Batteriezellen in Elektroautos: Zylindrisch, prismatisch oder Pouch
Kein Zellformat hat sich bisher durchgesetzt, alle probieren alles. Im Batteriesystem eines E-Autos muss das Paket aus Leistung, Sicherheit und Kosten passen.
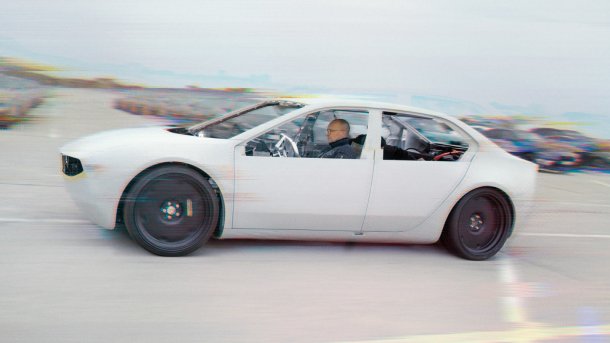
BMW bringt 2025 die elektrische Neue Klasse mit einer Traktionsbatterie aus Rundzellen 4695 des Zulieferers EVE.
(Bild: BMW)
- Christoph M. Schwarzer
Über viele Jahrzehnte stand bei der Weiterentwicklung des Antriebsstrangs in Autos der Motor im Fokus. Mit der Umstellung auf den batterieelektrischen Antrieb verschiebt sich das, denn nun steht die Batteriezelle im Mittelpunkt des Interesses. Global werden aktuell riesige Summen investiert, um hier Fortschritte zu erreichen. Energiedichte, Haltbarkeit, Ladeleistung und vor allem die Kosten sind es, die optimiert werden müssen, wenn der batterieelektrische Antrieb überall auf der Welt eine Chance haben soll.
In einer Artikelserie wollen wir zeigen, wo wir heute stehen und wohin die Entwicklung geht. Den politischen Rahmen hat die Europäische Union gesetzt: Ab 1. Januar 2035 dürfen ausschließlich Pkw neu zugelassen werden, die keine direkten CO₂-Emissionen haben. Nach heutiger Einschätzung werden das weitestgehend batterieelektrische Autos sein. Weil die Industrie nicht einfach ein- und ausgeschaltet werden kann, wird es in den knapp zwölf Jahren bis zum Stichtag einen kontinuierlichen Hochlauf geben.
Rund, eckig oder flexibel? Die Verpackung von Batteriezellen war und ist ein wichtiger Aspekt für die Funktion eines Batteriesystems im Elektroauto: Es kommt aufs Format an. Meistens werden drei Grundformen unterschieden. Die Rundzelle (auch zylindrisch genannt), die prismatische Zelle – ähnlich einem flachen und harten Kasten – sowie die Pouchzelle, deren Übersetzung Beutel auf das flexible Äußere hinweist. Keines dieser Formate hat sich als eindeutig beste Lösung marktbeherrschend durchgesetzt. Im Gegenteil: Viele Hersteller probieren alles aus.
In allen Fällen geht es darum, aus vielen Einzelzellen ein funktionierendes Batteriesystem zu bauen. Die Zellen werden parallel und seriell verschaltet. Sie müssen gekühlt und geheizt werden, um optimal zu arbeiten. Die Sicherheit muss gewährleistet sein. Gewicht und Gesamtvolumen des Batteriesystems sollen niedrig sein. Und natürlich muss der Preis stimmen. Aber was sind die spezifischen Vor- und Nachteile der unterschiedlichen Batteriezellformate?
Tesla hat den Anfang gemacht
Am bekanntesten ist wahrscheinlich die Rundzelle: Ein wesentlicher Durchbruch von Tesla war, industriell gefertigte Rundzellen zu einem System zusammenzufassen. Womit die erste Stärke bereits genannt ist – Rundzellen sind in großen Stückzahlen verfügbar, und es gibt eine sehr große Erfahrung bei der Produktion. 18650er-Zellen (für 18 Millimeter Durchmesser und 65 Millimeter Höhe) sind bis heute ein Standard in vielen Elektrogeräten. Das Produktionsverfahren ist massenhaft bewährt: Lange Streifen von Schichten der Materialien werden aufgerollt.
(Bild: Tesla)
Wie alle Zellen können Rundzellen unterschiedliche chemische Zusammensetzungen haben. Das gilt unabhängig von anderen Größen wie 2170 oder 4680. Rundzellen haben zusammen mit Pouchzellen eine besonders hohe volumetrische Energiedichte. In einem vorgegebenen Bauraum lässt sich vergleichsweise viel elektrische Energie speichern. Sie sind mechanisch belastbar, verwindungssteif und dicht. Rundzellen überstehen auch einen gewissen Innendruck. Eine Schwäche ist dagegen die Wärmeabfuhr; eine aktive und leistungsfähige Kühlung muss gewährleistet sein, und der Bauraum könnte noch besser ausgenutzt werden, wenn die Zellen eben nicht rund wären.
Das hält aber BMW nicht davon ab, für die zukünftige Neue Klasse (ab 2025) durch das Unternehmen EVE 4695-Rundzellen (46 Millimeter Durchmesser und 95 Millimeter Höhe) entwickeln zu lassen. Die gravimetrische Energiedichte – also nicht auf den Bauraum, sondern bezogen auf das Gewicht – könnte bei 260 bis 280 Wattstunden pro Kilogramm (Wh/kg) liegen. Für die SUVs von BMW ist außerdem eine 46125-Rundzelle mit 125 Millimeter Höhe in Arbeit.
Volkswagen zum Beispiel möchte ab 2025 die Einheitszelle in die Serienproduktion einbringen. Damit ist nicht die Zellchemie – die kann sehr wohl variieren –, sondern das Format gemeint: Eine prismatische Zelle, die in bis zu 80 Prozent aller Elektroautos integriert werden kann. Ein Ziel des normierten Formats bei Volkswagen ist die Kostensenkung durch Skaleneffekte.
(Bild: CATL)
(Bild: BMW)
Prismatische Zellen haben ähnlich wie Rundzellen eine hohe Steifigkeit und Dichtigkeit. Die mechanische Stabilität ist etwas geringer als bei Rundzellen, und sie müssen ebenfalls aufwendig gekühlt werden. Der praktische Vorteil dieses Formats liegt vor allem in der Einfachheit des Verbaus und der guten Packungsdichte; es wird kaum Bauraum verschenkt. Der logische und simple Einbau ins Batteriesystem kann auch langfristig eine Stärke sein, wenn etwa ein Refurbishment notwendig wird.
(Bild: Audi)
Zu den prismatischen Zellen gehört letztlich auch die sogenannte Blade-Batterie von BYD. Blade ist übersetzt die Klinge, und tatsächlich ähnelt die Einzelzelle von BYD der Klinge eines Schwerts: Lang, schmal und flach. BYD, der nach CATL und LG bedeutendste Hersteller der Welt, baut Batterien sowie Elektroautos und hat somit eine hohe Fertigungstiefe. Bei der Zellchemie setzt BYD auf die robuste und kostengünstige Lithium-Eisenphosphat-Variante (LFP). Das System kann sowohl mit 400 als auch mit 800 Volt Bordspannung arbeiten; es kommt hier allein auf die parallele und serielle Verschaltung der Zellen an. Das Format ist wie gehabt nur die äußere Form, die weiteren Parameter wie die Zellchemie oder die Spannung haben nichts oder nur indirekt damit zu tun.
(Bild: BYD)
Kein Format hat sich final durchgesetzt
Weit verbreitet und trotzdem zuletzt etwas zurückgefallen ist die Pouchzelle. Sie hat – ähnlich den Rundzellen – eine hohe volumetrische Energiedichte. Anders als bei den anderen Formaten ist die Hülle (meistens aus Aluminium) aber weich und flexibel. Wegen dieser Instabilität müssen Pouchzellen in ein deutlich schützendes Gehäuse integriert werden. Der Nachteil der dünnen und flexiblen Hülle ist zugleich ein Vorteil. So gelingt die Wärmeabfuhr leichter; die Kühleigenschaften sind besser. Sie lassen sich darum leicht stapeln. Viele Hersteller setzen Pouchzellen weiterhin ein.
(Bild: Audi)
Fazit: Kein dauerhafter Vorteil für bestimmte Formate
Bisher ist es keinem Auto- oder Batteriehersteller gelungen, über ein bestimmtes Zellformat einen dauerhaften Vorteil zu reklamieren. Das liegt letztlich an den vielfältigen und nicht einheitlichen Anforderungen, die an ein Batteriesystem aus vielen Einzelzellen gestellt werden.
So sind die Kosten in den unteren Fahrzeugsegmenten sehr viel bedeutsamer als in der Luxusklasse. Und wie gut Zellen innerhalb eines Systems geheizt oder gekühlt werden, hängt eher von Anordnung, Größe und Leistung der Heiz- und Kühlflächen ab als vom Zellformat. Konstant bleibt allein der Aspekt der Sicherheit – sie muss vorhanden und hoch sein. Im Betrieb und auch beim Unfall.
Artikelserie Elektroauto-Batterien: Der aktuelle Stand bei den Batterien
Batterien für Elektroautos Teil 2: Das Potenzial der Anode
Batterien für Elektroautos Teil 3: Die Zukunft - Natrium statt Lithium
Batterien in Elektroautos Teil 4: Refurbishment statt Tausch gegen Neuteil
Artikelserie Elektroauto-Batterien: Warum die Vorkonditionierung so wichtig ist
(fpi)