Auf dem Weg zum individuellen Massenschuh
3D-Druck verspricht die Individualisierung von Massenprodukten. Zusammen mit einem Start-up geht Adidas jetzt einen ersten bedeutenden Schritt auf dem Weg zu diesem Ziel.
- Katherine Bourzac
Anhänger des 3D-Drucks schwärmen seit langem von der Möglichkeit, die Technologie für individualisierte Konsumprodukte zu nutzen. Mit am häufigsten erwähnt werden dabei Sportschuhe mit Sohlen, die auf die Biometrie des jeweiligen Trägers abgestimmt sind.
Vergangene Woche verkündete das 3D-Druckunternehmen Carbon aus Kalifornien, genau das realisiert zu haben. Zusammen mit Adidas hat es Materialien und Designs für die Zwischensohlen von Sportschuhen, also ihren elastischen, stoßdämpfenden Teil, entwickelt. Adidas will die FutureCraft 4D-Schuhe mit von Carbon produzierten Zwischensohlen zum Kauf anbieten. Zunächst sollen nur 400 Paare zu Promotion-Zwecken zu einem nicht genannten Preis angeboten werden, später in diesem Jahr sollen dann 5000 Paare in den Geschäften erhältlich sein.
Lesen Sie zum Thema "3D-Druck" auch:
Maßgeschneiderte Schuhe aus dem 3D-Drucker
Die erste Auflage wird noch nicht individualisiert sein, doch das ist ebenfalls angekündigt: Bald sollen Drucker von Carbon an mehreren Produktionszentren zum Einsatz kommen und maßgeschneiderte Schuhe für Kunden vor Ort fertigen. In seiner Heimatstadt Herzogenaurach hat Adidas bereits 2015 eine Pilot-“Speedfactory“ eröffnet, eine weitere soll dieses Jahr in Atlanta folgen.
Carbon wurde, ursprünglich unter dem Namen Carbon 3D, im Jahr 2013 von dem Chemieingenieur Joseph DeSimone mitgegründet, um seine Forschungsergebnisse zu Materialien und Prozessen für schnelleren 3D-Druck mit Hochleistungspolymeren zu kommerzialisieren. DeSimone, im Jahr 2008 mit dem Lemelson-MIT-Preis ausgezeichnet, hat sich mit Materialien für Stents, Nanomedizin und viele andere Anwendungen beschäftigt. Derzeit ist er an der University of North Carolina beurlaubt, um sich als CEO um das Unternehmen zu kümmern.
3D-Druck für federnden Schritt
Die erste Serie der Schuhe wird noch zentral gefertigt und nicht individualisiert sein. Trotzdem profitiert Adidas laut DeSimone dabei bereits von dem 3D-Druck, weil der eine stoßdämpfende, mehrschichtige Struktur ermöglicht, die mit Spritzguss nicht zu realisieren wäre. Außerdem können die Eigenschaften der Zwischensohle bei dem 3D-Verfahren unterschiedlich gestaltet werden, etwa mit mehr Stabilität an der Ferse.
3D-Druck für den individuellen Schuh (5 Bilder)
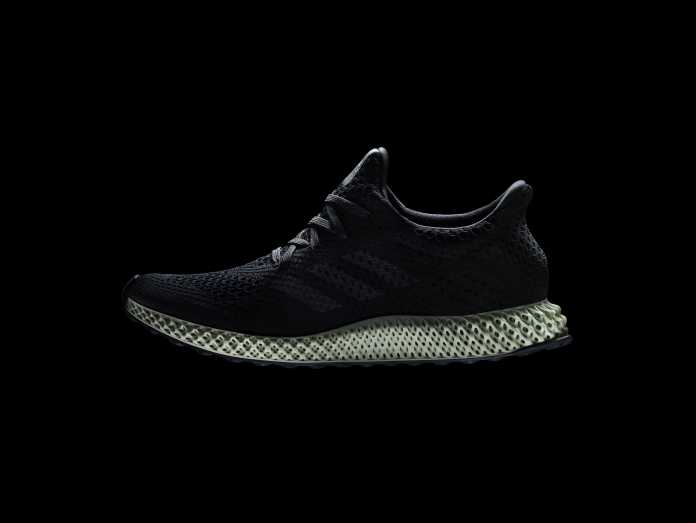
(Bild: Adidas)
Die Zwischensohle hat eine Honigwaben-Struktur. "Maschinenbauer ärgern die Welt seit Jahren mit den Eigenschaften dieser Struktur", sagt DeSimone. "Man kann so etwas mit Spritzguss nicht machen, weil jede Strebe ein individuelles Stück ist."
Revolution für die Schuh-Produktion?
Julia Greer, die sich als Materialwissenschaftlerin und Maschinenbauerin am California Institute of Technology mit den Auswirkungen von Mikro- und Nano-Strukturen auf die Eigenschaften von Materialien beschäftigt, bezeichnet Honigwaben-Strukturen als viel versprechend für Stoßdämpfung und Haltbarkeit. Wenn eine solche Struktur belastet wird, verformt sie sich nur in die Richtung der Belastung, erklärt Greer. Wenn die Ferse also auf die Zwischensohle drückt, komprimiert sie sich zum Boden und nimmt die Belastung auf, beult sich aber nicht zur Seite aus, was eine Abnutzung des Schuhs bedeuten würde.
Derzeit dauert der Druck einer einzelnen Zwischensohle noch 90 Minuten. Zusammen mit Adidas entwickelt Carbon aber Maschinen, mit denen er in 20 Minuten erledigt sein soll. Die 3D-Drucker von Carbon nutzen Muster von Laserlicht, um kontinuierlich aus einem flüssigen Bad von Polymer-"Tinte" zu drucken. Möglich ist dieser schnellere Prozess, weil unten im Tintenbad eine Sauerstoff-Barriere vorhanden ist, die verhindert, dass erstarrtes Polymer festklebt.
3D-Druck gegen mechanische Schwächen
Kontinuierliches Drucken bedeutet zudem, dass die Teile einheitlicher sind als bei anderen Technologien, die jede Schicht einzeln drucken. Der schichtweise Ansatz kann zudem mechanische Schwächen an den Verbindungen zwischen den Schichten bedeuten – bei dem Carbon-Prozess ist das nicht der Fall. Zudem hat sich das Unternehmen mit Polymer-Chemie beschäftigt und für die Zusammenarbeit mit Adidas ein spezielles druckbares Elastomer mit den richtigen mechanischen Eigenschaften und Farben für den Schuh entwickelt.
Adidas-Designer haben vor Ort bei Carbon in ungefähr 50 Iterationen das endgültige Design erarbeitet. Normalerweise haben die Designer nur 5 Anläufe dafür, weil jede Version aufwendig mit Werkzeugen hergestellt werden muss, bevor sie wieder in der Hand der Designer landet, und das kann Wochen dauern. Laut DeSimone bedeutet die Möglichkeit, Produkte dort zu entwerfen und zu testen, wo sie hergestellt werden, "das Ende der Prototypen".
(sma)