Flymo-Umbau: ferngesteuert Rasenmähen mit Propellerantrieb
Rasenmäher schieben war gestern. Der Flymo fliegt dank Fernsteuerung durch den Garten. Dazu braucht er allerdings gleich zwei Propellerantriebe.
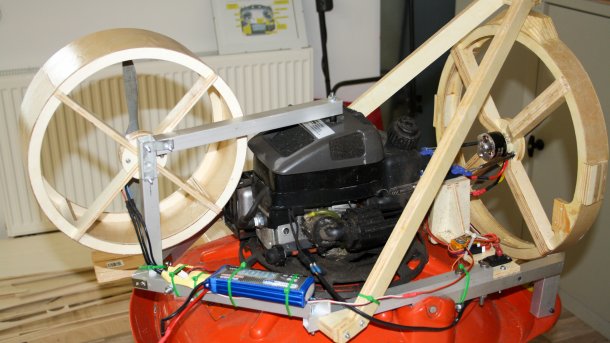
- Thomas Fischer
Ein Flymo ist ein spezieller Rasenmäher, der - ähnlich wie ein Hovercraft - auf einem Luftkissen über den Boden schwebt und für Rasenflächen entwickelt wurde, die sich mit normalen Rasenmähern schwer bis gar nicht mähen lassen. Der könnte doch auch ferngesteuert werden, meinte mein Schwiegersohn und kurze Zeit später stand ein gebrauchter Flymo, Typ HVT 40, in meiner Werkstatt.
Die nötigen Umbauten
Von Haus aus wird der Flymo wie jeder Rasenmäher über einen Handgriff gesteuert. Stattdessen soll der Flymo jetzt einen Antriebsmotor bekommen, wie auch das Futterboot, das ich in Make 2/16 vorgestellt habe. Weil bei einer Fernsteuerung niemand den Griff hält, kommt allerdings das Drehmoment des Mäh- und Antriebsmotors zum Tragen, das ein weiterer Motor ausgleichen muss. Er wird nach dem Hubschrauberprinzip quer zur Fahrtrichtung eingesetzt und lässt sich stufenlos auf die erforderliche Drehzahl zum konstanten Drehmomentausgleich einstellen – unabhängig vom Antriebsmotor. Nach dem Starten des Mähmotors wird er soweit hochgefahren, bis der Flymo ruhig stehenbleibt.
Hoverboard-Rasenmäher Flymo mit Umbauten (4 Bilder)

Als Antriebsmotor nutze ich einen 1,3-kW-Brushless-Motor (750 Watt dürften bereits ausreichen) mit einer 13×8-Zoll-Luftschraube, 80-Ampere-BEC-Regler und 5S-Lipo-Akku. Er wird von zwei Servos mit einer Zugkraft von je 15 kg gesteuert, die mit der Elektronik auf einem kleinen Anbau sitzen. Für den Drehmomentausgleich sorgen ein 500-W-Brushless-Motor, eine 10×7er Luftschraube, 50-Ampere-ESC-Regler und ein 3S-3600er Lipo. Ein Standardservo übernimmt die Ansteuerung des Notausschalters. Die Fernsteuerung hat einen Schaltkanal für den Notausschalter, einen Drehknopf für den Motor zum Ausgleich des Drehmoments sowie eine stufenlos regelbare Motordrossel für den Vortriebsmotors. Hier geht es zur Flymo-Einkaufsliste.
Da der Motor überdimensioniert ist, ist der Flymo in Fahrt kaum noch zu stoppen – hier kommen der geringe Luftwiderstand, wenig Widerstand beim Mähen und die Masseträgheit zusammen. Die Steuerung erfordert Übung: Mit dem Gas für Vortrieb muss man sehr behutsam umgehen.
Empfohlener redaktioneller Inhalt
Mit Ihrer Zustimmmung wird hier ein externes Video (Kaltura Inc.) geladen.
Ich bin damit einverstanden, dass mir externe Inhalte angezeigt werden. Damit können personenbezogene Daten an Drittplattformen (Kaltura Inc.) übermittelt werden. Mehr dazu in unserer Datenschutzerklärung.
Holzteile aus der Fräse
Die Vorlagen für alle Sperrholzteile können als DesignCAD- und dxf-Dateien hier heruntergeladen werden. Speziell bei den Bohrungen für die Motorbefestigungen ist auf die Passung zu den selbst verwendeten Motoren zu achten. In den Dateien "Sperrholzteile 8mm_1" und "Sperrholzteile 4mm" finden sich die Bauteile für den Bau des Antriebsringes, des Querbrettes und der Servohalterung zur Lenkung, nummeriert von 1 bis 5. Sofern die Bauteile mit einer Fräse geschnitten werden, ist in den mit Rechtecken markierten Bereichen der Ringe die Hälfte des Materials als Tasche abzutragen. Die Ringe sind auf der Vorlage aus Platzgründen geteilt.
Zunächst klebt kleben wir jeweils eine Kreuzhalterung (1) zwischen zwei Kreuzhalterungen (2) und danach diese Halterungen in den Mittelspant. Die Außenringe (unnummeriert) können mittels Klammern gleichzeitig angebracht werden. Auf der Innenseite des Ringes kleben wir den 4 mm dicken Spant auf den vorhandenen Spant. Dabei muss man auf Bündigkeit der Bohrungen achten und dazu während des Anpressens zwei Schrauben durch die Bohrungen der Motorhalterung schieben. Das Servobrett (3) klebt man winklig in die Aussparung an der schmaleren Seite der Spanten (4), daran anschließend von außen die Winkelstücke (5).
Ähnlich läuft der Aufbau des zweiten Rings ab (Dateien "Sperrholzteile 8mm_2" und "Sperrholzteile 6mm"), dessen Motor das Drehmoment ausgleicht. Die Spanten (2) mit ausgerichteten Bohrungen hinter Spant (1) kleben. Anschließend setzt man gleichzeitig die Kreuzhalterungen (3) mit den Ringen an die drei Spanten setzen, Spant (1) muss dabei auf der Innenseite des Ringes sitzen. Jeweils fünf der Teile (4) zu einem Paket bündeln, die für die Befestigung des ersten Rings gebraucht werden.
Aus der Datei "Sperrholzteile 8mm_3" kleben wir ebenfalls jeweils zwei Seitenteile. Dabei ist darauf zu achten, dass ein linkes und rechtes Seitenteil mit außenliegenden Bohrungen entsteht. Diese dienen nur als Orientierung für die Befestigung am Aluvierkant, damit die Löcher senkrecht in den Vierkant gebohrt werden können. Auch die Winkelverbinder (1) zwischen (2) kleben. Das Winkelverbinderpaket passt nach dem Trocknen in die dafür vorgesehenen Aussparungen zwischen den Seitenteilen.
Aus den Dreieckteilen klebt man jeweils zwei zu einem Paket, danach am unteren Ende der Seitenbefestigungsteile anbringen. Das 1-mm-Beplankungssperrholz wird so zugeschnitten, dass dessen Länge jeweils auf den Querstegen der Kreuzhalterungen zum Befestigen endet und von dort der nächste Abschnitt angesetzt werden kann. In der Mitte der Pakete aus den Teilen (4) setzen wird die Bohrung, in die anschließend das Messingrohr passend abgelängt eingeklebt wird.
Wenn die Beplankung des Antriebsringes fertig aufgebracht ist, kann an zwei gegenüberliegenden Stellen die Pakethalterungen ausgerichtet werden und der Messingring durchbohrt werden. Das Loch in der Beplankung anschließend etwas größer nachbohren, um das genaue Ausrichten der Pakete zu erleichtern. Die Pakete klebt man auf die Beplankung – damit sie richtig ausgerichtet sind zum Beispiel ein passendes Alurohr durch die beiden Bohrungen. Die Pakete sollten vorn und hinten am Ring bündig anliegen.
Um einen genügend großen Drehwinkel zu ermöglichen, das Paket oben beidseitig schrägen.
Schließlich alle Holzteile grundieren und, falls gewünscht, mit Farbe lackieren.
Zusammenbau
Als Nächstes ist der Handgriff des Flymo abzumontieren. Praktischerweise passen in die zwei Böcke, in denen der Griff befestigt war, Aluvierkanten von 20 × 20 mm. Auf dem Alugerüst werden alle weiteren Anbauten befestigt sodass auf dem Flymo nur drei Bohrungen nötig sind. Zwei Vierkantstücke werden auf 270 mm abgelängt und für die Verschraubung mit den Winkeln vorn um 45 Grad abgeschrägt.
Die zwei Aluwinkel vorn auf eine Höhe von 107 mm anpassen.
Zwei weitere Aluvierkantstücke werden auf 280 mm ablängt, sie werden später zur anderen Seite, nach hinten, angebracht. Die Aluvierkantleisten, die den Motor für den Drehmomentausgleich tragen, sind im 45-Grad-Winkel mit einer Länge von ebenfalls 280 mm und entsprechender Abschrägung zu sägen.
Der Standvierkant hat eine Höhe von 214 mm und ist oben leicht abgeschrägt, weil die Querstange (266 mm) vom Mähmotor entsprechend schräg liegt. Unten auf 20 mm Länge sollte nur eine Wand des Vierkants stehen bleiben, um eine stabile Auflage auf den tragenden Vierkantrohren zu ermöglichen.
Die Befestigungsbohrungen im Lagerbock des Flymo übertragen wir auf die nach hinten ragenden Vierkantrohre. Die Bohrungen für den hinteren Aluwinkel, den Stahlwinkel zum Flymogehäuse sowie in der Mitte auf dem Flymogehäuse ein 10-mm-Loch für die Schraube zur Aufnahme des Antriebsringes bohrt man mit einem 10er Bohrer.
Alle Bauteile am Flymo anschrauben und am Lagerbock zur Konterung eine M6-Stoppmutter verwenden.
Von der Hinterkante des Vierkantrohres sind bis zur Vorderkante des Servobrettes 93 mm abzumessen und das Brett beidseitig auf den Rohren auszurichten. Dann die Befestigunsbohrungen auf den Vierkant übertragen, die Servohalterungen für die Lenkservos mittig aufkleben und verschrauben und schließlich das Servobrett anschrauben.
Bei den nach vorn ragenden Vierkantrohren setzen wir zwei 8 mm Bohrungen im Abstand von 40 mm und übertragen diese auf die hinteren Vierkantrohre.
Diese Bauteile können nun alle miteinander verschraubt werden. Der Zusammenbau des vorderen Winkelträgers beginnt mit dem Anbringen des Frontwinkels. Die hintere Lasche sägte ich von einem größeren Stahlwinkel ab und bog sie passend zurecht.
Wenn diese drei Vierkantrohre verschraubt und die zwei Bohrungen vom Motorbefestigungsring des Drehmomentausgleichs im Standrohr übertragen sind, passt man die Halterung auf dem Flymo an und verschraubt sie.
Nun geht es an das Arbeiten an der Drehmaschine: Zuerst zwei M10-Schrauben auf 58 und 38 mm absägen. Auf einer Länge von 22 mm auf den Innendurchmesser des Messingrohres im Antriebsring abdrehen, sodass leichtes Bewegen ohne Schlackern möglich wird. Vor dem Zusammenbau sind diese Bolzen leicht zu fetten. Dann versehen wir 45-mm-Stahldraht (Außendurchmesser 10 mm) auf einer Seite mit einer 4,2-mm-Bohrung, die tief genug ist, um das Gewindestück zur oberen Motorabdeckung am Flymo komplett aufnehmen zu können und schneiden anschließend ein M5-Gewinde. Auf der gegenüberliegenden Seite 30 mm auf 6 mm abdrehen und ein M6-Gewinde aufschneiden.
Nun muss man die Motorabdeckung abnehmen und die Schraube auf einer großen Unterlegscheibe auf das Befestigungsgewinde schrauben. Die Bohrung ist auf die Querstange zu übertragen und verschrauben. Auf der Ringseite passen wir den Befestigungswinkel an und montieren alles fest mit dem Drehmomentring. Die kürzere M10-Schraube in das hintere mittlere Loch des Flymogehäuses mit einer großen Unterleg- und Sicherungsschraube anbringen, die längere in der oberen Halterung. Schließlich bringen wir alle Servos in ihren Halterungen an. Die Anlenkungshebel für die Lenkung sind, wie auf dem Foto zu sehen, zu verlängern.
Nun muss man den Antriebsring auf die untere Schraube stecken. Die Höhe der Anlenkungshebel ist auf den Mittenring zu übertragen und zwei Bohrungen zur Aufnahme der Anlenkungen zu setzen, bevor wir sie verschrauben.
Die obere Ringhalterung einstecken und am Vierkantrohr vorn mit Schraubzwingen befestigen. Dabei auf leichte Drehbarkeit des Ringes achten und die Bohrungen zum Vierkant hin rechtwinklig durchbohren. Sie werden mit genügend langen M4-Gewindestangen befestigt.
Die Verbindungen zwischen den Anlenkungshebeln der Lenkungssteuerungen stellen wir aus 6 mm Stahldraht her. Abschließend die Motoren mit den Reglern verbinden und diese wie die Servos mit dem Empfänger verbinden. Gegegebenenfalls sind die Anschlusskabel zu verlängern. In jedem Fall muss man die Laufrichtung überprüfen. An den neben dem Servo eingeschraubten Notausschalter löten wir zwei Kabel mit Kabelschuhen und verbinden sie mit der Buchse am Motor.
Am Servo einen möglichst langen Hebel aufsetzen und diesen in Längsrichtung zu einer Nut aufschneiden, in die der Schalthebel greift.
Auch hier noch einmal die korrekte Funktionsweise testen, dann kann es losgehen.
Empfohlener redaktioneller Inhalt
Mit Ihrer Zustimmmung wird hier ein externes Video (Kaltura Inc.) geladen.
Ich bin damit einverstanden, dass mir externe Inhalte angezeigt werden. Damit können personenbezogene Daten an Drittplattformen (Kaltura Inc.) übermittelt werden. Mehr dazu in unserer Datenschutzerklärung.
Anregungen für die Weiterentwicklung
Statt Motoren mit Propellern lassen sich auch Impeller verwenden; da sie bereits ummantelt sind, dürfte sich die Befestigung noch einfacher umsetzen lassen. Legt man für den Vortrieb zwei Impeller übereinander in gegenüberliegende Laufrichtungen, wäre sogar Rückwärtsfahren möglich. Impeller haben allerdings wegen der hohen Drehzahlen einen hohen Stromverbrauch sodass Akkus mit höheren Kapazitäten für längere Laufzeiten eingesetzt werden müssten. Auch der Einsatz als Rennfahrzeug ist möglich. Dafür sollten Nachbauer das Mähwerk entfernen und so das Drehmoment reduzieren. (hch)