Ladestecker-Hülle mit 3D-Drucker und Blender herstellen
Wo man früher Fragmente zusammenklebte und dann das Ganze in Epoxy versenkte, baue ich heute lieber mit 3D-Software und -Drucker individuelle Ersatzteile.
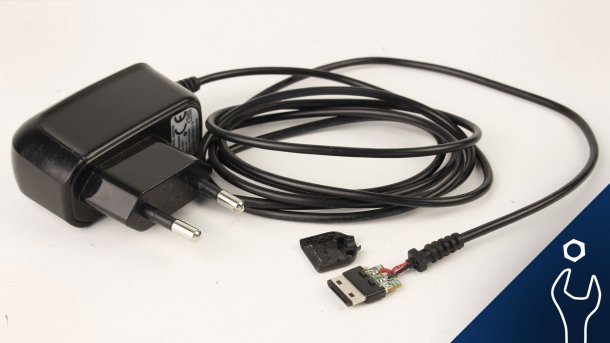
- Peter König
Als 3D-Software nehme ich meistens Blender – damit kenne ich mich inzwischen gut aus, weil ich gerne auch mal was realistisch rendere oder kleine Animationsfilme mache. Das eine oder andere Rendering hat es in den vergangenen Jahren sogar auf das Make-Cover gebracht. Durch eine gewisse Routine mit Blender brauche ich inzwischen selten mehr als eine knappe Stunde für die Konstruktion eines maßgeschneiderten Ersatzteils (Download via GitHub).
Beim Ladegerät eines betagten, aber immer noch von ihrer Besitzerin geliebten Klapphandys aus der Prä-Smartphone-Ära hatte sich das filigrane proprietäre Ladesteckerchen in seine Bestandteile aufgelöst. Eines der Hüllenteile war zwar noch vorhanden (es hing mit etwas Klebefilm am Kabel), aber eine Kopie davon wäre aufgrund vieler Rundungen aufwändig zu konstruieren und nur mit vielen Stützen druckbar. Zudem ist mir schleierhaft, wie die beiden Kabel im Inneren der Schalen ihren Platz finden sollten – sie waren dafür offenbar viel zu lang.
Da Kabel und Lötstellen noch intakt waren, wollte ich daran nicht viel rumbiegen und entschied mich, lieber eine neue Steckerhülle drumherum zu entwerfen. Eleganz war kein Kriterium, das ganze sollte leicht zu drucken, solide zu kleben und gut zu greifen sein. Also kam als Grundform ein Quader mit einem abgerundeten Ende heraus. Die war in Blender schnell angelegt.
Blockbauweise
Jetzt galt es "nur" noch, das vorhandene Innenleben zu geometrischen Grundformen reduziert in Blender (Download) nachzubauen und die dann von der Grundform mittels Bool-Modifier abzuziehen. Weil in diesem Fall alles in Bezug auf oben und unten sowie rechts und links als symmetrisch erwies, konnte ich mich darauf beschränken, nur eine halbe Schale zu konstruieren, die später zweimal gedruckt wurde. Außerdem nutzte ich, wo es ging, Mirror-Modifier.
Ich kenne das: Messschieber und Werkstück nehmen, messen, beides hinlegen, zu Tastatur und Maus greifen, auf den Bildschirm schauen – wie war das Maß nochmal genau? Deshalb messe ich lieber erst alles aus und mache mir eine Skizze. Die muss nur für die nächste Stunde und nur für mich verständlich sein und so sieht sie meistens auch aus. Macht nichts, die wandert danach in die Tonne.
Nach der Skizze waren dann der Zylinder für das ummantelte Kabel vom Steckernetzteil sowie der zwischengeschaltete Quader für die Zugentlastung schnell platziert und auf Maß gebracht. Den Kabelzylinder habe ich der Einfachheit halber weiter ins Innere des Steckers durchgezogen, das kam von den Maßen hin.
Klare Formen und Maße gab es auch auf der anderen Seite, bei der Kunststoffmanschette mit herausstehenden Nasen, in der auf der einen Seite die winzige Platine und auf der anderen der eigentliche Steckkontakt sitzt. Die Manschette baute ich in Blender durch einen weiteren Quader mit einer draufgesetzten Querleiste für die Nasen nach (Unterteilen im Edit Mode mit dem Loop-Cut-Werkzeug, dann extrudieren). Blieb noch der vage Bereich dazwischen, der Platz für die Platine und die Kabel bieten musste. Dafür zog ich kurzerhand den Quader für die Manschette rüber zur anderen Seite (als Distanz stand in meiner Skizze was von 14 mm) und extrudierte noch etwas nach oben und unten. Das sollte passen.