Stahlherstellung: CO2-arme Alternativen zum Koks
Bei der Stahlherstellung entstehen Unmengen an Kohlendioxid. Technisch ließe sich das ändern – aber der Aufwand dafür wäre immens.
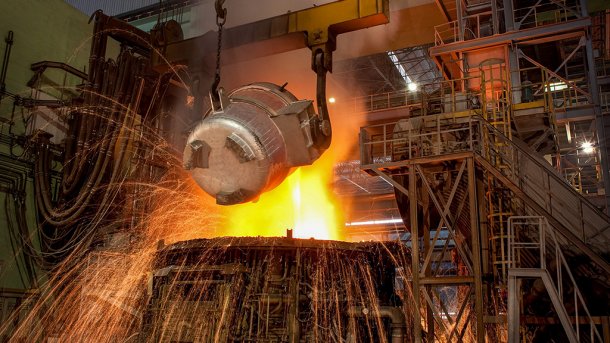
Elektrische Lichtbogenöfen wie dieser sind in der Stahlindustrie bereits weit verbreitet – vor allem zum Einschmelzen von Stahlschrott. Wird das Koks im Hochofen durch Wasserstoff ersetzt, müssen sich auch andere Prozesse der Stahlherstellung ändern. Lichtbogenöfen spielen dabei eine zentrale Rolle.
(Bild: SMS group)
- Udo Flohr
Stahl ist für rund sieben Prozent der weltweiten CO2-Emissionen verantwortlich – mehr als der Lkw-Verkehr. Allein in Deutschland verursachen die Stahlwerke rund halb so viele Emissionen wie die gesamte Pkw-Flotte. Und bis 2050 soll der weltweite Bedarf noch um mindestens ein Drittel steigen. Um die dabei entstehenden Emissionen zu senken, müssen die Stahlhersteller tief in die Trickkiste greifen, denn die Treibhausgase entstehen auf mehreren Wegen: Zum einen durch die Produktion der nötigen Hitze, zum anderen chemisch – ähnlich wie beim Zement.
Stahl wird im Prinzip immer noch hergestellt wie vor 3.000 Jahren: unter extensivem Einsatz von Kohle. Sie dient gleichzeitig als Energielieferant und als chemischer Reaktionspartner, der dem Eisenoxid im Erz den Sauerstoff entzieht (Reduktion). Im ersten Schritt erhitzt man die Kohle dazu unter Sauerstoffabschluss und wandelt sie so in Koks um. Das entfernt Verunreinigungen und erhöht den Kohlenstoffgehalt. Der Koks kommt zusammen mit Eisenerz in einen Hochofen und verbrennt bei rund 1.600 Grad, zusätzlich wird durch seitliche Düsen Kohlenstaub eingeblasen. Dabei entsteht unter anderem Kohlenmonoxid (CO), das sich mit dem Sauerstoff des Eisenoxids zu Kohlendioxid verbindet. Ein Teil des Kohlenmonoxids, etwa 22 Prozent, entweicht aus dem Hochofen, zusammen mit 22 Prozent Kohlendioxid und 52 Prozent Stickstoff. Diese Mischung nennt sich "Gichtgas". Es wird in der Regel aufgefangen und anschließend zur Energieerzeugung verbrannt.
Führt man das Gichtgas allerdings zurück in den Hochofen, statt es zu verbrennen, kann das Kohlenmonoxid weiteres Eisenerz reduzieren. Dies könnte den Kohlenstoffbedarf eines Hochofens um etwa 24 Prozent senken. Mit einem solchen Verfahren experimentierte etwa ArcelorMittal in Eisenhüttenstadt. Eine Studie der niederländischen Technologieberatung TNO erwartet die Marktreife bis 2030.