Wie 3D-Drucker besser werden können
Der 3D-Druck eignet sich traditionell eher für kleine Stückzahlen und "dumme" Bauteile. Neue Ansätze zeigen, wie sich beides ändern lässt.
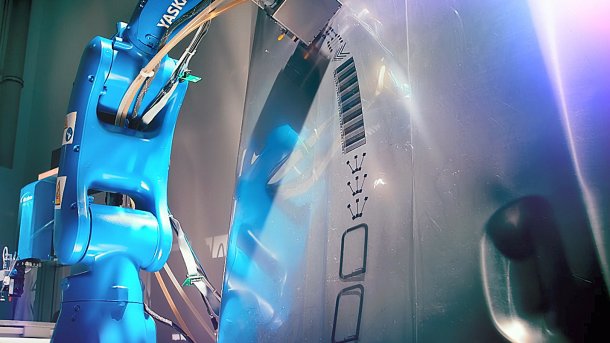
Ein Roboterarm druckt Leiterbahnen auf eine 3D-Oberfläche.
(Bild: Biermann&Jung)
Wäre es nicht praktisch, aus einem 3D-Drucker nicht nur einzelne Plastikteile zu ziehen, sondern fertige Schalter, Sensoren oder Lampen – ganz ohne zu löten, schrauben oder kleben? Solche Ansätze gibt es schon länger. Doch die wenigsten sind bisher über das Laborstadium hinausgekommen, berichtet Technology Review in seiner Januar-Ausgabe (ab Donnerstag am Kiosk oder online zu bestellen).
Das israelische Unternehmen Nano Dimension hingegen bietet unter dem Markennamen DragonFly bereits seit Jahren professionelle 3D-Drucker an, die Leiterbahnen und Gehäuse in einem einzigen Durchgang herstellen. Ein Druckkopf trägt schichtweise leitfähige Tinte mit Silber-Nanopartikeln auf, ein anderer bettet diese in Lagen aus isolierendem Kunststoff ein. Für den Sensorhersteller Hensoldt hat Nano Dimension beispielsweise eine zehnlagige, extrem dicht gepackte Leiterplatte hergestellt. Und gemeinsam mit dem Automobilzulieferer Rehau hat es einen beleuchteten Touch-Sensor entwickelt, der sich in beliebiger Form ausdrucken lässt. Andere Anwendungen sind etwa Antennen oder Kondensatoren.
„Das Druckverfahren ermöglicht ein unfassbares Spektrum neuer Modellierungstechnologien und enorme Flexibilität“, beschreibt Rehau die Vorteile. „Außerdem kann das Gehäuse direkt im Druckprozess hergestellt werden.“
Seine Maschinen bewirbt Nano Dimension in erster Linie für das schnelle Erstellen von Prototypen: Wenn Entwicklerteams neue Designs vor Ort ausdrucken und testen, können sie zügiger und diskreter arbeiten. „Top-Ziel“ sei für Rehau aber auch der Druck von Kleinserien. „Nur bei diesem Einsatz ist das Verfahren konkurrenzfähig“, teilt Rehau mit. Bei größeren Stückzahlen sind herkömmliche Methoden kostengünstiger.
Der Forschungsverbund Go Beyond 4.0 will individualisierte Produkte gleich so effizient herstellen wie Massenware. Das Projekt von sechs Fraunhofer-Instituten lief von 2016 bis 2020. Ergebnis sind mehrere Demonstratoren, darunter Autotüren mit individueller Verkabelung. Zunächst brennt ein Laser dazu Rillen ins Blech, in denen später die Leiterbahnen verlaufen.
Anschließend druckt ein Druckkopf, der an einem Roboterarm befestigt ist, isolierende Tinte in diesen Kanal, die ein weiterer Laser aushärtet. Als Nächstes folgt leitfähige Tinte und abschließend wieder eine Isolierschicht. So lassen sich nicht nur Leiterbahnen auf beliebig geformte Unterlagen drucken, sondern auch Schalter, Leuchten und andere Bauteile. Durch die vielen möglichen Ausstattungsvarianten sind die meisten Autos längst Einzelstücke, entsprechend aufwendig ist die Verkabelung mit klassischen Kabelbäumen. Dies wird durch das Druckverfahren nun überflüssig.
Mit dem Demonstrator Smart Wing druckten die Fraunhofer-Forscher Heizschlangen aus Silberpaste direkt auf trockenes Carbonfasergelege. Damit ließ sich eine zwei Millimeter dicke, minus 15 Grad kalte Eisschicht in sechs Minuten abschmelzen.
Ein weiterer Demonstrator sind LEDs mit beliebig gestaltbaren Linsen – sogenannte Freiformoptiken. In eine Stoßstange eingebaut, können sie etwa Warnsymbole auf die Straße projizieren. Zur Herstellung kombinierten die Forscher 3D-Druck mit fertigen Elektronikkomponenten aus dem Regal. Während des Drucks von Leiterbahnen und Linse halten die Druckköpfe inne, und ein Pick-and-Place-Roboter aus der Halbleiterindustrie platziert eine staubkorngroße LED an der richtigen Stelle. Laserscanner am Roboter und Markierungen am Bauteil sorgen dafür, dass alles exakt zusammenpasst.
„Unser Know-how sind die Prozessparameter“, sagt Ralf Zichner vom Fraunhofer-Institut für Elektronische Nanosysteme in Chemnitz. Oberflächen und Druckbahnen müssen beispielsweise entsprechend vor- und nachbehandelt werden, sodass die Tinte nicht zu stark verläuft. Auch beim Material war viel Feintuning nötig, so Sönke Steenhusen vom Fraunhofer-Institut für Silicatforschung in Würzburg. Für die Freiformoptiken entwickelten die Forscher einen druckbaren Ormocer-Kunststoff mit einem hohen anorganischen Anteil. Er hat ähnliche Eigenschaften wie Glas, ist hochtransparent und vergilbt nicht. Ein noch ungelöstes Problem ist die Wärmeentwicklung, weshalb die LEDs bisher nur als Anzeigen dienen, nicht aber als Scheinwerfer.
„Ein wichtiger Aspekt unserer Verfahren ist: Sie lassen sich direkt in konventionelle Produktionstechniken integrieren“, sagt Falk Kemper vom Fraunhofer-Institut für Angewandte Optik und Feinmechanik in Jena. Wie viel der Prozess genau gegenüber herkömmlichen Herstellungsverfahren einsparen würde, ist allerdings schwer zu sagen – Hersteller rücken ihre Zahlen ungern heraus. Sein Kollege Zichner ergänzt: „Wir haben wegen Corona zwar noch keine Kunden, konnten aber schon Partner begeistern.“
(bsc)