FAQ: Batterien in Elektroautos – Wie ist der Stand?
Zellchemie ist der Kern einer Batterie im E-Auto. Die Anforderungen sind vielfältig, für die Industrie geht es vor allem um Kosten. Wie ist der aktuelle Stand?
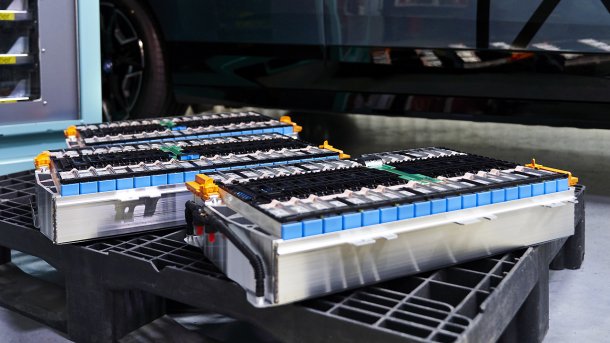
(Bild: BMW)
- Christoph M. Schwarzer
Die Traktionsbatterie ist das wichtigste Bauteil im Elektroauto. Jedes Batteriesystem ist aus vielen Zellen aufgebaut. In jeder dieser Zelle gibt es chemisch aktives Material. Der Aufbau aus Kathode, Anode und Elektrolyt ist die Basis für die Speicherung und Freigabe von elektrischer Energie: Strom fließt. Mal raus zum Elektromotor – wenn der Fahrer beschleunigen will –, mal rein, wenn per Rekuperation verzögert oder wenn am Netz geladen wird.
Die Zellchemie soll alles können: Viel elektrische Energie bei wenig Gewicht in geringem Bauraum sicher speichern, viel Strom in kurzer Zeit aufnehmen und abgeben können. Selbstverständlich soll die Batterie lange, lange halten. Vor allem aber soll sie günstig sein. Die Industrie arbeitet permanent daran, diese Parameter zu verbessern. Wir zeigen, wo Elektroautos bei der Zellchemie heute stehen – und was wir in naher Zukunft erwarten dürfen.
Wie hoch ist der Anteil des Aktivmaterials im Batteriesystem?
Weltmarktführer CATL aus China sagt, dass 72 Prozent des Qilin-Batteriesystems Aktivmaterial sind. Die Produktion dieses innovativsten und besten Systems von CATL läuft zurzeit an. Der Prozentanteil des Aktivmaterials ist wahrscheinlich Benchmark – wahrscheinlich, weil die meisten Hersteller den Integrationsgrad nicht transparent machen. Ein Ziel der Entwicklung von Batteriesystemen ist es, möglichst viel Aktivmaterial bei möglichst wenig Verpackung zu konstruieren, ohne dass die Sicherheit oder die Dauerhaltbarkeit leiden. Wenn das gelingt, steigen die gravimetrische und volumetrische Energiedichte automatisch; also die elektrische Energie, die pro Kilogramm oder pro Liter gespeichert werden kann. Wo weniger Material eingesetzt wird, sinken die Kosten.
Typisch für moderne Batteriesysteme ist das Weglassen der sogenannten Modulebene. In einem Modul sind mehrere Zellen – zum Beispiel zwölf – mit einem eigenen Softwaremanagement zusammengefasst. Diese Vorkonfektionierung hat es der Autoindustrie zu Beginn leichter gemacht, eigene Batteriesysteme zu konstruieren. Der Großteil der Elektroautos im Bestand hat noch eine Modulebene, obwohl es dafür keine Notwendigkeit gibt.
Wenn die Zellen statt in Module direkt ins äußere Gehäuse gebaut werden, heißt das Cell-to-Pack. Wenn das Batteriesystem zusätzlich eine tragende Funktion in der Fahrzeugkarosserie hat, nennt sich das bei BYD und anderen Herstellern Cell-to-Body. BYD (für Build Your Dreams) praktiziert das mit der Blade-Batterie zum Beispiel bei der Limousine Seal, die Ende des Jahres bei uns startet. Tesla hat für das gleiche Prinzip den Begriff Structural Pack eingeführt. Die gesamte Autoindustrie arbeitet daran. Inhaltlich geht es immer um das Gleiche. Siehe oben: Wenn der Anteil des Aktivmaterials hoch ist, steigt die Energiedichte, und die Kosten sinken.
Das war das Drumherum. Wie ist die Zelle aufgebaut?
In einer Batteriezelle gibt es Kathode, Anode und Elektrolyt. Die Kathode ist eine der beiden Elektroden in der Zelle. Hier werden positive Ionen entladen. Es findet eine Reduktionsreaktion statt. Die Anode ist die Gegenelektrode dazu. Hier wird oxidiert. Im Elektrolyt läuft der eigentliche Ladungstransport ab. Bei heutigen Elektroautos ist der Elektrolyt flüssig. Die Forschung arbeitet aber an halbfesten und festen Materialien für die gleiche Funktion, besser bekannt als Semi-Solid und All-Solid-State. Eine echte Festkörperzelle (das ist der deutsche Begriff) ist die Voraussetzung für eine Anode aus metallischem Lithium.
(Bild: Audi)
Welche Arten von Zellchemie sind heute üblich?
Im Serieneinsatz sind faktisch nur zwei grundsätzlich unterschiedliche Zellchemien zu finden: Solche mit einer Kathodenmischung aus Nickel, Mangan und Kobalt und dem Kürzel NMC. Die Industrie hat in den vergangenen Jahren unter anderem daran gearbeitet, den Anteil von Mangan und Kobalt im Verhältnis zu Nickel zu senken – vornehmlich aus Kostengründen.
Die zweite derzeit an Bedeutung gewinnende Zellchemie ist die Lithium-Eisenphosphat-Zellen (LFP). Sie ist preiswerter herzustellen und gilt als sehr zyklenfest. Allerdings ist sie schwerer als eine NMC-Zelle und lädt bei Kälte schlechter.
Was sind die Eigenschaften der NMC-Zellchemie?
Die Stärke von NMC-Zellen ist die besonders hohe Energiedichte. CATL reklamiert für die Qilin-Batterie eine gravimetrische Energiedichte von 255 Wattstunden pro Kilogramm (Wh/kg) für NMC. Das gleiche System kann auch mit LFP-Zellen bestückt werden. Der Vergleichswert liegt dann bei nur 160 Wh/kg. Bei der Energiedichte muss sauber zwischen Zell- und Systemebene unterschieden werden. Letztlich relevant ist die von CATL genannte Systemebene inklusive Crashstruktur sowie aktivem Temperaturmanagement. Die Zahlenwerte im Labor für eine Einzelzelle sind erheblich höher, und auch die volumetrischen Werte aus der Forschung können beeindrucken: Bis zu 700 Wattstunden pro Liter sind möglich.
(Bild: Audi)
Bei der Mischung von Nickel, Mangen und Kobalt an der Kathode gibt es inzwischen viele Variationen. Das Verhältnis dieser drei Metalle zueinander betrug vor zehn Jahren meistens 1 zu 1 zu 1. Hieraus ergab sich die Abkürzung NMC111 oder auch NMC333. Mittlerweile ist die Industrie dazu übergegangen, den prozentualen Anteil von Nickel schrittweise zu erhöhen. In typischen Serienautos sind NMC622 und NMC811-Zellen eingebaut, also mit 60 oder 80 Prozent Nickel. Weitere Steigerungen auf 90 Prozent (NMC955) sind in Arbeit. Eine Abwandlung der NMC-Zellchemie gibt es bei Tesla, wo lange NMA-Zellen mit Aluminium am häufigsten verkauft wurden.
Die wichtigsten Schwächen von Batteriezellen mit NMC-Kathode sind die vergleichsweise hohen Kosten – besonders wegen Nickel und Kobalt – und das Risiko des thermischen Durchgehens (thermal runaway). Die Fertigungsqualität muss darum hoch sein, und auch die Überwachung und Temperierung im System muss perfekt funktionieren.
Und LFP-Zellen?
LFP-Zellen sind wegen der Materialien Eisen und Phosphat preisgünstiger als NMC-Zellen. Sie sind außerdem in jeder Hinsicht robust und unempfindlich. Das Risiko des thermischen Durchgehens zum Beispiel ist sehr niedrig. Aber die Energiedichte ist erheblich geringer und in der Folge die Reichweite. Wahrscheinlich hätte niemand LFP-Zellen so richtig ernst genommen, wenn nicht Tesla das Dogma der maximalen Energiedichte als wichtigstem Kriterium durchbrochen hätte: In Model 3 und Model Y kommen in den Basisversionen LFP-Zellen zum Einsatz. Beispiel Model 3: Die Reichweite beträgt mit LFP-Zellen 491 statt 602 km. Ein Minus, das viele Kunden für verkraftbar halten, wenn nur der Preis stimmt. Aktuell beträgt die Differenz 9000 Euro.
Tesla hat es auch geschafft, das Kälteproblem von LFP-Zellen so klug wie möglich zu steuern: Bei Frost können sie nicht geladen werden. Nach dem Start des Ladevorgangs wird zuerst geheizt, bevor der Strom fließt. Die ideale Zieltemperatur der Vorkonditionierung im Routenplaner ist mit über 40 Grad erheblich höher als bei NMC-Zellen, wo es je nach Zusammensetzung rund 25 Grad sind. Teslas Vorheizung beseitigt die Schwäche von LFP zwar nicht, ermöglicht aber den Alltag. Die gesamte Autoindustrie zieht derzeit nach und bietet Elektroautos an, die in der Basisversion LFP-Zellen und bei teuren Varianten NCM-Zellen verkauft. Eine Ausnahme gibt es: BYD produziert ausschließlich LFP-Zellen und ist darauf spezialisiert.
(Bild: CATL)
Wie gut ist die Dauerhaltbarkeit?
Batteriezellen altern zyklisch – nach der Zahl der Ladevorgänge – und kalendarisch, also mit den Jahren. Nach einer Analyse von Prof. Dr. Markus Hölzle vom Zentrum für Sonnenenergie- und Wasserstoff-Forschung (ZSW) beträgt die typische Dauerhaltbarkeit von NMC-Zellen 2000 Zyklen und zwölf Jahre. Bei LFP-Zellen sind es 3000 Zyklen und 19 Jahre. Zellen, die Natrium statt Lithium verwenden, könnten das Doppelte davon erreichen. Multipliziert man die Zahl der Zyklen mit der Reichweite, erhält man die kilometrische Lebenserwartung. Bei NMC also zum Beispiel:
2000 Zyklen mal 300 Kilometer = 600.000 km.
Bestimmte Umstände können die Dauerhaltbarkeit drastisch mindern: Das schnelle Laden bei Kälte etwa ruiniert die Zyklenfestigkeit. Gute Elektroautos haben darum aufwendige Heiz- und Kühlsysteme, die die Zellen schonen.
Welche Veränderungen sind bei der Kathode bis 2030 zu erwarten?
Bei NMC-Zellen setzt sich die Verschiebung zu immer höherem Nickelanteil bei immer weniger Kobalt fort. LFP-Zellen werden möglicherweise zu LFMP-Zellen (M für Mangan) modifiziert – vielleicht werden noch in diesem Jahr Elektroautos mit LFMP-Zellen präsentiert, die eine bessere Energiedichte als LFP haben.
Der größte Fortschritt wird in diesem Jahrzehnt jedoch an der Anode stattfinden. Derzeit haben fast alle Elektroautos eine Anode aus Grafit. Grob vereinfacht ist Grafit das, was die Batterie schwer macht und eine höhere Ladegeschwindigkeit verhindert. In naher Zukunft wird dem Grafit darum Silizium beigemischt. Beim Porsche Taycan und dem Audi e-tron GT ist das jetzt schon im kleinen einstelligen Prozentbereich der Fall. Wissenschaftler halten bis zu 20 Prozent Siliziumanteil für machbar.
(Bild: Volkswagen)
Die Energiedichte und die Ladegeschwindigkeit würden hierdurch erheblich ansteigen. Im Zusammenspiel mit leistungsfähigen Heiz- und Kühlsystemen prognostizieren die meisten Autohersteller eine Verkürzung der Ladezeit von zehn auf 80 Prozent Ladestand von heute durchschnittlich rund 30 Minuten auf gut zehn Minuten bis Ende des Jahrzehnts.
Batteriezellen mit einer Siliziumbeimischung an der Anode sind die härtesten Konkurrenten von echten Festkörperzellen, weil sie deren Eigenschaften fast erreichen, ohne Probleme bei der Produktion zu verursachen. Echte Festkörperzellen haben eine Anode aus rein metallischem Lithium. Das ist hochreaktiv und schwer zu handhaben. Ein fester Elektrolyt ist die Voraussetzung zur erfolgreichen und gefahrlosen Umsetzung. Viele Batteriehersteller reden zwar öffentlich von Solid State-Zellen, meistens sind aber teilfeste Elektrolyte wie Gele oder weiche Pulver gemeint. Sie stellen lediglich eine Modifikation des aktuellen Aufbaus dar, während eine Festkörperzelle mit einer metallischen Lithium-Anode eine Revolution wäre.
Kann Natrium Lithium ersetzen?
Ja. CATL und andere haben angekündigt, Natrium- statt Lithium-Ionenzellen zu bauen. Der Produktionsanlauf soll noch in diesem Jahr stattfinden. Natrium-Ionenzellen können auf den gleichen Anlagen gefertigt werden wie die mit Lithium. Sie verwenden aber neben einem anderen Alkalimetall auch andere Materialien an der Anode (amorpher Kohlenstoff oder auch Englisch Hard Carbon) und der Kathode (zum Beispiel die Farbstoffe Preußisch Blau oder Weiß). Das Resultat: Nach den Berechnungen von Prof. Dr. Hölzle am ZSW betragen die Kosten pro Kilowattstunde Energieinhalt auf Systemebene bei Natrium-Ionen-Zellen 84 Euro. Bei LFP-Zellen sind es 123 Euro/kWh und bei NMC811-Zellen 152 Euro/kWh.
Die Energiedichte von Natrium-Ionenzellen ist sehr niedrig. In einer zweiten Entwicklungsstufe verspricht CATL trotzdem 200 Wh/kg und damit ein Niveau, das selbst für aktuelle LFP-Zellen ehrgeizig ist. Wann solche Zellen serienreif sind, sagt CATL dagegen nicht. Klar ist, dass Natrium-Ionen-Zellen vor allem in Konkurrenz zu LFP-Zellen gehen, weil der niedrige Preis das wichtigste Auswahlkriterium ist. Außerdem haben sie viel bessere Kälteeigenschaften und halten noch länger. Eins der ersten serienmäßigen Elektroautos mit Natrium-Ionen-Zellen im Batteriesystem wird der BYD Seagull sein. Ein Kleinwagen im Format eines VW Golf 1, der vielleicht auch bald in Europa verkauft wird.
Wie geht es weiter?
Die Forschung wird weiter an der Verbesserung der Zellchemie arbeiten, um den Zielkonflikt aus niedrigen Kosten, hoher Sicherheit und guten Leistungseigenschaften zu lösen. Eine Revolution etwa durch Festkörperzellen ist aus jetziger Perspektive unwahrscheinlich. Stattdessen wird es viele kleine kontinuierliche Verbesserungsschritte geben – und leider sitzen die Treiber des Fortschritts nicht in Europa, sondern in China.
(mfz)