Werkstoffe: So wird ein Schuh draus
Schneller, fester, billiger – ein kalifornisches Start-up will den 3D-Druck von Kunststoffen endlich reif für die Massenproduktion machen.
- Katherine Bourzac
Ein schwarzer Metallarm senkt sich in ein Becken milchig-grauer Tinte. Langsam bewegt er sich wieder nach oben und zieht dabei ein glänzendes und tropfendes Plastikgitter aus dem Bad: das vergrößerte Modell einer porösen Knochenstruktur. Wir befinden uns im Labor von Carbon im kalifornischen Redwood City. CEO und Mitgründer Joseph DeSimone freut sich immer noch, seinen Maschinen bei der Arbeit zuzusehen. Bei ihnen handelt es sich um eine neue Generation von 3D-Druckern, die das Verfahren endlich reif für den Massenmarkt machen soll. Das mit 222 Millionen Dollar von Investoren wie GE Ventures und Google Ventures finanzierte Unternehmen nennt seinen Prozess allerdings nicht mehr 3D-Druck, sondern "digitale Lichtsynthese". Sein Slogan lautet: "Stop prototyping. Start producing".
Wenn der Arm ein Objekt Millimeter für Millimeter aus dem milchigen Bad herauszieht, wirkt es so, als würde er eine bereits vorhandene Struktur zum Vorschein bringen. Tatsächlich aber entsteht sie erst währenddessen. Ein Digitalprojektor wirft kontinuierlich ultraviolettes Licht auf die Unterseite. Dabei verfestigt es die lichtempfindliche Tinte.
Mit diesem Verfahren will Carbon drei zentrale Probleme lösen, die bisher dafür gesorgt haben, dass 3D-Druck eine Nischentechnologie geblieben ist: geringes Bautempo, begrenzte Auswahl an Materialien, mangelnde Festigkeit der fertigen Produkte. Auch andere Unternehmen wie HP und Desktop Metal arbeiten an der Überwindung dieser Hürden. Carbon bewegt sich also auf einem zunehmend umkämpften Gebiet. Eine immer länger werdende Liste zahlender Kunden deutet aber darauf hin, dass Carbon auf dem richtigen Weg ist.
Einer dieser Kunden ist Adidas. "Das Volumen und das Tempo, das wir mit der digitalen Lichtsynthese von Carbon erreichen können, sind beispiellos", sagt Paul Gaudio, Kreativdirektor des Sportartikelherstellers. "Es ist fast Zauberei." Adidas hatte verschiedene 3D-Drucker ausprobiert, um individualisierte Schuhe für den Massenmarkt zu produzieren, doch keiner davon ließ sich im großen Maßstab nutzen. Mit Carbon-Druckern will das Unternehmen nun elastische Mittelsohlen mit Gitterstruktur herstellen. Die mechanischen Eigenschaften der Sohle werden durch die Geometrie des Gittermusters beeinflusst – und so genau auf den Träger abgestimmt. Die ersten 5000 Paare sind für diesen Winter geplant. Bis 2021 sollen es Millionen werden. Weitere Carbon-Kunden drucken Teile für Elektromotorräder, Server-Farmen oder Kühlsysteme aus, die mit anderen Verfahren schwierig oder gar nicht zu realisieren wären.
3D-Druck für den individuellen Schuh (5 Bilder)
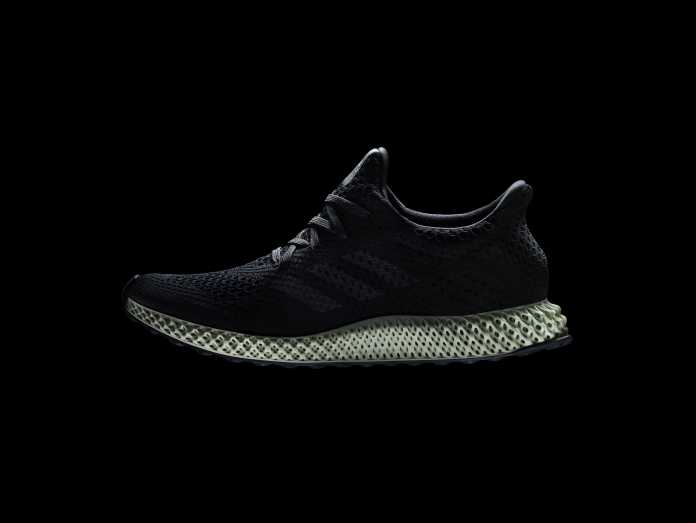
(Bild: Adidas)
Vor der Gründung von Carbon im Jahr 2013 war DeSimone mehr als 20 Jahre lang Polymerchemiker an der University of North Carolina. 2012, als die ersten 3D-Drucker für den Privatgebrauch gerade populär wurden, bekam er einen Anruf von Alex Ermoshkin, einem früheren Studenten. Ermoshkin hatte eine Geschäftsidee für ihn: Wie wäre es mit einem Start-up, das billigere 3D-Drucker entwickelt? DeSimone, der schon einige Erfahrungen mit der Technologie hatte, war begeistert. Eine Patentrecherche zeigte, was der Branche noch fehlte: Es gab praktisch nur Verfahren für den schichtweisen Aufbau von Objekten – etwa die Stereolithografie. Auch hier wird ein Harz mit UV-Licht gehärtet. Allerdings waren die verfügbaren Materialien weder besonders haltbar noch flexibel. Hinzu kommt, dass der Druck sehr langsam ist. Große Objekte können Stunden oder gar Tage brauchen.
DeSimone und Ermoshkin dachten darüber nach, wie man ohne Unterbrechungen drucken könnte. Inspirieren ließen sie sich vom humanoiden Roboter T-1000, der sich in dem Film "Terminator 2" aus einem Bad mit metallischer Flüssigkeit erhebt. Das Ergebnis war ein 3D-Drucker, der die herkömmliche Stereolithografie im Wortsinn auf den Kopf stellte. Während das Harz dort normalerweise von oben belichtet wird und das entstehende Objekt dann Schicht für Schicht in ein Bad aus flüssigem Harz abgesenkt wird, ist es bei Carbon genau umgekehrt: Ein Projektor projiziert ein Lichtmuster von unten durch eine Scheibe auf das Harz – wie einen Film auf eine Leinwand. Das Harz härtet dabei aus, und ein Druckarm zieht das Objekt kontinuierlich nach oben aus dem Tank. Um seine finale Festigkeit zu erreichen, muss es anschließend noch in einen Ofen.
Auf dem Weg zur praktischen Umsetzung mussten die Gründer zahlreiche Probleme lösen. Ein kleines, aber entscheidendes Detail war zum Beispiel die Frage: Wie lässt sich verhindern, dass die Objekte am Boden des Beckens kleben bleiben, während sie belichtet werden? Die Lösung war ein sauerstoffdurchlässiges Fenster. Der Sauerstoff unterbindet die Polymerisation und schafft eine trennende Schicht zwischen Objekt und Bodenfenster. Sie ist so dünn, dass Licht problemlos durchdringen kann, aber dick genug, um frisches Harz nachfließen zu lassen.
Laut DeSimone kann das Verfahren Tausende Male schneller arbeiten als klassischer schichtweiser 3D-Druck. Zudem haben die Produkte eine glatte Oberfläche und sind in jeder Richtung gleich belastbar. Als Rohstoff stehen mittlerweile zwölf Materialklassen zur Verfügung – von fest bis elastisch, von diversen Polyurethan-Varianten über Epoxidharze und Elastomere bis hin zu Cyanat-Estern, die Temperaturen von mehr als 200 Grad verkraften. Allein für die individuellen Schuhsohlen hat Carbon gemeinsam mit Adidas 150 verschiedene Varianten eines Elastomers entwickelt und ausprobiert. Für die Zukunft schwebt DeSimone ein "App Store für Harze" vor, in dem Kunden alles bestellen können, was sie zum Drucken brauchen.
Im Eingangsbereich des Hauptgebäudes zeigt ein großer Bildschirm den Betriebszustand aller Drucker des Unternehmens an, ob vor Ort oder bei Kunden. Carbon vertreibt die Geräte mit einem Abonnentenmodell und arbeitet dann zusammen mit den Kunden an der Auswahl der richtigen Designs und Materialien. Ungefähr alle sechs Wochen werden Software-Updates eingespielt, die auf den in der Praxis gesammelten Erkenntnissen basieren – eine Vorgehensweise, die Carbons Vice President für Technik, Craig Carlson, bei seinem früheren Arbeitgeber Tesla kennengelernt hat. Inzwischen entwickelt das Unternehmen auch Maschinenlern-Software, die für jedes Produkt das optimale Design und die besten Parameter finden soll. "Wir wollen die Probleme sehen, bevor wir drucken", sagt DeSimone. (bsc)