Recycling: Auf dem Weg zum Öko-Akku
Eine niedersächsische Firma hat die Wiederverwertung von ausgedienten Akkus optimiert.
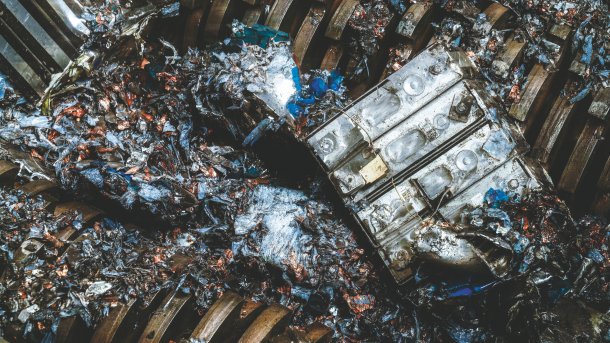
(Bild: Wolfram Schroll / Duesenfeld)
- Denis Dilba
Rund zwei Meter hoch ist die stählerne Konstruktion, auf die Christian Hanisch beim Rundgang durch die Industriehalle zeigt. Unzählige massive Schrauben verbinden zentimeterdicke graue Metallplatten. "Damit alles dicht bleibt. Das ist unser Inertgas-Schredder", sagt der Geschäftsführer der Duesenfeld GmbH, die auf umweltfreundliches Recycling von Lithium-Ionen-Batterien spezialisiert ist. Direkt daneben stehen eine große Vakuumpumpe und ein brusthoher silberner Tank. "Der ist für den wiedergewonnenen Elektrolyten", fährt Hanisch fort. Wenige Meter weiter steht eine knapp vier Meter hohe Säule, in deren Fuß ein Gebläse montiert ist. "Damit trennen wir nach dem Zerkleinern der Batterien die Separatorfolie ab – sie ist leicht, fliegt im Luftstrom nach oben und wird dort abgesaugt. Schwerere Metallfolien fallen einfach nach unten durch."
Normalerweise steckt die Technik in drei Standard-40-Fuß-Containern – zwei davon übereinander stehend, um die Trennsäulen unterzubringen. So kann sie einfacher dahin kommen, wo viele Akkus zu recyceln sind, etwa bei Sammelstellen. Das spart Zeit und Geld, denn Lithium-Akkus sind ein Gefahrgut. Transport und Lagerung machen den Löwenanteil der Wiederverwertungskosten aus.
Duesenfeld kommt laut Hanisch auf eine stoffliche Wiederverwertung von 96 Prozent. "Wir verbrauchen im Vergleich zu herkömmlichen Verfahren 70 Prozent weniger Energie und reduzieren den CO2-Fußabdruck der Batterie um 40 Prozent." Dies macht dem Unternehmen aus Wendeburg bei Braunschweig derzeit keiner nach. Das gängigste Recyclingverfahren des belgischen Marktführers Umicore schmilzt die Akkus bisher einfach im Hochofen ein. So können zwar Kobalt, Nickel und Mangan abgetrennt werden, der Rest aber landet als Schlacke in stillgelegten Bergstollen. Rund 7000 Tonnen Akkus verwertet Umicore nach eigenen Angaben pro Jahr. Der Prozess ist günstig, aber weder besonders energieeffizient noch umweltfreundlich. Die Recyclingquote liegt lediglich bei 25 Prozent.
Der Duesenfeld-Prozess hingegen kommt ganz ohne Hitze aus. Im ersten Schritt werden die Akkus tiefentladen. "Mit diesem Strom betreiben wir den Schredder", sagt Hanisch. Anschließend werden die Batterien mit Schraubenschlüsseln oder einer Flex auseinandergenommen. Aluminiumgehäuse, Kupferkabel und Plastikhalterungen landen sortenrein in Gitterboxen, die nackten Batteriezellen im Schredder. Dort sorgt eine Schutzgasatmosphäre für Sicherheit beim Zerkleinern.
Die Vorteile: Es entsteht kein ätzender Fluorwasserstoff, der aufwendig aus den Abgasen gefiltert werden muss. Zudem lässt sich der Elektrolyt wiederverwenden: Eine Vakuumpumpe reduziert den Druck so weit, dass die Flüssigkeit verdampft. Anschließend wird sie kondensiert und aufgefangen.
Nach dem Schreddern erhält Hanisch ein Granulat aus rund einem Zentimeter großen Partikeln unterschiedlicher Materialien. Sie können mit herkömmlichen Trennprozessen – Gebläse, Siebe oder Magnettrommeln – weiter sortiert werden. Übrig bleiben die Separatorfolie, Metalle sowie ein feines schwarzes Pulver. Darin stecken je nach Batterietyp verschieden große Anteile an Lithium, Graphit, Nickel, Mangan und Kobalt. Bisher verkauft Duesenfeld dieses Pulver an Firmen weiter, die daraus die Metalle extrahieren. Bald will die Firma die Stoffe selbst trennen, und zwar mit einem Schwefelsäurebad. Nur die Separatorfolie gelangt noch nicht in den Stoffkreislauf zurück.
Aktuell könne man 3000 Tonnen Lithium-Akkus pro Jahr verarbeiten, auch wenn dies in der Praxis noch nicht erreicht wird. In den kommenden Jahren will das Unternehmen 16 Schredder, sieben Trennanlagen im Container sowie eine zentrale hydrometallurgische Aufbereitung aufbauen.
Konkurrenzlos ist Duesenfeld aber nicht: Auch der Krefelder Recyclingspezialist Accurec hat zusammen mit Bernd Friedrich, Leiter des Instituts für Metallrecycling an der RWTH Aachen, ein Verfahren entwickelt, das die Recyclingquote an "das Optimum technischer und wirtschaftlicher Prozesse" heranbringt, so Friedrich. Hier wandelt ein thermischer Prozess das Lithium zu einer Verbindung um, die besonders einfach aus der schwarzen Masse herausgelöst werden kann.
"Beim Energieverbrauch erzielt das Verfahren ähnlich gute Werte wie die Duesenfeld-Methode", sagt Friedrich. Dafür habe das Accurec-Verfahren seine industrielle Tauglichkeit bereits bewiesen. "Es ist daher noch nicht entschieden, welches sich durchsetzen wird."
Die umweltfreundlichen Verfahren sind jedoch teuer. Ein wichtiger Grund ist die aufwendige Demontage per Hand. "Ein Traum wäre ein Robotersystem mit KI, das die verschiedenen Batterietypen per Kamera erkennt, deren Baupläne gespeichert hat und sie dann selbstständig und sicher zerlegt", sagt Friedrich.
Ein weiterer Grund sind die noch sehr geringen Mengen an Auto-Akkus. Daran wird sich auch so rasch nichts ändern, meint Dirk Uwe Sauer vom Institut für Antriebe der RWTH Aachen. Nennenswerte Mengen werden erst "weit im nächsten Jahrzehnt" in die Recyclingprozesse zurücklaufen. "Aktuell sind die Kosten für das Recycling von Lithium-Ionen-Batterien höher als die Erlöse durch die wiedergewonnenen Materialien", so Sauer. Zudem sinke der Anteil des teuren Kobalts in den Akkus laufend, wodurch das Recycling weniger lukrativ werde.
So ist es sehr wahrscheinlich, dass Hersteller und Kunden zumindest einen Teil der Recyclingkosten tragen müssen – etwa über ein Pfandsystem. Bei Starterbatterien aus Blei sorgt ein Pfand von 7,50 Euro bereits für einen Rücklauf von beinahe 100 Prozent und eine ebenso hohe Verwertungsquote. Um diesen Wert auch bei Lithium-Ionen-Akkus zu erreichen, müsste die EU allerdings ihre Recyclingregeln überdenken. Vorgeschrieben ist lediglich eine Recyclingquote von 50 Prozent. Die entsprechende Richtlinie stammt noch aus dem Jahr 2006. Damals liefen Lithium-Ionen-Batterien noch in der Kategorie "Sonstige". Das ist bis heute so geblieben.
(bsc)