommotor – nur ohne die angeführten Nachteile.
Weil man die Sensoren nicht mitrotieren lassen will – in diesem Fall bräuchte man doch wieder Schleifkontakte – lässt man nicht die Elektromagnete mitsamt Sensoren rotieren, sondern die Dauermagnete. Dies führt zu der bei Modellbauern bekannten Ausführung mit Außenläufer, das heißt, eine Schale mit den Magneten rotiert um den nun feststehenden Anker (oft als „Outrunner“ bezeichnet). BLDCs in E-Bikes sind dagegen meist Innenläufer, weil hierbei das Anflanschen eines Planetengetriebes einfacher ist.
Eine weit verbreitete Bauform ist die des Scheibenläufers, beliebt für Spindelantriebe in Disketten- und CD-Laufwerken. Hier befinden sich die Magnete auf einer Scheibe, die mit der Welle verbunden ist. Die Spulen sind als Flachwicklung ausgeführt und können zum Beispiel direkt auf die Platine mit der Ansteuerelektronik geklebt werden, ebenso wie die Hall-Sensoren.
Praktischerweise nutzt man die transistorisierte Schaltstufe auch gleich, um den Strangstrom mit einer Pulsweitenmodulation zu beaufschlagen; der Mehraufwand hierfür ist minimal. Die Ansteuerelektronik kann also Kommutierung und Drehzahlsteuerung gleichzeitig erledigen. Dazu braucht man keineswegs einen Mikroprozessor: Eine erste Anwendung von bürstenlosen Motoren in der Konsumelektronik waren direktangetriebene Plattenspieler, die Ende der 1970er Jahre aufkamen. Die Ansteuerung war hierbei noch völlig diskret mit ein paar Transistoren aufgebaut.

Sensor-kommutierte BLDCs werden zum Beispiel in PC-Lüftern oder Industrie-Servomotoren eingesetzt, ebenso als Antrieb in E-Bikes oder elektrischen Rollstühlen. Wie ein normaler Gleichstrommotor erlauben sie eine Drehzahlsteuerung von Null an, die Drehrichtungsumkehr erfolgt durch Ändern der Kommutierungsfolge – dazu reichen in paar Logik-Gatter oder einige Zeilen Code, sofern die Ansteuerung ein Mikrocontroller erledigt.
Sensorless BLDC
Den zusätzlichen Bauteile- und Verdrahtungsaufwand für die Hall-Sensoren möchte man gern vermeiden. Die Weiterentwicklung des BLDCs waren vor einigen Jahren deshalb die sensorlos kommutierten BLDCs, wie sie heute jeder Multikopter-Erbauer kennt.
Dank des Einsatzes von Mikrocontrollern ist es möglich, bei der gerade abgeschalteten Wicklung die dort durch das vorbeihuschende Dauermagnetfeld erzeugte Spannung (Gegen-EMK) zu messen (beziehungsweise mit einem Referenzwert zu vergleichen) und daraus den Wicklungs-Umschaltzeitpunkt abzuleiten. Das funktioniert bei laufendem Motor bis in höchste Drehzahlen überraschend gut, hat aber einen Nachteil: Wenn der Motor steht oder sehr langsam läuft, gibt es auch keine (oder nur eine zu geringe) induzierte Spannung in der abgeschalteten Spule, die man auswerten könnte.

Der BLDC-Controller muss den Motor daher vom Stillstand ausgehend zunächst „blind“ schalten, indem er bei ganz niedriger Spannung (bzw. einem sehr kleinem PWM-Tastverhältnis) ein niederfrequentes Drehfeld anlegt, den Motor also wie eine Art Synchron- oder Schrittmotor betreibt. Erst wenn er dann „Tritt gefasst“ hat und genügend Gegen-EMK liefert, kommt die elektronische Kommutierung zum Einsatz. Das ist der Grund dafür, warum Modellbau-BLDCs unter Last nur stotternd anlaufen und sich praktisch nicht unter eine Mindestdrehzahl steuern lassen.
Servo-Antriebe (dazu später) und höherpreisige BLDC-Controller beaufschlagen die zur Auswertung herangezogene Wicklung mit kurzen Stromimpulsen; anhand des Ausschwingverlaufs kann der auswertende Prozessor dann die Ankerstellung berechnen.

Es ist ausgesprochen lehrreich, einmal einen BLDC-Controller „zu Fuß“ aufzubauen. Die hier abgedruckte Schaltung entstammt einer Idee von Ulrich Radig, wir haben für einfachere Experimente und leichte Zugänglichkeit der Messpunkte allerdings nur bedrahtete Bauteile verwendet und die serielle Schnittstelle statt I2C zur Drehzahl-Steuerung eingestellt. Die Sourcen lassen sich mit dem AVR-GCC kompilieren, als Plattform eignet sich auch ein Arduino. Die Schaltung funktioniert übrigens auch mit Motoren, die mit Hall-Sensoren ausgestattet sind; die werden einfach nicht angeschlossen.

Die Spannungsteiler für die Messung der Gegen-EMK (R17, R13, R19 sowie R18, R12, R5) sind für Betriebsspannungen bis 12 V ausgelegt. Bei höheren Motorspannungen ist das Teilerverhältnis zu erhöhen – beispielsweise, indem man die Werte 4k7 und 10k miteinander verstauscht. Die Eingangsspannungen B_EMF und SUM_UVW dürfen in keinem Fall höher als 5 V liegen.
Besonders gewiefte BLDC-Kenner findet man übrigens in einschlägigen Modellbauforen – dort werden Motoren für Wettbewerbsvorteile auch mal umgewickelt oder gar von Grund auf selbst konstruiert; gleiches gilt für die BLDC-Controller. Es fließen dann gern neue Ideen und Entwicklungen ein – etwa mit einer sinusförmigen Motorstrom-Ansteuerung anstelle des einfachen An- und Abschaltens der Wicklungsstränge (Sinus- statt Blockkommutierung).
Universalmotoren
Den Universalmotor findet man in den unterschiedlichsten Anwendungsbereichen – in der Märklin-Lokomotive genau so wie im Staubsauger oder der Handbohrmaschine. „Universal“ heißt er aber deshalb, weil er an Gleichstrom und Wechselstrom gleichermaßen betrieben werden kann.

Sein Aufbau ähnelt dem DC-Motor, allerdings wird das Magnetfeld im Stator nicht durch Dauermagnete erzeugt, sondern über eine Spulenwicklung, die (zumindest bei den uns interessierenden Motoren) in Reihe zu den Kommutator-Anschlüssen (Bürsten) geschaltet ist. Man nennt diese Wicklung auch Erreger- oder Feldwicklung. Bei einer Umpolung der Versorgungsspannung wechselt sowohl die Richtung des Erreger- wie auch des Anker-Magnetfelds, so dass das Drehmoment unabhängig von der Polarität des Stromes immer in die gleiche Richtung wirkt.
Um eine einfache Drehzahlsteuerung zu erreichen, ist zum Beispiel im Küchenmixer die Stator-Feldwicklung mit mehreren Anzapfungen versehen. Hier macht man sich den Effekt der so genannten Feldschwächung zu nutze (siehe Kasten „Gegen-EMK“). Das Wicklungsende mit den meisten aktiven Windungen ist die kleinste Drehzahlstufe. Durch das hierbei sehr kräftige Erregerfeld erzeugt der Motor auch bei kleiner Drehzahl genügend Drehmoment.
Will man die Laufrichtung eines Universalmotors umdrehen, muss man entweder die Anschlüsse der Feldwicklung oder die des Ankers (also der Bürsten) miteinander vertauschen. Bei klassischen Märklin-Lokomotiven zum Beispiel geschieht dies durch Umschalten der zweiteiligen Feldwicklung – beide Hälften sind gegensinnig gewickelt.
Größere Universalmotoren lassen sich mit einem Phasenanschnitt-„Dimmer“ problemlos in der Drehzahl steuern, solange dieser für induktive Lasten ausgelegt ist. Das Drehmoment ist bei kleinen Drehzahlen aber merklich kleiner als bei einer Drehzahlsteuerung über die Feldwicklung.
Synchronmotoren
Während die Synchronmaschine im Maschinenbau ein gern verwendeter Antrieb ist, findet man sie im kleinen Maßstab eher selten – und dann auch nur in vereinfachter Bauform mit unmagnetischem Anker (als so genannter Reluktanzmotor). In ihnen richtet sich der Anker mit jeder Halbwelle des (Netz-)Wechselstroms in einer bestimmten Position aus, die nächste Einrastposition liegt um einen bestimmten Winkelschritt weiter. Die Drehzahl ist daher absolut starr mit der Netzfrequenz verkoppelt.
Einphasige Synchronmotoren laufen in unbestimmter Richtung oder gar nicht an, wenn man nicht besondere Vorkehrungen (also eine Anlaufhilfe) vorsieht. Berühmt ist zum Beispiel der Synchronmotor in alten Hammond-Orgeln, der den mechanischen Tongenerator mit der geforderten Drehzahl- und damit Frequenzkonstanz antreibt. Er wird zunächst mit einem manuell zugeschalteten Spaltpolmotor auf Touren gebracht und rastet dann auf der Netzfrequenz ein.

Kleine einphasige Synchronmotoren findet man zum Beispiel im Drehteller-Antrieb von Mikrowellen-Herden, in kleinen Aquarienpumpen und in Spiegelkugel-Antrieben. Leistung und Wirkungsgrad sind eher bescheiden; werden sie überlastet, bleiben sie einfach stehen.
Drehstrommotoren
Mit den vielen Drehstrommotor-Bauarten kommt der geneigte Bastler eigentlich nur in Form der Drehstrom-Asynchronmaschine mit Kurzschlussläufer in Berührung – das ist zum Beispiel wie der klassische Baukreissägen-Motor der Antrieb größerer stationärer Maschinen. Als bürstenloser Motor arbeitet er geräusch- und verschleißarm, ist aber deutlich voluminöser und schwerer als der Universalmotor.
Der Anker besteht aus einem Eisenkern mit eingepressten Aluminiumstäben. Das Feld des Stator-Magneten induziert nun in den Aluminiumstäben eine Spannung; da diese in sich kurzgeschlossene Windungen darstellen, fließt ein hoher Strom, der ein Magnetfeld im Anker-Eisenkern hervorruft – das wiederum dem Drehfeld im Stator zu folgen versucht. Anker dieser Art bezeichnet man auch als Käfigläufer.
Im Heimwerker-Bereich gibt es praktisch nur zwei- und vierpolige Drehstrommotoren – „zweipolig“ bedeutet hier, das zu jedem Drehstrom-Strang zwei Wicklungen gehören, bei „vierpoligen“ insgesamt 4 × 3 = 12. Zweipolige Maschinen haben eine Leerlaufdrehzahl von 3000 U/min, vierpolige 1500 U/min. Der Anker kann unter Last dem Drehfeld nacheilen, dies nennt man „Schlupf“ – er liegt je nach Motorengröße bei 2 bis 10 Prozent.
Arbeitspferde
Die drei Wicklungsstränge können dreieck- oder sternförmig miteinander verbunden werden; bei kleineren Motoren ist eher die Sternschaltung üblich, jeder Wicklungsstrang ist hier für 230 V ausgelegt. Durch die Phasenverschiebung ergibt sich eine Leiterspannung von:

Der Mittel punkt des Sterns ist nicht mit dem Netz verbunden.

Die Drehzahl lässt sich nur unzureichend über die angelegte Spannung steuern – sie ist in erster Näherung von der Netzfrequenz und damit der Umlaufgeschwindigkeit des Drehstroms abhängig. Um einen Drehstrommotor stufenlos zu steuern, benötigt man einen Frequenzumrichter, der über eine Halbleiterschaltung einen frequenz- und spannungsvariablen Drehstrom erzeugt. Ein solches Gerät (ca. 150 Euro in der Leistungsklasse um 1 kW) erlaubt je nach Ausführung auch den Betrieb am normalen Lichtnetz – also ohne Drehstrom-Steckdose. Die robusten Motoren vertragen durchaus auch Drehzahlen oberhalb ihrer 50-Hz-Nenndrehzahl, eine maximale Ausgangsfrequenz von 400 Hz oder noch mehr ist bei den meisten Umrichtern deshalb Standard.
Wir haben wegen der erheblichen Vorteile inzwischen einige Kondensatormotoren bei unseren Werkstattmaschinen durch Drehstromausführungen mit Umrichter ersetzt – erleichtert übrigens durch die DIN-Maße bei Standardmotoren. Die abgebildete Standbohrmaschine lässt sich nun stufenlos von 200 bis 2500 U/min steuern – ohne lästiges Umlegen des Treibriemens. Zusätzlich haben wir nun den Luxus der Vorwärts-Rückwarts-Umschaltung, zum Beispiel für das Gewindeschneiden.
Bei der Verwendung von Frequenzumrichtern für 230 V sollte man den Motor übrigens von Stern- auf Dreieckschaltung umklemmen, sonst erreicht er wegen der geringeren Klemmenspannung nicht seine volle Leistung.
Kondensatormotoren

Der Kondensatormotor ähnelt dem gerade besprochenen Drehstrommotor mit Kurzschlußläufer – allerdings verwendet er normalen Haushaltsstrom und erzeugt sich die für ein Drehfeld fehlende Phase über einen Betriebskondensator selbst. Im Unterschied zum Drehstrommotor (120° Phasenverschiebung) arbeitet er mit 90° Phasenwinkel, er benötigt deshalb nur zwei Wicklungen. Eine der beiden Statorwicklungen wird direkt aus dem Wechselstromnetz versorgt, während der zweiten Wicklung ein Kondensator in Reihe geschaltet wird (Faustregel: 20 µF pro kW Motorleistung).
Kondensatormotoren erreichen bei gleicher Größe nur etwa 65 Prozent der Leistung von Drehstrom-Asynchronmotoren. Für den variablen Betrieb über Frequenzumrichter eignen sie sich weniger, da der Kondensator nur für eine Frequenz (und genaugenommen nur für den Belastungsfall Nennleistung) ausgelegt ist. Als wartungsarmen Antrieb verwendet man die anspruchslosen Motoren gern bei kleineren Maschinen, Rasenmähern und Pumpen.

Übrigens kann man mit einem Kondensator auch normale Drehstrommotoren am einphasigen Lichtnetz zum Laufen bekommen: Man verbindet zwei der drei Anschlüsse mit den Leitern L und N des Lichtnetzes und den dritten über einen Kondensator mit einem der beiden Pole (Steinmetz-Schaltung). Der Kondensator ist hier allerdings mit gut 70 µF pro Kilowatt zu bemessen, in Frage kommen wie beim Kondensatormotor nur Folien- oder Metallpapier-Kondensatoren (MP) mit ausreichender Spannungsfestigkeit (450 V AC).
Spaltpolmotoren
Die pflegeleichten Spaltpolmotoren fand man früher in jedem Tonbandgerät und jedem Plattenspieler, auch heute werden sie zum Beispiel in 230-V-Lüftern noch gern verwendet. Durch den geräuscharmen Antrieb ohne schleifende Bürsten eignet sich der Spaltpolmotor auch für den Dauereinsatz.
Der Spaltpolmotor ist eigentlich eine Art Drehstrom-Asynchronmotor, auch wenn man ihm die Verwandtschaft zu den dicken Industriemotoren kaum ansieht. Wie seine großen Brüder arbeitet er mit einem Kurzschlussläufer, bei dem das eigene Magnetfeld durch Induktion entsteht.
Statt einer dritten Phase oder einer Kondensator-Schaltung wird die nötige Phasenverschiebung hier durch Kurzschlusswindungen erzeugt, die einen Teil des Magnetjochs umfassen. Ist der Werkstoff des Ankerkerns magnetisch „hart“ (behält also nach der Magnetisierung eine Zeit lang seinen Magnetismus), läuft der Motor zwar als Asynchronmotor an, aber als Synchronmotor mit hoher Drehzahlkonstanz weiter – wichtig für den Einsatz in Plattenspielern.

Die Drehzahl eines Spaltpolmotors ist weitgehend unabhängig von Betriebsspannungsschwankungen und fast nur von der Netzfrequenz abhängig. Ohne Frequenzumrichter lässt sich die Drehzahl also nicht steuern.
Schrittmotoren
Schrittmotoren sind für nicht allzu anspruchsvolle Positionieraufgaben das Mittel der Wahl: Sie können in einer vorgegebenen Position verharren und auf Befehl eine bestimmte Anzahl von Umdrehungen (auch teilweise) präzise ausführen – genau das braucht man für 3D-Drucker und CNC-Maschinen.
Der Schrittmotor ist eine Art Synchronmotor mit zwei Wicklungen, „gezahnten“ Feldmagneten und einem Anker aus Weicheisen. Ein Strom durch eine der Wicklungen sorgt dafür, dass der Anker in einer bestimmten Stellung „einrastet“: Vom gezahnten Stator wird der jeweils nächstliegende Zahn des Rotors angezogen, so dass der magnetische Kreis auf möglichst kurzem Weg geschlossen wird. Damit eine Drehbewegung entsteht, müssen die Ströme in den Wicklungen eine Phasenverschiebung von 90° aufweisen; die Drehrichtung ändert man, indem man die eine Phase nicht nach-, sondern voreilen lässt.

Die heute in jedem 3D-Drucker vorhandenen Schrittmotoren sind durchweg so genannte Hybrid-Schrittmotoren, bei denen der Anker über Dauermagnete vormagnetisiert ist; man spürt auch im stromlosen Zustand beim Drehen der Achse von Hand ein gewisses Halte- oder Rastmoment. Die Bauart ermöglicht eine feine Rastung (in der Regel 200 Schritte entsprechend 1,8° pro Umdrehung). Ältere und sehr billige Motoren mit Dauermagnet-Anker weisen eine deutlich gröbere Rastung (z .B. 7,5°) auf.
Schrittmotoren benötigen wie BLDCs eine Ansteuerschaltung, um sie sinnvoll betreiben zu können. Die sorgt für die zeitrichtige Abfolge der Strangströme. Früher hat man die Spulenwicklungen einfach an die Betriebsspannung gehängt; um die Ansteuerung zu vereinfachen, wurde zudem eine Mittelanzapfung herausgeführt, der Motor hatte also 6 Anschlüsse. So kam man mit zwei simplen Schalttransistoren pro Wicklung aus, die zur Magnetfeldumkehr den Strom mal in die eine, mal in die andere Wicklungshälfte schickten.
Nur einfachste Schrittmotorantriebe arbeiten heute noch so; diese Art der Ansteuerung erreicht weder besonders hohe Geschwindigkeiten noch einen ruhigen Motorlauf. Eine deutliche Verbesserung ergibt sich, wenn man einen Vollschritt in mehrere Teilschritte aufteilt – indem man den Strom der beiden Wicklungen halt nicht „digital“ nur ein- und ausschaltet, sondern mehrere Zwischenwerte zulässt. Üblich sind 2, 4, 8 oder 16 Teilschritte. Ein Motor mit 200 Vollschritten pro Umdrehung benötigt für den gleichen Weg also 3200 16tel-Schritte.
Zur Ansteuerung verwendet man heute durchweg integrierte Lösungen – angesichts der günstigen Angebote der fernöstlichen Chipschmieden wird niemand mehr auf die Idee kommen, eine Schrittmotor-Endstufe diskret aufzubauen. Aktuelle Ansteuer-Chips interpolieren aus 4 bis 16 Teilschritten bis zu 256 Mikroschritte, wobei der Strom durch die Wicklung durch aufwendige Tabellenberechnungen einen sinusförmigen Verlauf annimmt. Die Anzahl der gewünschten Teilschritte pro Umdrehung kann man an der Schrittmotor-Endstufe meist mit Drahtbrücken, Jumpern oder DIP-Schaltern einstellen.
Von der Ansteuerung mit konstanter Spannung ist man ebenfalls abgerückt. Wer den Artikel über Spulen in der letzten Make-Ausgabe 3/16 verfolgt hat, weiß warum: Der Strom durch eine Spule (in diesem Fall die Motorwicklung) steigt bei angelegter konstanter Spannung nur endlich schnell an. Schon bei einigen hundert Impulsen pro Sekunde wird der für ein bestimmtes Drehmoment erforderliche Strom nicht mehr erreicht – und der Strom ist es ja schließlich, der für die magnetischen Kräfte im Innern des Motors verantwortlich ist.
Eine hochohmige Wicklung mit vielen Windungen und entsprechend hoher Induktivität lässt sich mit normalen Mitteln also nicht mehr schnell genug ein- und ausschalten. Moderne Schrittmotoren haben deshalb eher niederohmige Wicklungen im unteren einstelligen Ohm-Bereich und niedrige Induktivitätswerte. Die manchmal noch aufgedruckte Betriebsspannung ist praktisch ohne Belang; sie gibt praktisch nur an, welche Spannung an der Wicklung bei Nennstrom zustande kommt.
Neuere Motoren haben nur noch zwei (bipolar betriebene) niederohmige Wicklungen ohne Mittelanzapfung, als A und B bezeichnet. Wicklung A und B dürfen ohne weiteres miteinander vertauscht werden, eine falsche Drehrichtung lässt sich durch Umpolen einer (!) der beiden Wicklungen beheben. Die zu einer Wicklung gehörenden Anschlüsse lassen sich leicht mit einem Ohmmeter ermitteln, denn untereinander haben die Wicklungen keine Verbindung.

Passende (meist integrierte) Schrittmotor-Endstufen arbeiten durchweg mit geschalteten Strömen statt mit geschalteten Spannungen. Die Stromregelung erfolgt über einen eingebauten Messwiderstand; sobald der gewünschte Motorstrom erreicht ist, wird die Zufuhr gekappt. Das An- und Abschalten erfolgt wie bei einem Schaltnetzteil verlustarm mehrere tausendmal pro Sekunde. Ein Motor mit einer „Nennspannung“ von 3 V kann deshalb auch an einer 24-V-Endstufe nicht durchbrennen, solange der zulässige Motorstrom (meist ebenfalls an der Endstufe einzustellen) nicht überschritten wird.
Die Stromregelung, die ja zudem den eingestellten Teilschritten folgen muss, ist ein ziemlich komplexer Regelvorgang, ebenso die Interpolation der Zwischenschritte. Führend auf diesem Gebiet ist übrigens die Hamburger Firma Trinamic – dort optimiert man inzwischen auch die Geräuschentwicklung und den Energieverbrauch von Schrittmotoren.
Beim Gebrauchtkauf aufpassen: Es gibt auch fünfpolige Schrittmotoren (etwa die sehr hochwertigen des Hersteller Berger Lahr). Diese laufen extrem ruhig, benötigen aber zwingend die passende Ansteuerschaltung des jeweiligen Herstellers. Meiden sollte man aus oben genannten Gründen auch Motoren mit hohen Wicklungswiderständen – dies sind meist ältere Modelle.
Schrittmotoren auf Speed
Schrittmotoren erreichen unter Last nur dann hohe Geschwindigkeiten, wenn der Strom durch ihre Wicklungen schnell genug ansteigen kann. Das klappt ausschließlich mit niederohmigen Motorwicklungen und hohen Betriebsspannungen! Wenn der Motor schnellen Bewegungen nicht folgen kann, nützt es überhaupt nichts, den Strom an der Schrittmotor-Endstufe höherzustellen – das führt nur zu unnötiger Erwärmung und stärkerer Geräuschentwicklung im unteren Geschwindigkeitsbereich.
Bei unserer China-Steuerung ermöglichte schon der Sprung von 24 V auf 36 V Betriebsspannung erheblich höhere Geschwindigkeiten – so stieg stieg die Verfahrgeschwindigkeit unserer CNC-Fräse mit einfachen Trapezspindeln von 1800 auf 2800 mm/min. Mit dem Austausch der Endstufen gegen spannungsfestere konnten wir dann sogar 4500 mm/min Verfahrgeschwindigkeit bei 48 V Betriebsspannung realisieren – und das sogar bei nun niedriger eingestelltem Motorstrom.
Servomotoren
Servomotoren sind die Königsklasse bei den Positionierantrieben – von hochspezialisierten (und deshalb hier außen vor bleibenden) Linearmotoren einmal abgesehen. Ein Servomotor ist ein ganz normaler Elektromotor (der Kompaktheit wegen meist als DC- oder BLDC-Motor ausgeführt), dem ein Drehwinkel-Encoder (auch Resolver genannt) und eine Regelschaltung beigefügt wird. Er kann den Schrittmotor in hochdynamischen, schnellen Antrieben vollständig ersetzen, eignet sich aber auch für eine Fülle anderer Aufgaben.
Ein Servomotor funktioniert im Prinzip genau wie die kleinen Modellbauservos: Ein Sollwert (Breite des Fernsteuerimpulses) wird ständig mit einem Istwert (Position des Ruderhorns) verglichen. Bei Abweichungen von Soll- und Istwert wird der Motor so lange in die eine oder andere Richtung laufen gelassen, bis beide Werte möglichst gut übereinstimmen – eine klassische Regelschleife.

Beim Servomotor stellt die gewünschte Maschinenposition den Sollwert dar, der Wert vom Drehwinkel-Encoder den Istwert. Stimmen beide Werte überein, ist der Zielpunkt erreicht, ansonsten muss der Motor ein Drehmoment in die der Abweichung entgegengesetzten Richtung ausüben.
Nun wird es kompliziert: Einerseits soll der Motor die gewünschte Stellung möglichst rasch anfahren, andererseits aber nicht übers Ziel hinausschießen, um sich hinterher korrigieren zu müssen – oder gar zu Schwingungen auflaufen. Ständig ist nebenbei das Drehmoment und der Motorstrom zu kontrollieren, damit weder Mechanik noch Motorelektronik Schaden nehmen.
Im Grunde genommen werkeln hier drei ineinander verschachtelte Regelkreise: Einer, der den Motorstrom und das Drehmoment nachregelt, dann ein zweiter, die für die Geschwindigkeit zuständig ist, und drumherum die eigentliche Positionsregelung. Die Technik, die dahinter steckt, ist im Detail noch viel komplizierter – mit der Theorie über PID-Regler hätten wir diese 12 Seiten komplett füllen können. Zum Glück muss man sich darum nur ansatzweise kümmern, denn das erledigt der zum Motor passende Servoregler (auch als Servoverstärker bezeichnet).
Klassische Servoverstärker arbeiten entweder mit analogen Eingangswerten (d. h. Spannungen im Bereich von 0 bis 10 V) für Position, Drehzahl und Drehmoment, oder aber wie eine Schrittmotor-Steuerung mit Schrittimpulsen und einem Richtungs-Signal. Moderne Servoantriebe können darüber hinaus über TCP/IP oder Feldbussen wie Profibus oder CAN angesteuert werden, fahren vorgegebene Bewegungsabläufe ab und können auf Zustände der Maschine autark reagieren – sie erreichen aber auch leicht den satt vierstelligen Euro-Bereich.
Viele der ebay-Angebote aus dem industriellen Umfeld kommen für den Heimanwender somit gar nicht in Frage – Feldbus-Systeme benötigen einen ziemlichen Overhead an Interfaces und passenden Kabeln. Das Industrie-Schnäppchen sollte also wenigstens ein Impuls-Richtungs-Interface haben, zudem ist eine vollständige Dokumentation unerlässlich.
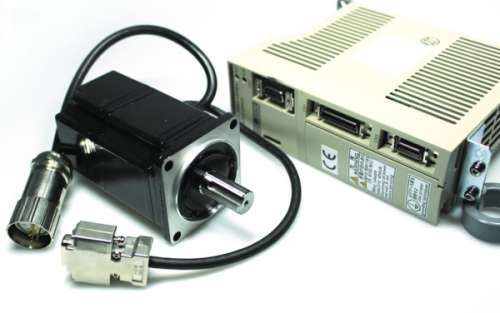
Gebrauchte Industrie-Servoverstärker bekommt man in Online-Auktionen ab 100 Euro, für einen passenden Motor muss man 50 bis 150 Euro anlegen. Wichtig: Die Regelungscharakteristik ist in jedem Fall auf die Maschine anzupassen, weil die inerten Massen des Antriebsstrangs und die Dämpfung/Reibung in die Regelkreise einbezogen werden müssen. Viele Servoverstärker haben deshalb eine RS-232- oder RS-422-Schnittstelle zur Parametrierung über ein Computerprogramm (meist, aber längst nicht immer kostenlos) des Herstellers.
Inzwischen gibt es halbwegs erschwingliche Servoantriebs-Sets als Neuware aus China, beispielsweise die Modelle ACS606 und ACS806 des Herstellers Leadshine – 200 Euro muss man aber auch dafür anlegen. Das ist im Vergleich zu einem gleich großen Schrittmotor mit Endstufe immer noch fünfmal so teuer.

„Gleich groß“ heißt hier aber nicht „gleich stark“: Servomotoren sind durch ihren BLDC-Antrieb deutlich leistungsfähiger. Auch wenn ihr Nenn-Drehmoment zunächst wenig auffällig ist: Im Unterschied zu Schrittmotoren, die schon bei Drehzahlen von 400 U/min drehmomentmäßig in den Keller fallen, können Servomotoren ihre angegebenen Newtonmeter auch noch bei 3000 U/min und mehr halten; außerdem kommen sie ohne ansteuerungsseitige Brems- und Beschleunigungsrampen aus und verpassen keine Schritte.
Wer einmal ein Servo-System live gesehen hat, wird sofort von der Leichtfüßigkeit und Dynamik dieser Antriebe fasziniert sein. Trotzdem: Ein solcher Antrieb dürfte sich nur für größere CNC-Maschinen rechnen. Wer das Abenteuer Servo meistert, wird mit einer seidenweich laufenden und unglaublich agilen Maschine belohnt. —cm