Nachhaltiger Beton: Wie der graue Baustoff klimafreundlicher werden kann
Beton ist für bis zu zehn Prozent des weltweiten CO2-Ausstoßes verantwortlich. Ihn zu senken ist kompliziert. Forscher arbeiten daran – auch an seiner Ästhetik.
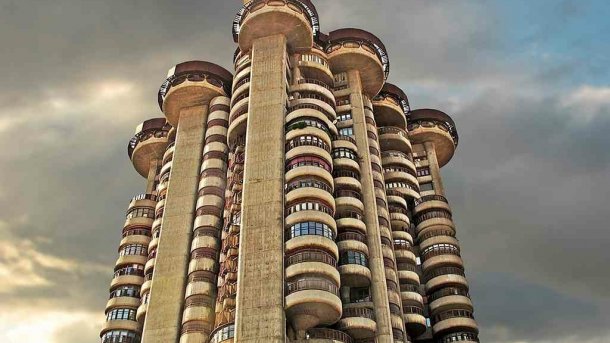
Die 71 Meter hohen „Torres Blancas“ in Madrid zeigten schon 1969, wie vielfältig Betonbauten sein können.
(Bild: Jacinda Lluch Valero)
Wolfram Schmidt hat viel zu erzählen. Entsprechend rasant ist sein Redetempo. Innerhalb einer knappen Stunde spannt er am Telefon den Bogen von der Maniokwurzel zum Hochhaus, von der Chemie zur Logistik, von der Ausbildung zur Normung. Der graue Werkstoff Beton, das wird spätestens nach einem Gespräch mit Schmidt klar, hat viele bunte Facetten. Von Architekten geliebt und vom Publikum beargwöhnt, drängt sich nun ein neuer Aspekt ins öffentliche Bewusstsein: seine Klimabilanz.
Beton ist nach Wasser der am meisten von Menschen benutzte Stoff überhaupt. Er besteht in erster Linie aus Kies und Sand, die von Zement zusammengehalten werden. Allein dessen Herstellung ist, je nach Quelle, für satte sechs bis zehn Prozent des weltweiten CO2-Ausstoßes verantwortlich. Tendenz: vermutlich steigend, denn gerade Schwellenländer haben einen großen Aufholbedarf. "80 Prozent der Gebäude, die 2050 in Afrika stehen werden, sind noch gar nicht gebaut", sagt Schmidt. "Afrika könnte ein Pionier werden für grünes Bauen."
Er selbst arbeitet an der Bundesanstalt für Materialprüfung (BAM) mit unkonventionellen Ideen daran, Beton klimafreundlicher zu machen. Die schlechte Nachricht ist: Man muss dazu immer an mehreren Stellschrauben gleichzeitig drehen, denn die CO2-Emissionen fallen auf verschiedenen Wegen an. Die gute: Es gibt reichlich Ansätze, die Klimabilanz trotzdem zu verbessern. Sie bringen Farbe in die graue Welt des Betons.
Heute ist mit "Zement" meist grauer "Portland-Zement" gemeint, benannt nach dem gleichfarbigen Kalkstein der gleichnamigen südenglischen Halbinsel. Ob in Säcken abgefüllt oder im Betonmischer angeliefert, ob beim Stahlbeton einer Autobahnbrücke oder beim Mörtel einer Ziegelwand – die grundlegende Rezeptur ist im Wesentlichen immer die Gleiche. Das freut Normungsgremien und Bauingenieure, denn es macht ihre Arbeit einfacher. Aber es ist auch ein Grund für die verheerende Klimabilanz, denn oft passt Portland-Zement nur mittelgut zu einer bestimmten Anforderung. So vielfältig die Anwendungen von Zement, so vielfältig ist auch die Möglichkeit – und Notwendigkeit – ihn für bestimmte Aufgaben maßzuschneidern.
Klassischer Portland-Zement besteht im Wesentlichen aus gemahlenem Kalkstein, Ton, Sand und Eisenerz, die in einem Drehrohrofen bei rund 1450 Grad zu "Klinker" gebrannt werden. Dabei wandelt sich Kalkstein (Calciumcarbonat, CaCO3) zu Calciumoxid (CaO, vulgo "gebrannte" oder "ungelöschter" Kalk). In diesem Prozess wird CO₂ chemisch freigesetzt. Rund 60 Prozent der insgesamt 600 bis 900 Kilo Kohlendioxid, die bei der Herstellung einer Tonne Zement entstehen, gehen aufs Konto dieser Quelle, der Rest auf die Erzeugung der Wärme. Und genau hier liegt das Problem: Den Wärmebedarf kann man durch Abfallstoffe oder klimaneutrale Wärmequellen decken. Doch was ist mit dem Rest?
"Beton steht überall zur Verfügung"
Beton komplett zu ersetzen, etwa durch Holz, sei jedenfalls keine Lösung, meint Wolfram Schmidt. "Gerade in Schwellenländern wurde oft schon zu viel abgeholzt. Beton ist der einzige Rohstoff, der überall zur Verfügung steht. Die häufigsten Elemente der Erdkruste – Sauerstoff, Silizium, Aluminium, Eisen, Natrium, Kalium und Calcium – sind gerade die Elemente, aus denen Beton hergestellt wird."
Und wie sieht es mit den Möglichkeiten aus, Beton einzusparen? Ein heißes Thema in Architektenkreisen ist derzeit der 3D-Druck von Gebäuden. Da die Drucker nur dort Beton auftragen, wo er aus statischen Gründen wirklich gebraucht wird, kommen sie insgesamt mit weniger Material aus. "Dafür brauchen sie allerdings schnell erhärtende Betonrezepturen, was einen höheren Anteil an klimaschädlichem Zement bedeutet", wendet Schmidt ein. Deshalb sei 3D-Druck, anders als oft dargestellt, nicht von Natur aus nachhaltig.
Architektonische Zurückhaltung
Schmidt plädiert daher für architektonische Zurückhaltung – etwa bei großen Abständen, die Decken oder Böden ohne Stützen überbrücken müssen. "Architekten lieben das, aber Betonträger erreichen dadurch mitunter absurde Ausmaße." Allein die Erhöhung einer Stützweite von 5 auf 6,25 Metern steigere den Materialbedarf um rund 30 Prozent. Zudem seien Hochhäuser wahre Betonfresser, weil die unteren Etagen die oberen tragen müssen. Ein zehnstöckiges Gebäude kommt beim Bau laut Schmidt auf die 5,5-fachen CO2-Emissionen eines vergleichbaren ebenerdigen Baus.
Zement muss klimafreundlicher werden
Allerdings zersiedeln flachere Bauten auch die Landschaft und führen zu mehr Verkehr. Es hilft also nichts: Der Zement selbst muss klimafreundlicher werden. Die naheliegendste Möglichkeit ist es, das entstehende Treibhausgas einfach abzufangen und einzulagern (CCS, "Carbon Capture and Storage"). Dies ist der bevorzugte Weg der großen Zementhersteller. Die Verfahren dazu sind aus fossilen Kraftwerken bekannt: Entweder wird der Klinker mit reinem Sauerstoff gebrannt ("Oxyfuel"), dann entsteht ein Abgasstrom mit hochkonzentriertem CO2, das sich relativ leicht abfangen lässt. Ein Konsortium um HeidelbergCement will eine entsprechende Demonstrationsanlage im baden-württembergischen Mergelstetten aufbauen. Einen Kreislauf-Ansatz verfolgt der Wettbewerber LafargeHolcim im schleswig-holsteinischem Lägerdorf: Dort soll der nötige Sauerstoff aus der Elektrolyse von Wasser stammen. Der dabei entstehende Wasserstoff soll sich mit dem abgeschiedenen Kohlendioxid aus der Zementherstellung zur Basischemikalie Methanol verbinden.
Das Oxyfuel-Verfahren erfordert allerdings hohe Investitionen in die Zementfabriken und lässt sich nicht nachrüsten. Die sogenannte Aminwäsche kann hingegen auch nachträglich in einem Zementwerk installiert werden, braucht allerdings mehr Energie. In Norwegen will HeidelbergCement auch dieses Verfahren testen. Ein weiteres Konzept verfolgt der Konzern mit dem "Leilac"-Verfahren: Dabei werden die Zement-Ausgangsstoffe in einer Stahlröhre von außen erhitzt, sodass sich die Abgasströme von der Wärmeerzeugung und der chemischen Reaktion getrennt voneinander auffangen lassen. Ein Versuchswerk in Belgien besteht bereits, eine größere Anlage soll in Hannover folgen.
Doch alle diese Verfahren haben drei Nachteile: Sie sind teuer, energieintensiv und es ist völlig offen, was mit dem abgetrennten CO₂ passieren soll: Die Verpressung in den Untergrund ist politisch hoch umstritten und einen nennenswerten Markt für die Verwendung des Klimagases gibt es nicht. CCS könne die Kosten der Klinkerproduktion um den "Faktor zwei bis drei" erhöhen, heißt es in der Studie "Eco-efficient cements" des UN Environment Programmes – und damit auch die Preise für Häuser und Infrastruktur. "Das hätte signifikante soziale Folgen in Entwicklungsländern. Da der meiste Zement jetzt und in Zukunft in Entwicklungsländern produziert wird, sind kostengünstigere Varianten hochgradig wünschenswert."
Lesen Sie auch
Innovation: Die ganz natürliche Industrie
Wie also lässt sich Zement dazu bringen, schon bei der Herstellung weniger CO₂ auszustoßen? Dazu muss man tiefer in die Chemie einsteigen. Klinker besteht chemisch betrachtet aus einer Reihe von Oxiden, vor allem von Calcium, Aluminium, Silizium und Eisen. Kommen sie mit Wasser zusammen, kristallisieren sie zu festen Hydrat-Komplexen aus. Während aber Siliziumoxid (als Sand) und die übrigen Oxide (als Erze) reichlich in der Erdkruste vorkommen, ist Calcium vor allem in Form von Kalkstein (CaCO3) reichlich und preiswert verfügbar. Dieser ist im Wesentlichen für den CO2-Ausstoß beim Brennen verantwortlich.
Nachhaltige Alternative: Verwertung der Maniokschalen
Es gibt zwar etablierte Alternativen zu Kalk, etwa Flugasche aus Kohlekraftwerken oder Schlacke aus Hochöfen, die schon heute zu großen Teilen dem Zement zugesetzt werden. Doch ihr Anteil lässt sich kaum noch steigern, denn praktisch das gesamte verfügbare Material landet bereits in der Zementindustrie. Außerdem ist es mangels Industrie in den wenigsten Schwellenländern vorhanden.
Gefragt sind also Ersatzstoffe, die es reichlich vor Ort gibt – so wie die Schalen von Maniok (Cassava). Die Pflanze wächst auf praktisch jedem Boden, ihre Wurzeln sind in Ländern wie Nigeria ein Grundnahrungsmittel, ihre Schalen aber bislang unverwertbarer Abfall, der nicht einmal als Viehfutter taugt und meist in großen Haufen vor sich hin rottet. Wolfram Schmidt hat nun mit Kolleginnen und Kollegen aus Nigeria und Ghana ein Verfahren entwickelt, den Abfallstoff gleich mehrfach zu verwerten: Aus der restlichen an der Schale haftenden Stärke lassen sich zum Beispiel Polysaccharide gewinnen. Sie können Zusatzmittel aus der Erdöl-Chemie ersetzen, welche die Verarbeitung des Zements erleichtern. Die verbliebenen Schalen können unter Sauerstoffabschluss verkohlt ("pyrolysiert") und anschließend bei 750 bis 850 Grad gebrannt werden. Dabei entsteht eine Asche, die ähnlich wie klassischer Portland-Zement mit Wasser reagiert und 20 bis 40 Prozent davon ersetzen kann. Der entstehende Beton ist allerdings nicht mehr unbedingt grau, sondern je nach Austauschmenge braun.
Dauerhaftigkeit testen
Auch aus anderen Pflanzenabfällen wie Zuckerrohrresten oder Maiskolben lässt sich hervorragender Zement herstellen. "Asche aus Reisschalen hat sogar eine höhere Festigkeit als klassischer Zement, das ist sozusagen der Rolls Royce unter den Aschen", so Schmidt.
Eine dazu nötige Ofenlinie für Lehr- und Forschungszwecke hat Schmidt mit seinen Partnern, unterstützt vom Bundesforschungsministerium, auf dem Campus der University of Ghana errichtet. "Das Ganze ist nicht völlig CO2-neutral, aber schon deutlich weniger CO2-intensiv", sagt Schmidt. Genaue Zahlen, wie viel Kohlendioxid im großen Maßstab eingespart werden könnten, habe er leider nicht. Für sein Projekt zur Verwertung von Maniokschalen in Nigeria bekam er 2018 den Deutsch-afrikanischen Innovationsförderpreis des Bundesforschungsministeriums.
Neues Baumaterial anfassbar machen
Mit dem Geld will er nun ein Haus aus Maniok-Beton bauen, um eine zentrale Frage zu beantworten: "Bei jedem Vortrag ist immer irgendjemand im Publikum, der fragt: Was ist mit der Dauerhaftigkeit?", so Schmidt. "Woher soll ich das genau wissen, wenn es noch keiner jemals gemacht hat? Deshalb muss man das ausprobieren und anfassbar machen." Eigentlich sollte das Haus im Jahr 2020 gebaut werden, doch dann kam Corona dazwischen. Im Oktober soll es nun weitergehen.
Würde man alle verfügbaren Maniokschalen sammeln und weiterverarbeiten, ließe sich damit 2,5 bis 5 Prozent des Zements in Nigeria ersetzen, heißt es in einem Paper von Schmidt. Damit ist klar: Für eine flächendeckende Dekarbonisierung reicht das nicht. Aber die Welt des Betons ist vielfältig, und es muss nicht immer Maniok sein. Schmidt: "Das Wunderbare an Beton ist, das man überall auf der Welt mit lokalen Bindemitteln bauen kann." Dazu müsse man keinen Hüttensand aus Pakistan nach Kenia bringen oder Maniokschalen aus Afrika in die Schweiz. Um genau zu erfahren, welche Reststoffe man wo zu welcher Zeit am besten entnehmen könne, sei eine Datenbank mit Künstlicher Intelligenz wünschenswert, die berechnet, mit welchen Stoffen gewünschte technische Eigenschaften erreicht werden können und ob die Versorgungsketten die benötigten Mengen auch hergeben. Bisher sei solch eine KI aber "leider nur ein Wunsch", so Schmidt.
Die UN-Studie sieht für Pflanzenasche zwar durchaus interessante Möglichkeiten auf regionaler Ebene. Größeres Potenzial sieht sie aber in "kalzinierten Tonen". Ton – besonders, wenn er das Aluminium-Silizium-Mineral Kaolinit enthält – wird reaktiv, wenn er bei 700 bis 850 Grad gebrannt wird, also bei deutlich niedrigeren Temperaturen als Kalkstein. Er steht laut UN-Studie weltweit "praktisch unbegrenzt" zur Verfügung. Auch Schmidt hält sie "in Verbindung mit Kalksteinmehl von den reinen Mengen her global für einen wesentlichen Teil der Lösung". Allerdings können ihre Eigenschaften regional sehr unterschiedlich ausfallen. "Es funktioniert, aber man muss mit viel mehr Wissen und Forschung an das Bindemittel ran und dafür fehlt es global noch an Kenntnissen." Das größte Manko sei aber das mangelnde Vertrauen der Verbraucher in Neuentwicklungen. "Der Beton hat plötzlich eine andere Farbe und schon sind die Leute skeptisch."
Weiteres Finetuning der Prozesse
Oft sind es aber keine mehr oder minder exotischen Materialien, die den größten Hebel bieten, sondern Finetuning der Prozesse – zum Beispiel beim Mahlen und Mischen. Zement besteht nämlich nicht nur aus chemisch reaktivem Klinker, sondern auch aus einem "Füller", meist bestehend aus schlichtem ungebrannten Kalkstein. Wasser und Klinker durchdringen die Lücken zwischen den Partikeln dieses Füllers und verfestigen das Gemisch. Wenn aber die Korngröße so optimiert ist, dass die Lücken dazwischen möglichst klein werden und ein chemisches Dispersionsmittel für eine gleichmäßige Durchmischung sorgt, ist bei gleicher Festigkeit weniger Klinker nötig. Schon heute werden handelsüblichem Zement 5 bis 35 Prozent Füller zugesetzt. Allein das "optimierte Mix-Design" könne den Anteil an Füller ohne Zugeständnisse bei der Festigkeit auf über 50 Prozent erhöhen, heißt es in der Studie von UN Environment. Damit ließe sich die Öko-Effizienz von Zement um den Faktor vier gegenüber der schlechtesten Variante verbessern.
Eine große Stärke des Portland-Zements ist gleichzeitig auch eine weitere Schwäche: der bequeme Umgang mit ihm. Gerade in Schwellenländern kommt meist ein Standard-Zement im Sack auf die Baustelle und wird erst dort zu Beton angesetzt – oft mit einem übertrieben großzügigen Anteil an Zement. Würde Beton verstärkt unter genau definierten Bedingungen in Fabriken angesetzt und fertig gemischt zur Baustelle gebracht, ließen sich nach Schätzung der UN-Studie rund zehn Prozent des Zements einsparen. In China ist das Ansetzen von Beton direkt auf der Baustelle schon seit 2003 verboten. Das funktioniert allerdings nur in Städten, wo die Anfahrtswege nicht zu lang sind.
"General Purpose" nicht sinnvoll
"Wir glauben, dass der ‚General Purpose‘-Ansatz für Zement-Standards eine große Hürde für die umweltfreundliche Optimierung ist", schreiben die Autoren des UN-Reports. Zum Beispiel ist Universal-Zement in der Regel stark alkalisch, weil sich aus einem Teil des Kalksteins Calciumhydroxid (CaOH) bildet. Das soll Stahlarmierungen vor der Korrosion schützen, trägt aber selbst nichts zur Festigkeit bei.
Nun ist es aber so, dass nur rund ein Viertel des Zements in Stahlbeton landet – der Rest geht in Putz, Mörtel oder Fertigprodukte aus Beton, wo ein hoher pH-Wert gar nicht nötig ist. Also ließen sich dort auch problemlos kalkärmere Alternativen mit besserer Treibhausgasbilanz einsetzen. Oder auch Zemente, die nicht mit Wasser aushärten, sondern durch "Carbonisierung": Sie nehmen Kohlendioxid aus der Luft auf und binden es chemisch. Solche Zemente sind keine CO2-Quelle mehr, sondern sogar CO2-Speicher.
"Neue Zement-Techniken haben Potenzial"
Leider funktioniert das nur unter genau definierten Bedingungen, weil sichergestellt werden muss, dass der Zement beim Aushärten ausreichend Kontakt mit dem Kohlendioxid bekommt. Auf einer Baustelle dürfte das schwierig werden – nicht aber in einer Fabrik für Fertigteile wie Wände, Träger, Platten oder Ziegel. Die US-Firma Solidia Cement hat ein solches Verfahren nach eigenen Angaben bereits in 50 Zementfabriken in 10 Ländern erfolgreich demonstriert. Ihr Verfahren lasse sich in normalen Brennöfen durchführen, beschleunige die Aushärtung und verbrauche weniger Wasser und Energie, so Solidia.
"Das Potenzial der neuen Zement-Techniken ist ermutigend", schreiben die Autoren der UN-Studie. "Sie werden voraussichtlich mehr kosten als gegenwärtiger Zement, aber viel weniger als Kohlendioxid-Abscheidung." Und sie werden eine flexiblere Normierung benötigen. "Die ganze Normung ist nicht mehr zeitgemäß", sagt Wolfram Schmidt. "Sie basiert im Grundsatz nach wie vor nur auf Beton aus Portland-Zement." Um das zu ändern, arbeitet er in einem weltweiten Netzwerk, dem GLOBE – Global Consensus on Sustainability in the Built Environment, an den Grundlagen für eine aktualisierte Normung.
Damit einher müsse auch eine bessere Ausbildung gehen, fordert Schmidt: "Bauingenieure werden nicht über die Chemie des Zements ausgebildet und Themen der Nachhaltigkeit fließen nur langsam in die Lehrpläne ein. Oft sind sie nur noch Erfüller von Normen, die dann oft nicht mal mehr zeitgemäß sind. Das Denken und Entwickeln, was ja eigentlich die Uraufgabe von Ingenieuren ist, bleibt da häufig auf der Strecke."
(bsc)