Leichter leiser: Nockenwellenmodul aus Kunststoff
Kunststoff statt Leichtmetall: Nach einem Stahl-Plastik-Zylinder stellt das Fraunhofer-Institut nun ein seriennahes Nockenwellenmodul aus Faser-Kunstharz vor.
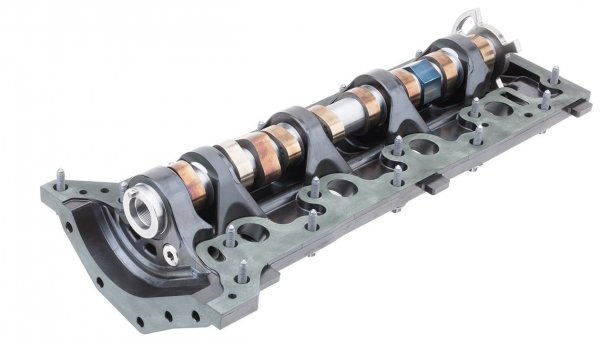
Das vom Fraunhofer ICT entwickelte Modul in Mischbauweise besteht größtenteils aus faserverstärktem Kunstharz.
(Bild: Fraunhofer ICT)
Moderne Verbrennungsmotoren stehen heute in unmittelbarer Konkurrenz zu den leisen, effizienten Elektroantrieben. Sparen heißt daher die Devise, und zwar vor allem an den Produktionskosten für die im Vergleich zu Elektromotoren unvergleichlich komplexen thermodynamischen Maschinen. Einen Beitrag soll Kunststoff leisten können.
Bisher eher anspruchslose Kunststoffteile
Schon heute bestehen die eher anspruchslosen Teile wie Zylinderkopfhaube, Ansaugtrakt oder Ölwanne von Verbrennungsmotoren häufig aus Kunststoffen. Das ist billiger, leichter und dämpft Geräusche schon am Motor. Vor rund fünf Jahren experimentierte das Fraunhofer-Institut für Chemische Technologie (ICT) sogar mit einem Zylinder in Kunststoff-Stahl-Verbundbauweise.
Nockenwellenmodul aus Kunststoff (4 Bilder)
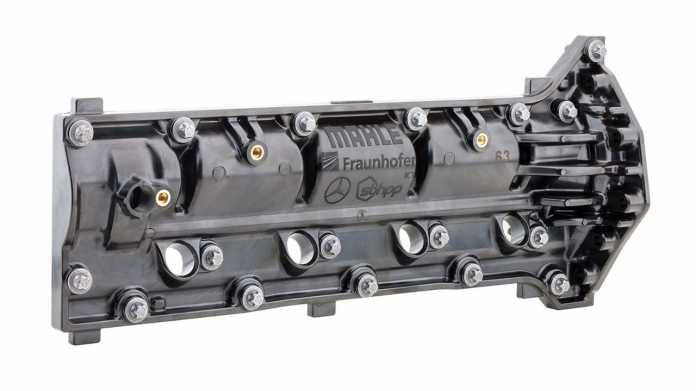
(Bild: ICT )
Vor allem das Downsizing dürfte in diesem Fall etwas zur Ernüchterung beigetragen haben, denn die modernen Verbrennungsmotoren arbeiten mittlerweile mit deutlich höheren Verbrennungsdrücken. Dabei treten Kräfte auf, die mit Kunststoffen nicht mehr einfach zu beherrschen sind. Der Kostenvorteil, für die Industrie ganz weit im Vordergrund, wäre dahin.
Heute ist es ein Nockenwellenmodul in Kunststoff-Verbundbauweise, das vom Fraunhofer ICT in Zusammenarbeit mit Partnern aus der Industrie wie dem Zulieferer Mahle und dem Autohersteller Daimler erprobt wird. Das Modul besteht aus dem Zylinderkopfdeckel, wie er für viele Motoren schon seit Jahren aus Plastik gebaut wird und einem Unterteil mit der Nockenwellenlagerung. Ein Aufbau, der sich nur für Motoren eignet, die bereits modular konstruiert wurden, das sind heute noch die wenigsten.
Bauweise erfordert Materialmix
Dieses Bauteil kann man günstig aus faserverstärktem gehärteten Kunstharz (Duromer) herstellen, wie das ICT zeigt. Wegen des grundsätzlich weniger festen Materials – die Steifigkeit des Duromers liegt nur bei einem Viertel dessen, was Aluminium bietet – haben die WissenschaftlerInnen die Lagerböcke für die Nockenwelle deutlich kräftiger dimensioniert. Um eine funktionale Materialpaarung herzustellen, läuft die stählerne Nockenwelle allerdings nicht direkt in den Lagerböcken, wie man das bei Aluminium-Zylinderköpfen zumeist macht, sondern in eigens dafür in den Kunststoff eingebetteten Buchsen aus Aluminium oder einem geeigneten Weichmetall.
Verminderte Schallabstrahlung
Die Pressemitteilung weist zurecht auf das gute Dämpfungsverhalten von Kunststoffen hin. Die Abstrahlung von hochfrequentem Rasseln, Klimpern und Klappern entsteht beim Grundmotor vor allem im Bereich des Ventiltriebs, zu dem die Nockenwelle ja gehört. Darüber hinaus spielt auch die Dämpfung der hörbaren Verbrennungsvorgänge eine Rolle, mittlerweile auch bei Downsizing-Ottomotoren. Aluminium leitet Schall besonders gut, viel besser als etwa Grauguss, das man daher gern für die Zylinderkurbelgehäuse verwendet. Bei grundsätzlich geringerer Schallabstrahlung eines in Teilen aus Plastik bestehenden Zylinderkopfes kann der Hersteller auf die übliche Kapselung in diesem Bereich verzichten, was die Komplexität unter der Motorhaube und die Produktionskosten gleichermaßen senken helfen kann.
Geringerer Fertigungs- und Energieaufwand
Das Fraunhofer-Institut reklamiert außer den Vorteilen bei Preis, Gewicht und Lärmdämmung auch einen geringeren Fertigungsaufwand. Das mag überraschen bei einem Bauteil, das im Gegensatz zu einem aus Leichtmetall aus mehreren Komponenten gefertigt werden muss. Die ForscherInnen halten dagegen, dass die Gussteile aufwendig nachbearbeitet werden müssen, während die faserverstärkten Kunstharzteile schon "endkonturnah" herstellen lassen sollen.
Ganz ohne Nachbearbeitung geht es aber auch damit noch nicht. Wichtig scheint auch die Lebensdauer von Duroplast-Spritzgusswerkzeugen im Gegensatz zu den Aluminium-Hochdruck-Gusswerkzeugen. Das Institut spricht von einer Lebensdauer von 500.000 Stück bevor das Werkzeug erneuert werden muss, gibt aber nicht an, wie lange das entsprechende für Aluminium hält.
Subventionierter Strom und Umweltschäden
Was die Hersteller perspektivisch beschäftigen könnte, ist zudem der hohe CO2-Ausstoß durch die energieintensive Produktion von Leichtmetallbauteilen. Er könnte sich durch den Einsatz von Kunstharz deutlich verringern lassen. Aber so weit ist es wohl noch nicht angesichts der gesetzgeberischen Rahmenbedingungen wie der Ausnahmen von der Energiebesteuerung gerade für die stromhungrige Aluminium-Industrie. Von den Umweltschäden durch die Bauxit-Industrie vor allem in Entwicklungsländern ganz zu schweigen.
Heiße Tests folgen
Erste Tests auf dem Prüfstand verliefen offenbar erfolgreich, wenn auch der Motor noch nicht mit eigener Kraft lief. 600 Stunden sogenannter geschleppter Versuche ergaben offenbar das erwartete, gute Verschleißverhalten. Als Nächstes sollen die Teile ihre Eignung in einem Kraft abgebenden Versuchsmotor unter Berücksichtigung der Gaskräfte und Temperaturbelastungen des Verbrennungsprozesses beweisen.
Ob die Industrie das Modul in der Serienfertigung einsetzen möchte, scheint sie sich immerhin anzuschauen, die Beteiligung von Mahle und Daimler an diesem Projekt zeigen es. Die staatliche Förderung durch das Bundesministerium für Wirtschaft und Energie (BMWi) ermöglicht es, das Fraunhofer-ICT für die Industrie kostengünstig als Entwicklungspartner einzubinden.
(fpi)